www.magazine-industry-usa.com
30
'22
Written on Modified on
Engineering the future: 80 years of innovation for BOBST folder-gluers
In 1942, BOBST delivered the first folder-gluer, the PCR 382, to clients in Switzerland and France. Today, the company celebrates a historic eight decades of progress and development.
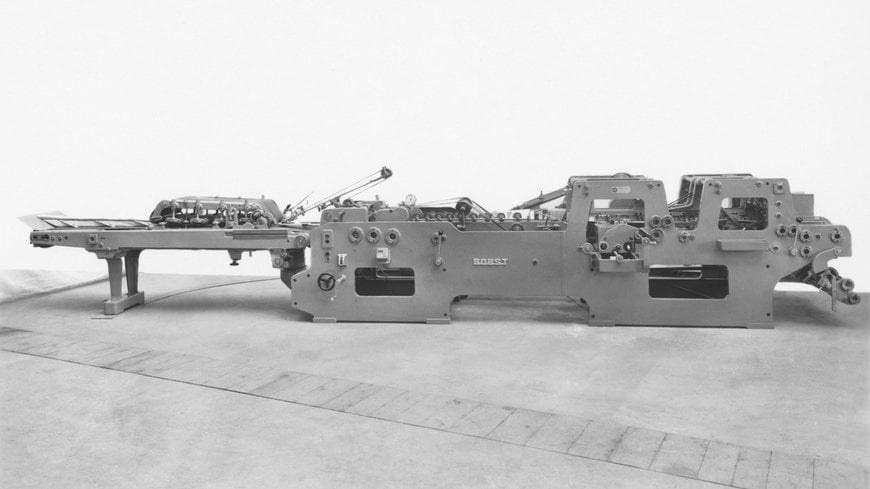
Back in the day, the PCR 382 made it possible to achieve consistently high box quality on an industrial scale. Together with the brand-new BOBST AP900 die-cutter, it created a complete converting line for folding carton boxes. Today, many of the customers who invested in the first folder-gluers on the market are still working with BOBST equipment.
Speed has become a key factor
Säuberlin & Pfeiffer SA member of the Autajon group based in Châtel-St-Denis, Switzerland, is one of those customers. Although the company is equipped with the latest generation of BOBST folder-gluers, the business owns an earlier PCR 382, which is still used to this day.
Asked why Säuberlin & Pfeiffer has remained a loyal BOBST customer, the Head of the company says: “We appreciate the stability and reliability of BOBST machines, and they are extremely easy to operate.”
Even with one of the very first folder-gluers still in use, for him, there is no comparison with today’s machines. “Setting up the PCR 382 is worlds apart from the setup of a modern folder-gluer”, he says.
Changeovers have become a crucial stage in packaging production. In addition to delivering the quality and consistency that customers expect, Säuberlin & Pfeiffer has to deal with the fact that orders have become smaller and more frequent, putting focus on faster and shorter job runs.
For the Head of Säuberlin & Pfeiffer, being equipped with operator-friendly machines which are highly automated and allow to cut down changeover times, is therefore essential. “Efficiency is key and reducing setup times is and will be an essential factor in staying competitive,” he concludes.
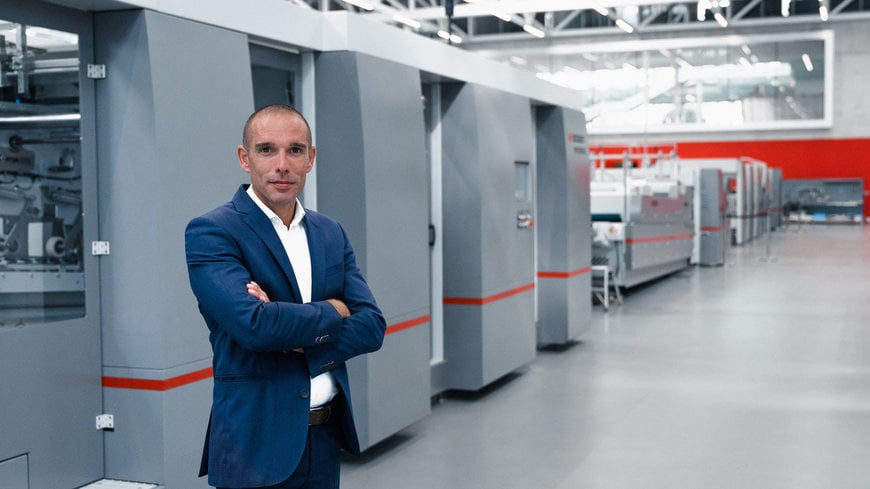
Pierre Binggeli, Head of the Product Line, in front of a folder-gluer production line in the Competence Center in Mex.
Quality is non-negotiable
The need for machines you can count on is also a topic which comes up when talking to Carlos Labori, CEO of Envase Gràfico Industrial SA (EGISA), based in Barcelona.
The company was one of the first in Spain to invest in a BOBST folder-gluer in the 1960s. Their PCR 800 has since been replaced with newer BOBST technology, and EGISA still partners with BOBST to this day.
“Of their many great qualities, we particularly appreciate their reliability, durability and modularity,” says Carlos Labori. Specialized in high-end packaging for prestigious brands, precision is a must. “Folding-gluing is at the end of the long process of designing and creating a box, and the moment when potential faults of previous production stages come to light” says Labori.
This stage of the production line is therefore essential and contributes an important part to his company’s target to add maximum value to each box. With limited space available and raising customer’s expectations, EGISA makes great use of the high level of automation and increased productivity and accuracy of the latest BOBST folder-gluers.
Although the basic folding-gluing process has not been greatly changed over all these years, there has been a huge development in the efficiency and precision of the machines. Labori adds that “BOBST machines show that quality and productivity are not mutually exclusive”. He is confident that his company will continue this long-standing relationship with BOBST, because, Labori says, “after acquiring a machine, we can always count on local Services to give us support when we need it – even if that means having a spare part delivered by taxi”.
Completing the folding-gluing line
In 1963, BOBST expanded its folder-gluer portfolio, introducing the first machine for processing corrugated board boxes, the DYNAMIC 130. This was the beginning of the development of a portfolio dedicated to corrugated and litho-laminated converting. Italian packaging converter, Fag Artigrafiche Spa, bought a DOMINO 145 in 1999 to improve the company’s gluing capacities. The very same DOMINO 145 is still used today, but Fag has since completed the machine park with several other folder-gluers.
“We could always rely on the precision of our BOBST folder-gluers, but the level of automation on the newer generation of machines has made the job for the operators much easier,” In regard to the machine evolution, Mario Gambera, Production Manager in the Dogliani Plant, says.
The company owns two MASTERFOLD 230, one of which is equipped with the brand-new SPEEDPACK automatic packer, allowing the machine to run at maximum speed of up to 250 m/min and use the full potential of the folding-gluing line.
Indeed, for Mario Gambera “the mechanization of the process pre- and post-machine is, and will remain, key to further increase the productivity and the quality of the final product.” He is aligned with the BOBST vision, considering the digital connection of machines and people in the production process as an important step towards the future of converting.
“Productivity, quality and versatility are the main characteristics of our folding-gluing department and over the years, BOBST has helped us to achieve this target with innovation and service” concludes Gambera.
A vision for the future
“We are very proud of what we achieved in those last 80 years” says Pierre Binggeli, Head of Product Line Folder-gluers at BOBST. Pierre has been with the company for over 20 years and witnessed important evolutions.
“The human element will always be an important factor in the folding-gluing process, but today’s machines are much more productive, precise and flexible, while offering an ever-increasing level of automation, ease of use and operator security,” He says.
Having added different devices, modules and peripherals to the folder-gluers over the years, almost every machine delivered is different, matching the customer’s particular needs. Today, the most recent machine developments also include the digitalization and connectivity needed to allow customers to shift into Industry 4.0.
As Pierre puts it: “Although BOBST is celebrating the 80th anniversary of folder-gluers today, we are fully focused on what lies ahead and committed to the 4 pillars of the BOBST vision: connectivity, digitalization, automation and sustainability. Today’s economic and ecological challenges are huge. But we are determined to continue to innovate, to stay ahead of the curve and engineer the future of the packaging industry.”
www.bobst.com