www.magazine-industry-usa.com
15
'15
Written on Modified on
Increased productivity and process reliability at MTU Aero Engines due to Safe-Lock
Due to the positive form and frictional clamping system made by HAIMER, MTU Aero Engines in Munich was able to increase the reliability in the process of machining difficult-to-cut materials while also decreasing their processing times.
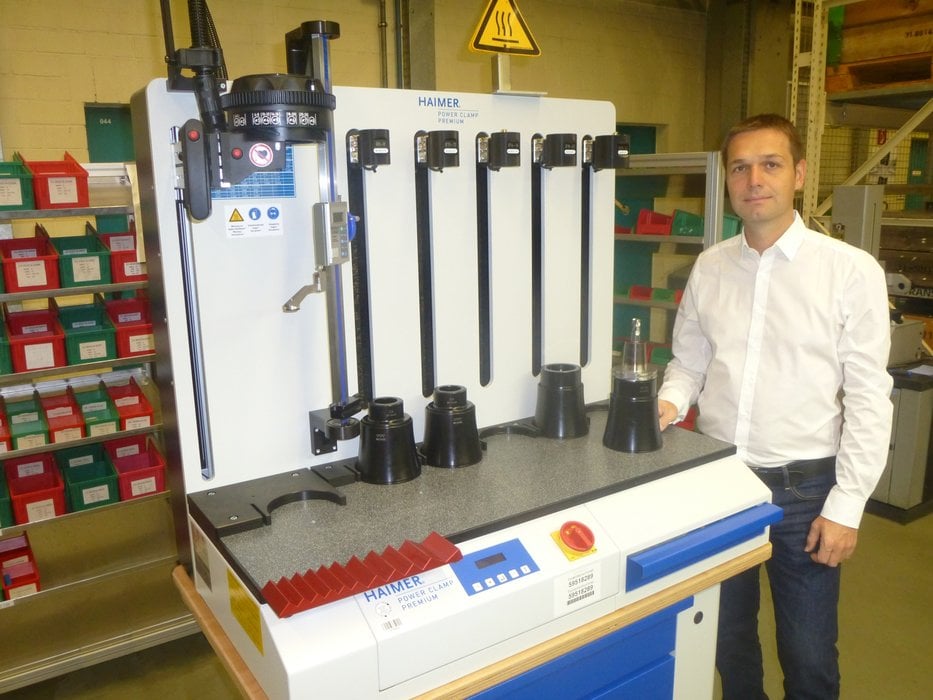
Due to Safe-Lock™-shrink fit chucks and the shrink fit machine Power Clamp Premium NG from HAIMER, Alexander Steurer, Senior Manager NC-Programming Stator Components at MTU, accomplishes heavy duty machining of high-temperature materials with excellent runout accuracy and maximum pull out protection.
Picture: HAIMER
MTU Aero Engines is Germany’s leading engine manufacturer and an established global player in the industry. The company engages in the design, development, manufacturing and support of commercial and military aircraft engines in all thrust and power categories and stationary gas turbines. Due to HAIMER‘s patented Safe-Lock™pull out protection system, MTU was able to optimize their machining process regarding the production of structural frames and castings.
Jet engines are high-tech products. In their production, innovative technologies and processes are used. To keep current technologically, MTU develops innovative manufacturing strategies, and if necessary obtains additional external expertise. So was the case when they contacted HAIMER, the tool holding specialists from Igenhausen, Germany, to help optimize the demanding machining process of manufacturing frames and castings.
Difficult-to-machine materials, high-quality components and the high degree of automation at MTU require an absolutely smooth and reliable machining process to maintain the highest levels of quality. In order to ensure this consistency and to control the high axial cutting forces during machining, MTU decided to implement the Safe-Lock™ pull out protection system by HAIMER.
In the HAIMER Safe-Lock™ system, special drive keys in the tool holder and grooves in the tool shank prevent the cutting tool from spinning during extreme machining, thus preventing tool pull out from the chuck. In addition to the frictional clamping forces of the selected clamping system, the cutting tool is held using positive form locking in the tool holder through the constructive design of the Safe-Lock™ system.
Alexander Steurer, Senior Manager NC-Programming Stator Components at MTU Aero Engines AG in Munich, explains the decision for the HAIMER system: “Through the introduction of Safe-Lock™ and the shrinking technology from HAIMER, we can guarantee process reliability even with milling challenging high temperature materials. This is a prerequisite to guarantee smooth processing during manufacturing of frames and castings, given our high degree of automation.“
The combination of pull-out protection and highest concentricity of the Safe-Lock™ system leads to low vibration and as a result, a very stable machining process. Due to the increased cutting depths and feeds, the metal removal rate can be increased significantly. And thanks to the improved runout accuracy of HAIMER shrink fit chucks, tool life is improved by up to 50%.
The benefits of less than 3 µm runout, that the symmetrical Safe-Lock™ design provides, coupled with optimum balance and the possibility for easy length presetting were substantial reasons for MTU to switch to the HAIMER system instead of continuing to use Whistle Notch or Weldon tooling systems. While these other systems do in fact prevent tool pull out, both are unsymmetrical by design, hence providing insufficient runout and balance accuracy.
Through the use of a set screw the cutting tool is wedged against the opposite wall of the clamping bore. The holder pushes the cutting tool off center and thereby leads to excessive amounts of runout. Any such design also allows for significant radial play between the tool shank and the bore itself. That way the aforementioned holders actually push the cutting tool off center, thereby inducing excessive amounts of runout. Hans Drahtmüller, Line Manager Machining Stator Components at MTU in Munich, explains the resulting problems: “Due to the deteriorated runout, the tool life could not be fully realized. As a result, the tools with a Weldon flat had to be exchanged early. With Safe-Lock™ regrinding could be automated due to the cylindrical form of the system, as the cutting tools no longer have to be inserted manually into the grinding machine compared to Weldon flat tooling. This saves tool costs!“
Easy and quick tool change
In addition to productivity improvements in the machining process, time is also saved outside of the machine via extremely fast and easy tool changes. HAIMER Power Clamp Premium NG, the high end shrink fit machine MTU is using currently, offers an ergonomic working space, perfect handling and linear guided cooling bodies with temperature monitoring for maximum safety. Presetting the tool length to exactly 0.02 mm (e.g. for sister tools) can optionally be integrated into this machine. The intelligent New Generation (NG) coil is adjustable. With one turn, you can set the coil to the size of the shrink fit chuck both in length and diameter. This new system obsoletes the former interchangeable ferrite stop disks, which were always at risk of breaking during change overs. Thanks to the multiple patented HAIMER technology, the shrink fit chuck is only heated in areas where it is necessary. This way the process of both heating and cooling the tool holders is much faster. During the cooling process different sized cooling bodies shorten the cooling time and create a gentle, even and clean cooling effect. The cooling bodies ride on linear guides, so that the cutting edges are always protected from collision with the cooling body.
MTU Aero Engines
MTU Aero Engines AG is Germany’s leading aero engine manufacturer. The company is a technological leader in low-pressure turbines, high-pressure compressors, turbine center frames as well as manufacturing processes and repair techniques. In the commercial OEM business, the company plays a key role in the development, manufacturing and marketing of high-tech components together with international partners. In the commercial maintenance sector the company ranks among the top 5 service providers for commercial aircraft engines and industrial gas turbines. The activities are combined under the roof of MTU Maintenance. In the military area, MTU Aero Engines is Germany's leading industrial company for practically all engines operated by the country's military, the German Bundeswehr. MTU operates a network of locations around the globe; Munich is home to its corporate headquarters. In the fiscal year 2014, the company had a workforce of some 9,000 employees and posted consolidated sales of approximately 3.9 billion Euro.
HAIMER shrinking technology
During modern high-end milling operations systems with Weldon shanks reach their limits because of their insufficient runout accuracy. During operations with a high rpm even the smallest differences can lead to poor results, tool and spindle wear and can reduce the surface quality. Here lies the strength of the shrink fit chucks, which offer high runout accuracy thanks to their rotationally symmetric clamping body. HAIMER products offer runout accuracy of less than 3 µm at a length-to-diameter ratio equal to 3x the tools diameter.
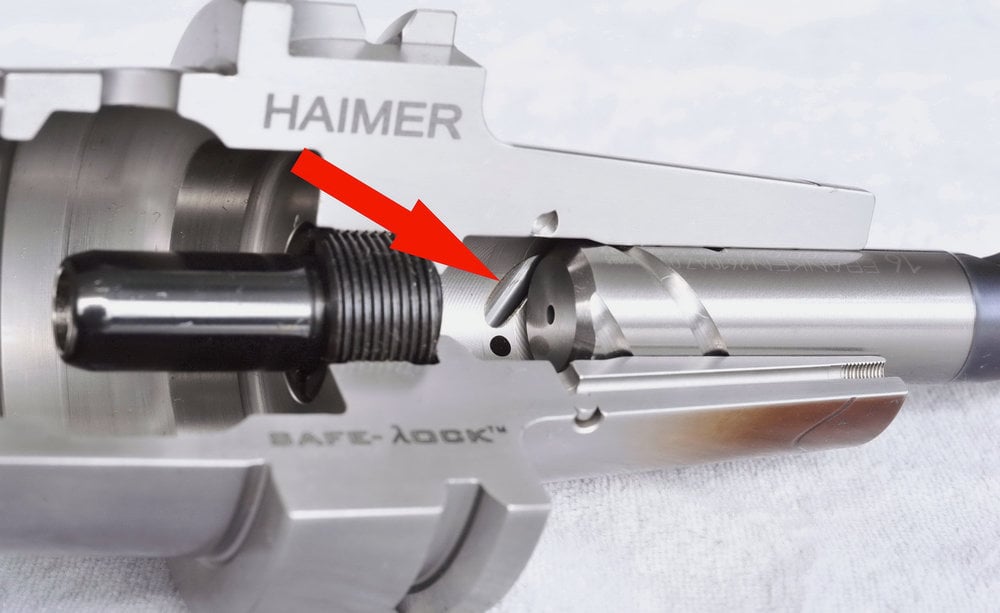
B02_Haimer_MTU_Safe_Lock.jpg
Cut away Safe-Lock™-holder for shrinking technology: the drive key, which can be seen at the bottom of the shank of the tool holder, grips into the groove in the tool shank ultimately providing form locking in combination with the high accuracy frictional clamping of shrink fit tool holders.
Picture: HAIMER
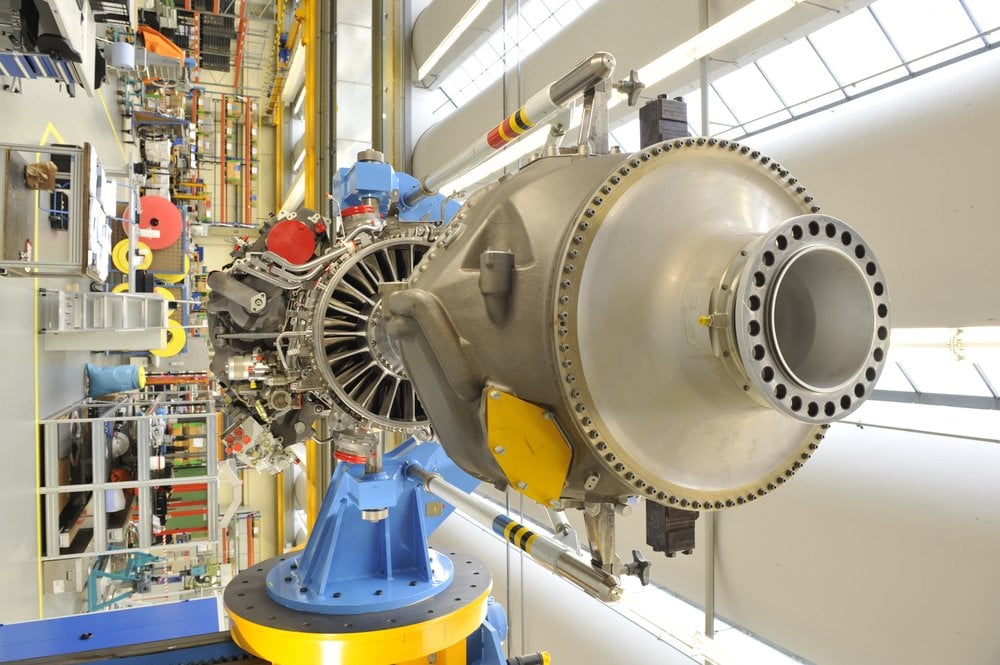
B03_Haimer_MTU_TP400-D6.jpg
MTU Aero Engines manages challenging roughing applications for the military turboprop engine TP400-D6 with Haimer Safe-Lock.
MTU is responsible for the TP400-D6’s intermediate-pressure compressor, intermediate-pressure turbine and intermediate-pressure shaft and has a stake in the engine control unit. Furthermore, final assembly of all TP400-D6 production engines takes place at MTU Aero Engines in Munich. Picture: MTU Aero Engines