Latest generation of Voith dispergers: InfibraDisp sets standards with hydraulic gap adjustment
Voith is expanding its product portfolio in the BlueLine stock preparation line with the launch of a new disperger with hydraulic gap adjustment. InfibraDisp is characterized by precise, infinitely variable gap adjustment, automated zero-point adjustment and user-friendly handling. The newly developed, smart control unit enables monitoring of filling wear and prevents any risk of plate contact with vibration sensors. As the core element of the BlueLine Compact Dispersion System, the new InfibraDisp contributes significantly to the provision of a high-quality raw fiber material based on recovered paper.
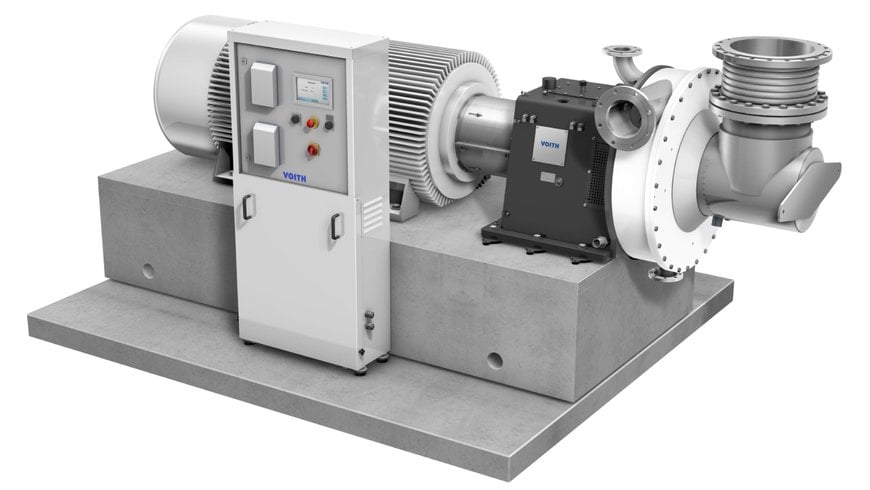
InfibraDisp is characterized by precise, infinitely variable gap adjustment, automated zero-point adjustment and user-friendly handling.
- Hydraulic gap adjustment allows continuous and precise adjustment of the dispersion intensity
- Automatic zero-point adjustment for a consistently high and reproducible dispersion result
- Robust design, high reliability and easy maintenance
InfibraDisp: Hydraulic gap adjustment allows continuous and precise adjustment of the dispersion intensity
In dispersion, bothersome particles and inks are separated from the fibers and milled to a size suitable for further processing. The newly developed disperger achieves outstanding increases in strength of up to 25% and optimally prepares the fiber structures for subsequent starch application. The new hydraulic gap adjustment allows infinitely variable and precise adjustment of the dispersion intensity, thereby achieving an outstanding dispersion result. The adjustment can be made at any time by means of a user-friendly control panel directly on the machine. Together with the new disperger, Voith's The Wall disperger filling forms an ideal combination for achieving the best technological results with comparatively low specific energy input.
Automatic zero-point adjustment for a consistently high and reproducible dispersion result
“The hydraulic system of the new InfibraDisp disperger allows us to perform a precise ‘zero-point’ adjustment after the plate change by just pressing a single button. This eliminates the need for manual intervention on the disperger itself,” says Susana Fernández-Carrión, Stock Preparation Plants Manager at Saica in Saragossa, Spain. Due to the automatic zero-point adjustment, InfibraDisp delivers an optimal dispersion result at any time. The fully automatic zero-point detection is initiated by the operator and then runs autonomously.
“Operation of InfibraDisp is much easier than with the familiar dispergers on the market due to the automatic zero-point adjustment,” says Tomislav Druzinec, start-up engineer at Voith Paper. “Since the result can be reproduced independently of the respective operator due to the automatic recognition, our customers are able to significantly stabilize their dispersion process.”
InfibraDisp's feed screw is driven by its main drive, which ensures a homogeneous and continuous stock feed to the filling, prevents clogging and minimizes performance fluctuations during the dispersion process.
Robust design offers high reliability and easy maintenance
The stable welded construction of the new disperger with hydraulic gap adjustment offers long, reliable and almost wear-free operation. The feed screw is driven by the main drive of the disperger. This results in a homogeneous and continuous stock feed to the filling; the formation of blockages is prevented and performance fluctuations occurring during the dispersion process are minimized.
At the same time, the feed screw is easily accessible and the entire machine is very easy to maintain thanks to a single drive. “The design concept of a single motor driving both the rotor and the feed screw has saved space and will ultimately reduce our maintenance costs,” says Fernández-Carrión from Saica in confirmation. The combination of forced and sump lubrication continually lubricates the bearing arrangement of InfibraDisp, thus increasing operational safety even in the event of unforeseeable incidents.
Automation advantages through newly designed control unit
In addition to the new hydraulic gap adjustment, a further core component is the specially designed control unit. The “digital brain” of InfibraDisp enables previously unrealized 4.0 features. The control unit contains the automation function, which controls the autonomous zero-point detection, processes the values of the vibration monitoring and adapts to technical parameters locally.
“The new system for measuring filling wear will allow us to improve the monitoring of fillings throughout their life cycle, to compare the wear between different fillings or with different raw materials and to detect abnormalities even before a planned shutdown,” says Fernández-Carrión, praising the digital development. In the future, the wear monitoring system can, for example, interact directly with Voith’s Webshop and thus automatically initiate a filling order. In addition, the filling runtime is permanently monitored and the remaining operating time is calculated. The next filling change is therefore predicted in good time and downtime dates are recommended.
Compact dispersion system: Low-cost, optimum dispersion results
The new InfibraDisp disperger is part of the BlueLine Compact Dispersion System from Voith, which is characterized by high energy efficiency, a reliable and high dewatering performance, and reduced spatial requirements. In addition to InfibraDisp, the dispersion system includes the InfiltraScrewpress screw press and the InfibraHeater heating unit.
www.voith.com