www.magazine-industry-usa.com
27
'16
Written on Modified on
Makino DA300: The precise 5-axis vertical machining centre delivering the same productivity as a horizontal machining centre.
Kirchheim unter Teck, September 2016. – Makino launches DA300 – the latest 5-axis vertical machining centre. The DA300 provides an ideal blend of speed, precision and flexibility for multi-axis complex workpieces in the smallest of machine footprints. Inspired by the best design characteristics from both vertical and horizontal machining centres, the DA300 combines the structural rigidity and accuracy of a vertical centre with the high produc-tivity and reliability of a horizontal centre, offering the best-of-both-worlds. It significantly reduces the part cycle times while achieving very accurate per-formance.
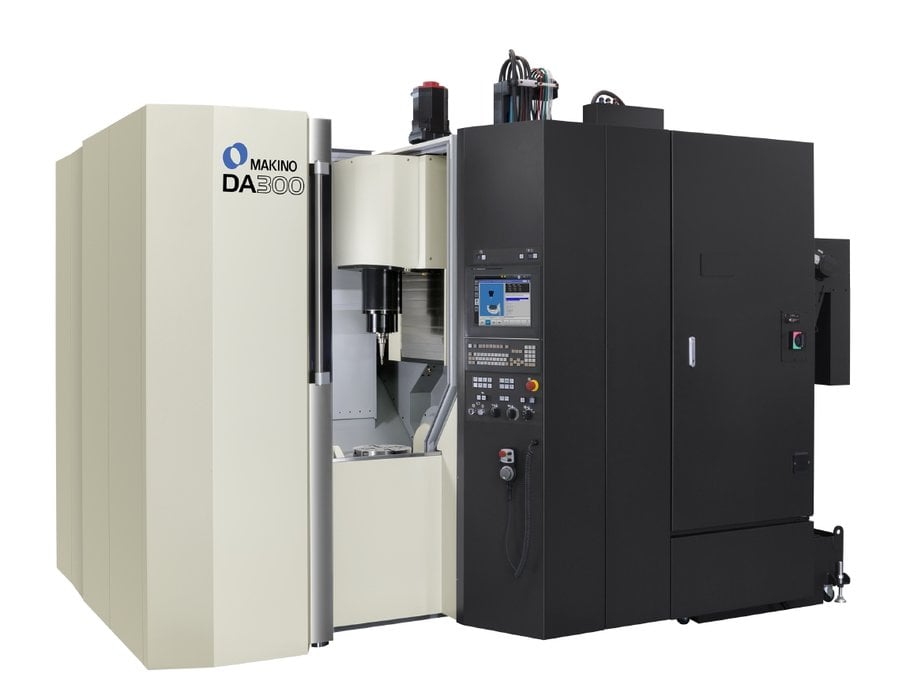
Target markets
The DA300 is aimed at the parts production industry. Target markets include manufacturers of industrial components such as hydraulic and pneumatic components, aluminium die-casted parts and the likes. This machining centre is ideal for all who produce high-precision, geometrically complex parts and prototypes e.g. manufactures and job-shoppers from various industries like automobile, medical, photonics, racing and luxury car industries, and energy. The DA300 would also be of interest to aerospace component manufacturers, especially small structural parts, satellite components, and engine components such as blisks, impellers, and blades.
Machine rigidity
The DA300 is based on the half-bridge structure traditionally used in the Makino vertical machines. With the direct-drive (DD) motors designed for the A-axis and C-axis, the machine offers excellent dynamic motion control and a five-side access for production of complex parts in less setups. The double-side supported table is embedded in a highly rigid frame structure making the machine rigid but light, enabling increased dynamics, acceleration and maximum speeds without compromising on performance. The DD motors also bring the benefit of high-speed rotation, even with a maximum table load of 250 kg. Additionally, well-dimensioned 45 mm wide roller guides and core-cooled ball screws with 40 mm diameter increase the stability of the machine.
Reduction of cutting and non-cutting times
Keeping in mind the production sector, productivity of the DA300 is excel-lent. Equipped with a highly dynamic, 20,000 rpm, HSK-A63 spindle, the machine reduces the cutting time needed for rigorous milling, drilling and tapping operations. A standard 60-tool magazine and a well-proven Automatic Tool Changer (ATC) unit inspired from the popular Makino a1nx series horizontal machining centre (HMC) performs with great reliability and delivers with 3.5 seconds chip-to-chip time. The ATC shutter mechanism is driv-en by a servo motor, which is not only highly reliable but also simplifies the set-up, reducing the tool-changing time. The DA300 also features the Vision Broken Tool Sensor (Vision B.T.S) as a standard equipment. This broken-tool sensor validates the cutting-tool condition after every tool change. The Vision B.T.S. system has minimal moving parts and require no physical con-tact with the cutting tool allowing for enhanced, long-term reliability and less risk of chipping delicate tool materials, such as polycrystalline diamond (PCD). It creates a silhouette of the cutting tool and detects the length, size and approximate weight of the tool.
Intelligent functionality
With Makino’s latest Professional 6 (PRO 6) controller, the DA300 is equipped with several intelligent functions to increase productivity of the machine. The controller was developed to meet customer needs for enhanced machining processes through improved safety, ease of operation, reliability and productivity.
It achieves these goals by reducing the collision risk, streamlining and facilitating operability, including many previously optional functions as standard features, and bettering machine performance. The controller has been de-signed for easy, intuitive operation via simplified menus and smartphone-like icons.
The new advanced motion control Geometric Intelligence (GI) functions re-duce overall cycle time, especially in typical production components. GI Drilling enables the spindle and tool to arc from hole to hole instead of following a square path. This reduces non-cutting times in comparison to common hole-pattern drilling. On the other hand, GI Milling is designed to improve performance in 2-D milling. It lets the user define a corner-rounding tolerance on each milling path.
Other intelligent machine functions include Inertia Active Control (IAC) de-signed to further speed up machine motions based upon system dynamic attributes. The IAC gets feedback from the servomotors and sets the acceleration and deceleration of the specific pallet at the optimum level.
Enhanced operability without foregoing ease and safety
All the enhanced productivity comes with state-of-the-art safety measures, thanks to Collision Safe Guard (CSG), a most advanced real-time collision prevention system that is particularly important and effective in 5-axis applications. Statistically speaking, the most frequent cause of spindle damage is a collision. The main contributory factors are mistakes in operating, setting and editing, and tooling and clamping – all mistakes that occur on the ma-chine itself. The collision safeguard takes real machine conditions into consideration to prevent collisions.
Excellent coolant management and chip evacuation
The importance of effective coolant management is often underestimated in vertical machining centres (VMC), even though it is an absolute necessity if a machine is intended for high productivity levels and consequently generates high volumes of chips per minute. Contrary to the conventional 5-axis trunnion type table setup, where there are two narrow troughs on each side of the trunnion for chip removal, the DA300 has a wide-open trunnion and a wide trough located beneath the table. This ensures that chips fall directly in to the trough. The coolant management system in the DA300 is outstanding. A generous flow of coolant from the overhead shower and terrace washing coolant system eliminates accumulation of chips and enables excellent evacuation.
Operational accuracy and thermal control
Makino machines are renowned for their thermal control technology – the DA300 is no exception. A thermally symmetrical structure is combined with effective heat removal from the spindle, support structures like the ball screws and motors, to ensure the machine’s stability and machining accuracy during long hours of operation.
Ready for automation
The DA300 is ready for integration into automated production cells. The table (340 mm by 300 mm) has 5 pneumatic ports (hydraulic as option) which makes it ready for handling pallets, providing quick, efficient part exchange and maximizing machine utilization. It offers easy access to the table from the side so as not to interfere with front operation, and to accommodate different automation possibilities from standard zero-point clamping systems to direct part handling with hydraulic clamping.
All in all, this 5-axis VMC delivers an unmatched combination of high productivity, quality and operational safety combined with intuitive ease of use.
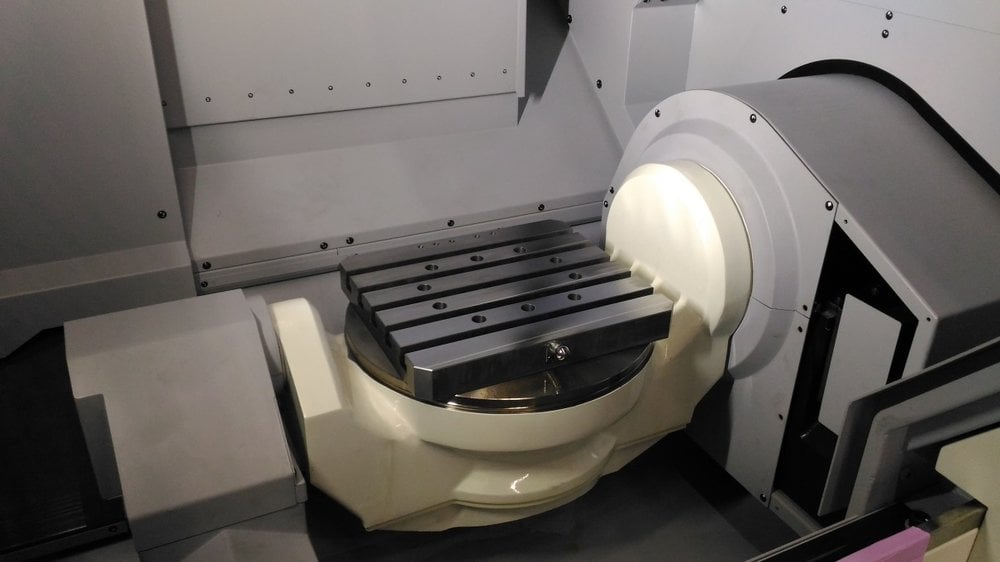
Image 2: Rigid and dynamic 5-axis table
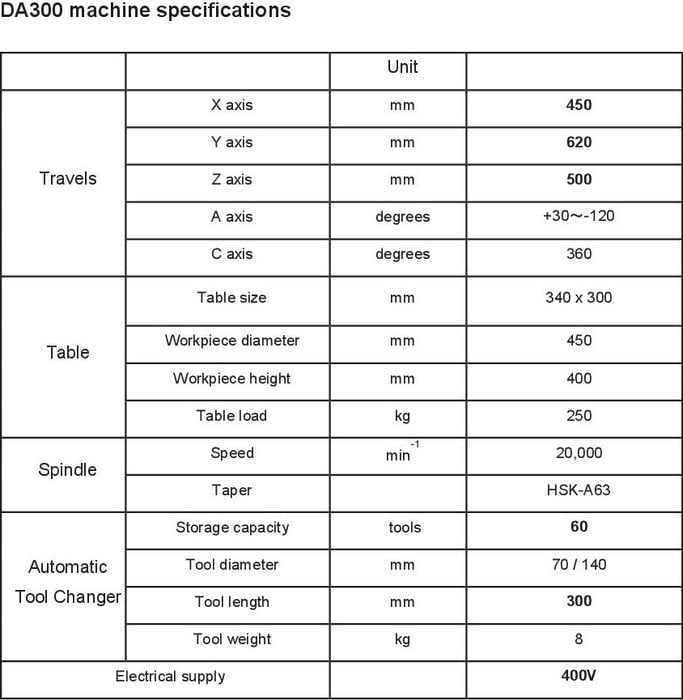