www.magazine-industry-usa.com
11
'24
Written on Modified on
Energy efficiency booster for deep drawing presses
Servo-hydraulic drive solution from Bosch Rexroth increases energy efficiency of deep drawing presses and conserves resources.
www.boschrexroth.com
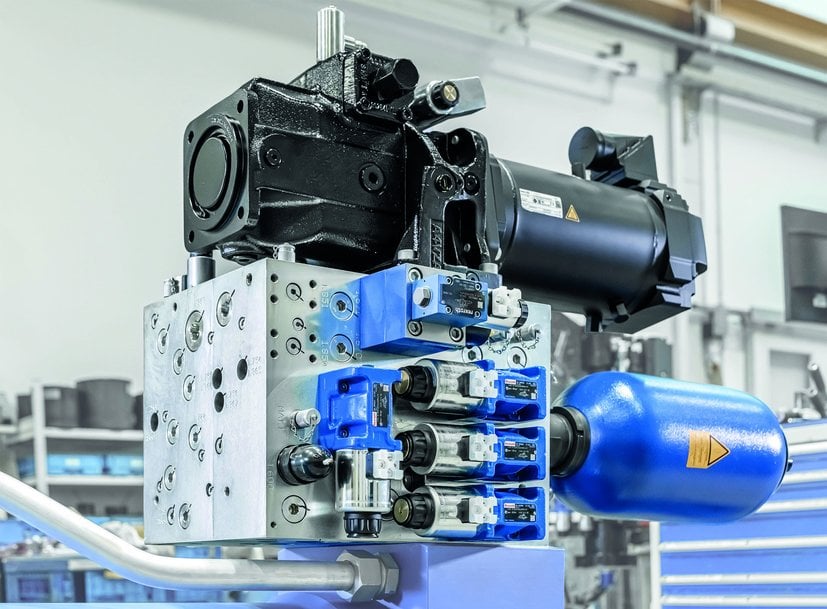
With its servo-hydraulic drive solution, Bosch Rexroth is increasing efficiency in sheet metal forming. Recuperation (energy recovery) can increase the energy efficiency of deep drawing presses by up to 30 percent. The modular design simplifies engineering and installation for the machine manufacturer. End customers also benefit from reduced oil volume and smaller installation space. Sheet metal can be formed with increased productivity and quality. At the same time, the solution opens up more opportunities for digitalization. End users can minimize downtimes with condition monitoring, for example.
Modern deep drawing presses should form sheet metal with consistently high quality and productivity and require as little energy as possible. At the same time, machine manufacturers require standardized drive concepts in order to be able to implement a wide range of applications economically. In particular, engineering and installation costs need to be reduced.
The servo-hydraulic drive solution from Bosch Rexroth offers many advantages here. The modules comprising a servo-hydraulic pump unit and control block can be used to supply the die cushion and upper ram as required. If both servo-hydraulic solutions are operated with a common electric drive system, such a deep-drawing press achieves energy savings of up to 30 percent compared to a conventional hydraulic press with valve control.
The significant increase in energy efficiency is made possible on the one hand by the speed-controlled servomotor pump unit for the upper ram, which provides the exact power required at every point in the press cycle. On the other hand, during deep drawing, part of the process energy can be recovered via the servomotor pump unit in the die cushion, which regulate the die cushion force instead of a valve control. The recovered electrical energy can either be fed back into the grid or provided to the upper ram via the common DC bus. This reduces the energy consumption of the machine directly during the drawing process.
Furthermore, the servo-hydraulic drive solution opens up additional possible savings by minimizing the cooling requirements of the hydraulic unit. The reason for this is the high level of efficiency and the drastic reduction in throttle losses, which leads to less heating of the hydraulic oil. As a result, the power unit can be designed smaller and in some cases it can work without any cooling at all, which further reduces investment and operating costs.
More productivity, quality and transparency
The digital control of the servo-hydraulic drive has a positive effect on process quality and transparency as well as productivity. As the individual pressures, positions, velocities and forces can be controlled very precisely, sheet metal parts can be produced with repeated accuracy and higher quality. For example, the upper ram drive can also operate at very low motor speeds of just a few rotations per minute. At the same time, the fast-reacting servomotors enable shorter cycle times and higher output. Various pump options with 2-point or proportional adjustment systems through to multi-quantum control further expand the design scope, making the energy-saving drive concept attractive for many other applications.
The servo-hydraulic drive also enables data-based analyses for process optimization and condition monitoring to minimize downtimes.
Modern deep drawing presses should form sheet metal with consistently high quality and productivity and require as little energy as possible. At the same time, machine manufacturers require standardized drive concepts in order to be able to implement a wide range of applications economically. In particular, engineering and installation costs need to be reduced.
The servo-hydraulic drive solution from Bosch Rexroth offers many advantages here. The modules comprising a servo-hydraulic pump unit and control block can be used to supply the die cushion and upper ram as required. If both servo-hydraulic solutions are operated with a common electric drive system, such a deep-drawing press achieves energy savings of up to 30 percent compared to a conventional hydraulic press with valve control.
The significant increase in energy efficiency is made possible on the one hand by the speed-controlled servomotor pump unit for the upper ram, which provides the exact power required at every point in the press cycle. On the other hand, during deep drawing, part of the process energy can be recovered via the servomotor pump unit in the die cushion, which regulate the die cushion force instead of a valve control. The recovered electrical energy can either be fed back into the grid or provided to the upper ram via the common DC bus. This reduces the energy consumption of the machine directly during the drawing process.
Furthermore, the servo-hydraulic drive solution opens up additional possible savings by minimizing the cooling requirements of the hydraulic unit. The reason for this is the high level of efficiency and the drastic reduction in throttle losses, which leads to less heating of the hydraulic oil. As a result, the power unit can be designed smaller and in some cases it can work without any cooling at all, which further reduces investment and operating costs.
More productivity, quality and transparency
The digital control of the servo-hydraulic drive has a positive effect on process quality and transparency as well as productivity. As the individual pressures, positions, velocities and forces can be controlled very precisely, sheet metal parts can be produced with repeated accuracy and higher quality. For example, the upper ram drive can also operate at very low motor speeds of just a few rotations per minute. At the same time, the fast-reacting servomotors enable shorter cycle times and higher output. Various pump options with 2-point or proportional adjustment systems through to multi-quantum control further expand the design scope, making the energy-saving drive concept attractive for many other applications.
The servo-hydraulic drive also enables data-based analyses for process optimization and condition monitoring to minimize downtimes.
www.boschrexroth.com