www.magazine-industry-usa.com
10
'25
Written on Modified on
Yamaha Robotics delivers flexible automation boosting customer’s output
LCMR200 linear transfer system elevates reliability in automotive parts production and introduces future-proof flexibility to handle changing market demands.
www.yamaha-motor.com
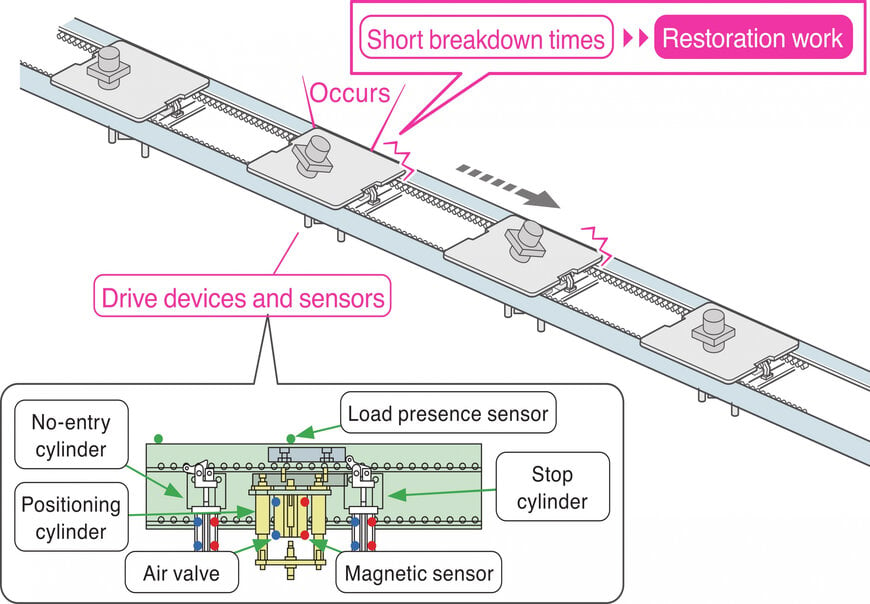
Conventional production line with conveyor-based transfer experienced frequent stoppages.
Yamaha Motor Robotics FA Section has delivered a 10% uplift in output for a customer manufacturing automotive parts, by superseding conventional conveyors with a system comprising LCMR200 modules.
The customer chose the LCMR200 to overcome a specific challenge in the factory by eliminating large numbers of position sensors and electromechanical stoppers needed to control their existing conveyors. These conveyors would routinely encounter about 15 short stoppages per day due to component failures. Although easily fixed within just a few minutes on each occasion, often requiring a simple reset command, the total productive time loss per shift noticeably affected the overall productivity.
The production team started a project to increase output by preventing stoppages caused by the conveyors, seeking new and more reliable equipment capable of operating continuously for extended periods. After analysing the market, the team discovered that the LCMR200 is highly regarded by many other companies facing similar challenges. After arranging a demonstration from Yamaha, they were impressed with the design that minimizes the number of driving devices and sensors while ensuring accurate and precise control. The LCMR200’s uncomplicated architecture, based on electronically controlled and programmable linear motors, ensures outstanding reliability.
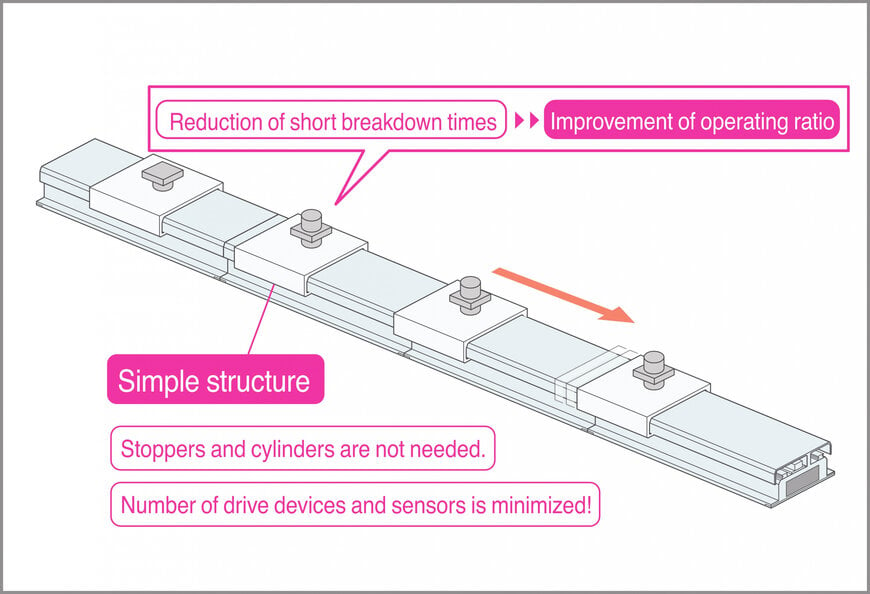
The LCMR200 modules eliminated the causes of conveyor breakdowns, transforming productivity.
As a modular system for workpiece transport in automated production lines, the LCMR200 transfers workpieces quickly and efficiently between the different processes needed to assemble and package all kinds of products, especially small engineering parts like the automotive components in this example. The modules are equally suited to manual production lines staffed by human workers, and partially or fully automated production, offering fast, quiet, and safe operation. The speed, acceleration/deceleration, stop positions and even direction are all programmable, permitting fast setup as well as flexibility to adapt as manufacturing demands change.
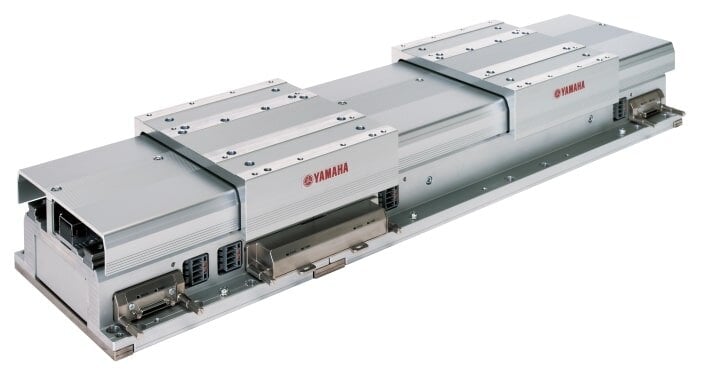
The LCMR200 modules are reliable, fast, and flexible.
The production team manufacturing automotive components quickly decided the LCMR200 was the way forward, to raise production and meet the needs of their demanding customers. Yamaha worked the team to ensure a smooth project and introduced a system integrator with the skills to create a fully engineered production line to replace conventional, conveyor-based production with the LCMR200.
Now in operation, the new production line has demonstrated 100% reliability, completely eliminating the regular stoppages that proved so disruptive in the past. Working with the same line rate and process-cycle times as before, the new line is producing an extra 5400 units per month. That an increase of 10.3% in output, simply through increased uptime.
The LCMR200 has more performance to unleash as the team gains familiarity with the new production line. The maximum speed of 2.5 m/s permits much faster transfer times than conveyors, in a wide variety of industrial scenarios. The line length can be scaled by increasing or decreasing the number of modules. The mechanical and electrical connections are quick to install and the sliders have individual identities that allow connecting and controlling up to 64 units simultaneously. The total height of the module and slider is 109mm, allowing a low profile, while the overall width of 175mm ensures the installed production line has a compact footprint.
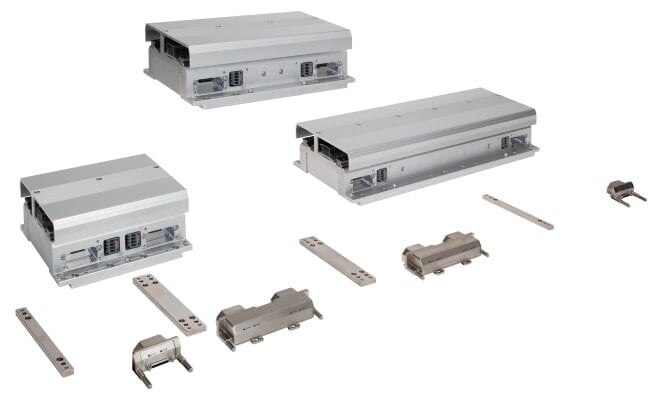
The LCMR200 system permits fast and easy installation.
Special modules for circulation and traversing are available that let integrators build compact production lines and allow branching or overtaking to change the sequence of processes if required. This can be helpful, for example if factory floorspace is extremely limited, or if individual production workpieces need to be diverted for special processes such as personalizing or applying customer-specified options. The sliders can carry up to 30kg and their high rigidity allows production processes to be performed directly on the module. This can save removing and returning workpieces to the sliders, which permits fast and efficient cycle times as well as minimising engineering and tooling costs.
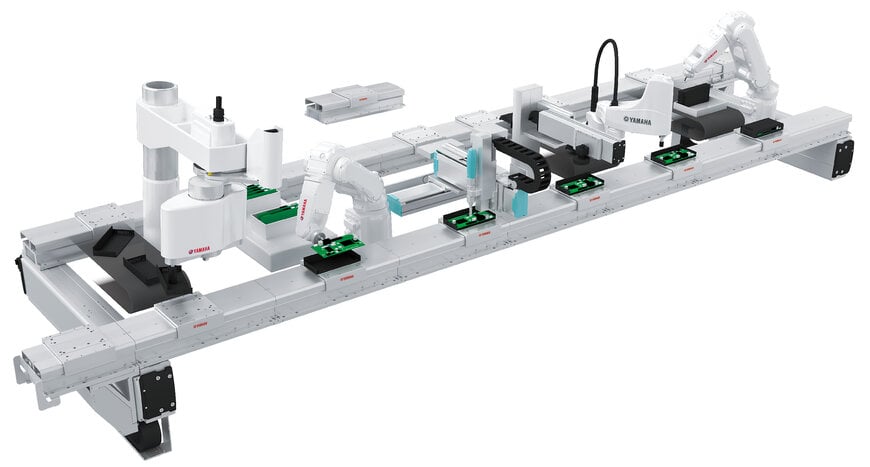
The LCMR200 linear transfer system supports manual or automated assembly and allows operation directly on the sliders.
“Close cooperation between Yamaha, the system integrator, and the customer delivered a fast and reliable solution that totally fulfilled the requirement for uninterrupted production, increased output, and greater productivity,” said Tatsuro Katakura, FA Section Sales Manager, Yamaha Motor Robotics Europe. “Moreover, the LCMR200 has many additional benefits to offer this customer as they gain familiarity and explore its full performance and flexibility. I am sure they will consolidate their future plans on the LCMR200 as they evolve and expand their product lines and introduce new production processes in the future.”
“While offering tremendous reliability, the LCMR200 system is also supremely flexible and can help owners handle diverse challenges that all companies face over time, including frequent new product introductions, market expansion, and technological change,” he concluded.
www.yamaha-motor-robotics.com
Yamaha Motor Robotics FA Section has delivered a 10% uplift in output for a customer manufacturing automotive parts, by superseding conventional conveyors with a system comprising LCMR200 modules.
The customer chose the LCMR200 to overcome a specific challenge in the factory by eliminating large numbers of position sensors and electromechanical stoppers needed to control their existing conveyors. These conveyors would routinely encounter about 15 short stoppages per day due to component failures. Although easily fixed within just a few minutes on each occasion, often requiring a simple reset command, the total productive time loss per shift noticeably affected the overall productivity.
The production team started a project to increase output by preventing stoppages caused by the conveyors, seeking new and more reliable equipment capable of operating continuously for extended periods. After analysing the market, the team discovered that the LCMR200 is highly regarded by many other companies facing similar challenges. After arranging a demonstration from Yamaha, they were impressed with the design that minimizes the number of driving devices and sensors while ensuring accurate and precise control. The LCMR200’s uncomplicated architecture, based on electronically controlled and programmable linear motors, ensures outstanding reliability.
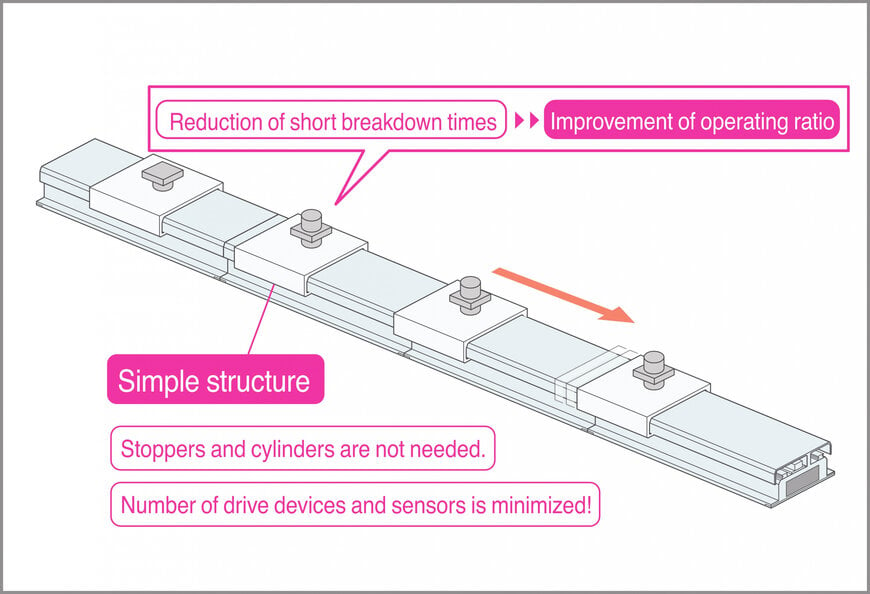
The LCMR200 modules eliminated the causes of conveyor breakdowns, transforming productivity.
As a modular system for workpiece transport in automated production lines, the LCMR200 transfers workpieces quickly and efficiently between the different processes needed to assemble and package all kinds of products, especially small engineering parts like the automotive components in this example. The modules are equally suited to manual production lines staffed by human workers, and partially or fully automated production, offering fast, quiet, and safe operation. The speed, acceleration/deceleration, stop positions and even direction are all programmable, permitting fast setup as well as flexibility to adapt as manufacturing demands change.
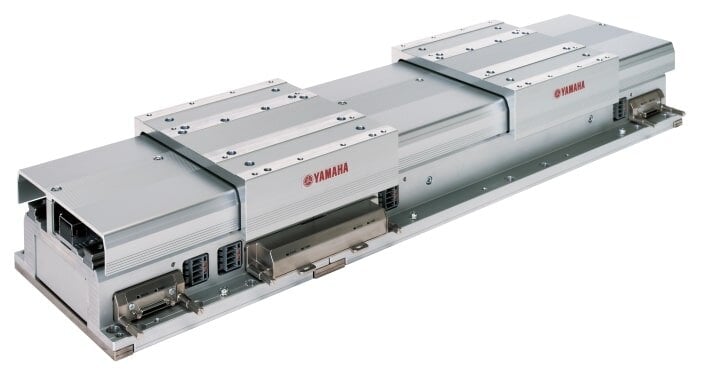
The LCMR200 modules are reliable, fast, and flexible.
The production team manufacturing automotive components quickly decided the LCMR200 was the way forward, to raise production and meet the needs of their demanding customers. Yamaha worked the team to ensure a smooth project and introduced a system integrator with the skills to create a fully engineered production line to replace conventional, conveyor-based production with the LCMR200.
Now in operation, the new production line has demonstrated 100% reliability, completely eliminating the regular stoppages that proved so disruptive in the past. Working with the same line rate and process-cycle times as before, the new line is producing an extra 5400 units per month. That an increase of 10.3% in output, simply through increased uptime.
The LCMR200 has more performance to unleash as the team gains familiarity with the new production line. The maximum speed of 2.5 m/s permits much faster transfer times than conveyors, in a wide variety of industrial scenarios. The line length can be scaled by increasing or decreasing the number of modules. The mechanical and electrical connections are quick to install and the sliders have individual identities that allow connecting and controlling up to 64 units simultaneously. The total height of the module and slider is 109mm, allowing a low profile, while the overall width of 175mm ensures the installed production line has a compact footprint.
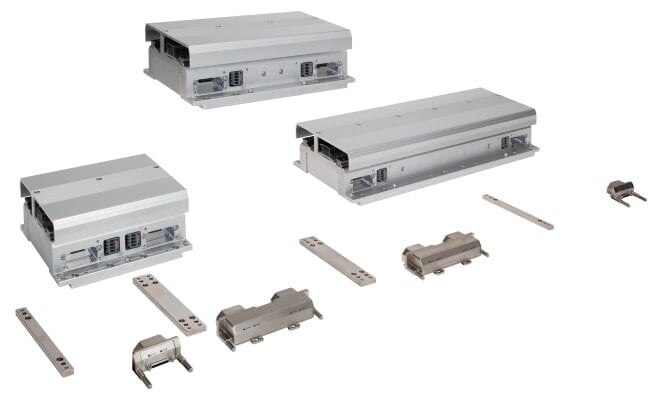
The LCMR200 system permits fast and easy installation.
Special modules for circulation and traversing are available that let integrators build compact production lines and allow branching or overtaking to change the sequence of processes if required. This can be helpful, for example if factory floorspace is extremely limited, or if individual production workpieces need to be diverted for special processes such as personalizing or applying customer-specified options. The sliders can carry up to 30kg and their high rigidity allows production processes to be performed directly on the module. This can save removing and returning workpieces to the sliders, which permits fast and efficient cycle times as well as minimising engineering and tooling costs.
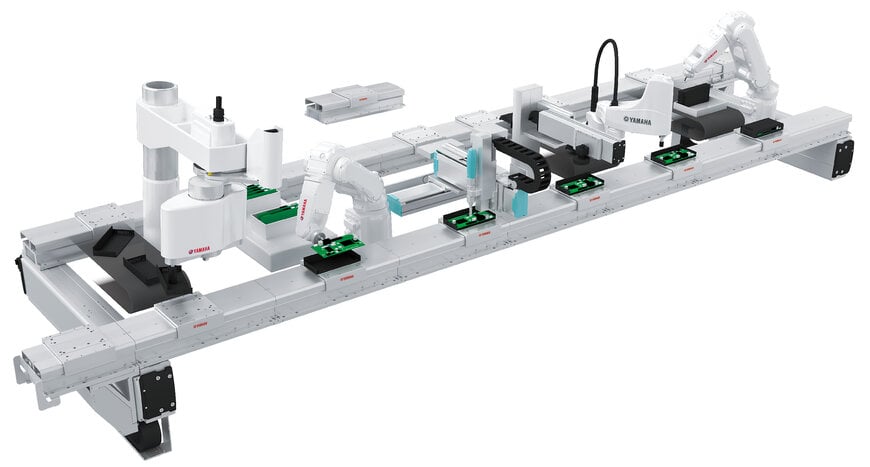
The LCMR200 linear transfer system supports manual or automated assembly and allows operation directly on the sliders.
“Close cooperation between Yamaha, the system integrator, and the customer delivered a fast and reliable solution that totally fulfilled the requirement for uninterrupted production, increased output, and greater productivity,” said Tatsuro Katakura, FA Section Sales Manager, Yamaha Motor Robotics Europe. “Moreover, the LCMR200 has many additional benefits to offer this customer as they gain familiarity and explore its full performance and flexibility. I am sure they will consolidate their future plans on the LCMR200 as they evolve and expand their product lines and introduce new production processes in the future.”
“While offering tremendous reliability, the LCMR200 system is also supremely flexible and can help owners handle diverse challenges that all companies face over time, including frequent new product introductions, market expansion, and technological change,” he concluded.
www.yamaha-motor-robotics.com