www.magazine-industry-usa.com
17
'12
Written on Modified on
KRPXng concept, by REDEX
KRPXng is the newest successful range of REDEX rack & pinion drives portfolio, especially designed for machine-tools with moving column or gantry. The cost effective and easy to implement KRPX, is a remarkable example of the close cooperation between REDEX and Machine-tools OEMs leaders.
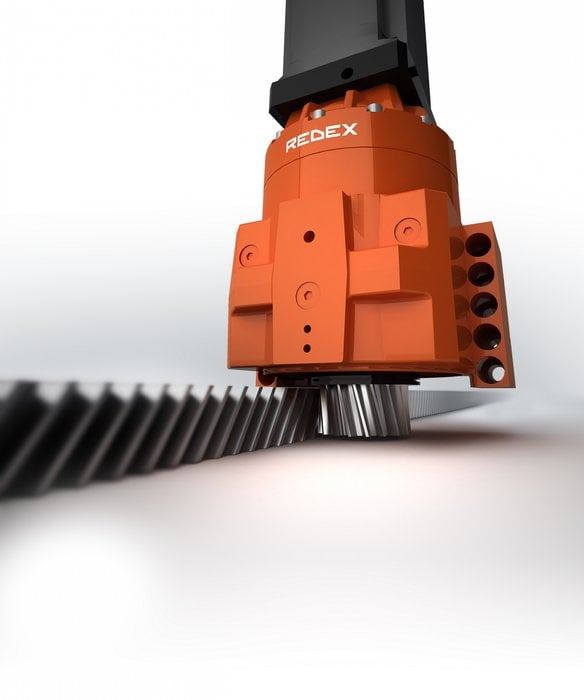
Easy integration and cost savings
The implementation of a TwinDRIVE solution (1) on a moving column or gantry machine was, before KRPX, rather difficult and required either a special extension on both sides of the main frame, or a new design and the production of special bracket supports to be fitted to the frame.
Each solution must keep the global stiffness at the same level as the main frame, to avoid deterioration of the dynamic performances.
Those special configurations require spending time and money on designing the part to fit perfectly, manufacturing it. It also might increase significantly the design risk.
KRPX eliminates the need to design and integrate any high precision fixation extension to the main machine frame as the frame extension is already a part of the KRPX design itself.
This greatly simplifies the implementation process and is more cost-effective (15 to 20% less expensive) then the conventional solutions.
A precise keyway is machined on the mounting surface, allowing an easy settling while keeping perfect mounting geometry. This smart system was specifically designed to cancel the risk of wrong mounting and system deflection.
Full range designed, proved, and available
Available in the 5 standard universal sizes (size 1 to size 5), KRPXng is compact and hold a definitive implementation advantage with respective pinion height not higher than 75.9 to 135 mm.
With this exclusive Racks & Pinion Drive concept, the machine-tools designer can easily expect to exceed market standard with maximum feed capacity up to 145 000 N and stiffness on the rack up to 463 000 N/mm.
The full range is designed to be supplied together with the highest standard of quality racks, and its compatible fully automatic lube system.
Machine-tools quality construction and ultra-high stiffness
KRPX housing is made of high quality spheroidal graphite cast iron. KRPX uses oversized screws to ensure perfect mounting and absolute security.
Its global structure has been optimized with FEM analysis methods to avoid deflection during acceleration.
Output pinion is machined into the output shaft, and at the same diameter, offering a perfect combination of transmissible torque and rigidity at the rack.
The output bearing consists out of two preloaded and substantially oversized angular contact roller bearings.
This construction enables the bearing to support the pinion as close as possible to the force, as only the thickness of the fastening nut separates the pinion from the output bearing.
This design reduces dramatically the radial bending, a factor responsible for up to 60% of the overall distortion (and even so poorly handled by most of the other existing systems on the market).
As a consequence, the natural frequencies of the global axis drive systems, in which the KRPX is integrated, can be raised more than significantly: its performance in terms of compound stiffness combined with its low inertia enables higher accelerations (up to 25 m/s2) and therefore give ability to move heavier loads at higher speed.
KRPXng is a complete, ready to use product, a real turnkey solution which gives the best cost effective – improved dynamic precision, combination on the market thus makes it an easy choice for machine designers.
Improving Energy efficiency
After turning their latest R&D achievements into gear quality standard, REDEX Engineers took another step forward, introducing a new gear finishing technology to the machine tool industry. This new technology, HQ-GF, ensures high-reversibility, significant noise reduction, and above all, a decrease of over 15% of power losses (2).
Thousands of kWh are saved in a machine’s lifetime!
With the HQ-GF inside, the new KRPXng technology is joining the long line of REDEX’s innovations designed specifically by its engineers team to improve the machine-tool industry.
(1) TwinDRIVE solution means true zero backlash by using two servo-reducers and electrical preload
(2) HQ-GF compared to standard DIN quality 6 gears obtained by shaping.
www.machine-tool-drives.com
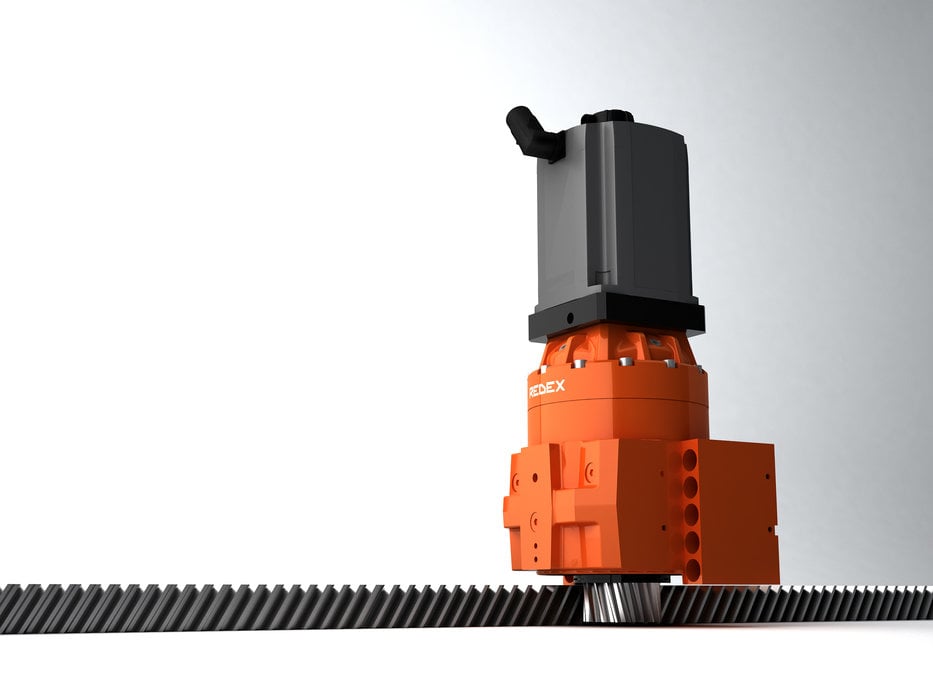
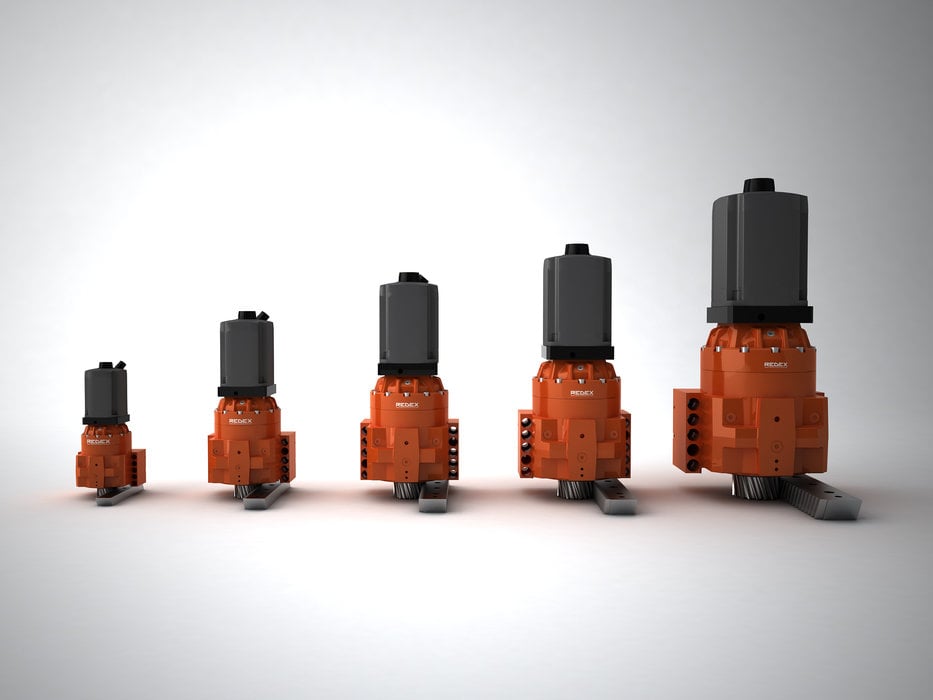