REDEX rack and pinion drive cooling systems: high productivity without compromising precision
The potential to increase machine tool productivity through higher feed rates and greater dynamics is reaching its limits, especially in light of growing demand for multi-tasking turn-mill machines.
www.redex-group.com
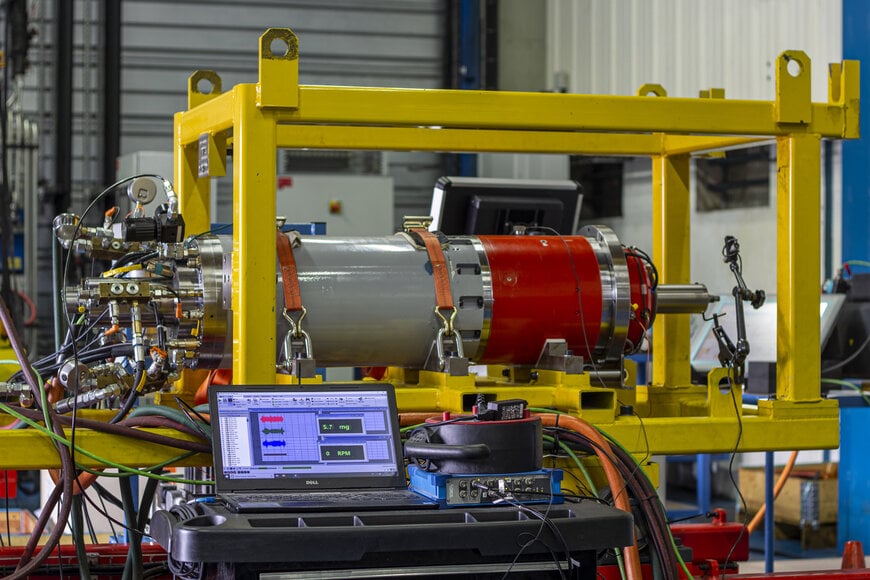
REDEX Group can help design engineers achieve a step-change in the productivity of multi-task machines with its cooling-optimized high-precision drive solutions. Such an advance subsequently presents the potential to capture a larger share of this highly competitive global market.
Not so long ago, the milling tables were limited to the production of prismatic parts with drilling and/or tapping operations, the round shapes of which were produced by low-speed milling. Today, a multitasking machining center can produce cylindrical parts obtained by rapid turning with milling/drilling features on the same machine in a single set-up - driving immediate gains in productivity.
But this increase in productivity generates thermal constraints, because with more torque and higher speeds, the power involved exceeds the limits acceptable for conventional drives. The result is temperature problems that lead to machine inaccuracy.
Developing a stand-out multi-tasking machine tool instead requires adapting the drive type and machine structure to achieve the necessary gains in performance, versatility, and precision. However, it demands technological changes.
Motor manufacturers are already offering, air-cooled or water-cooled versions of motors are already available, allowing high continuous speeds while maintaining an acceptable operating temperature. Along the same lines, REDEX has for several years been developing cooling options for its drives to ensure effective heat dissipation and the maintenance of operating temperatures compatible with the precision that end users expect from a multi-tasking machine.
Rack and pinion: the driving force
When selecting a suitable drive solution for a new machine tool, three options are available: a direct-drive motor (linear motor), ball-screw drive, or rack and pinion drive.
Direct-drive (linear) motors have largely become unaffordable because of the cost associated with magnetic elements, cables and complementary cooling components. Their high power consumption in comparison with servomotors also makes this option unappealing.
While ball-screw drives currently enjoy widespread adoption in the general machine tool market, several design limitations bring into question their suitability for the productivity and performance required by multi-tasking machines. For instance, heat accumulation following repetitive and intensive ball-screw motion generates positioning errors due to thermal expansion. This undesirable effect could throw doubt on the ability of the machine tool’s structure to comply with ISO 230-3:2020-6 tests for thermal distortion.
With these factors in mind, rack and pinion drives are proving the go-to solution for controlling the thermal behavior of feed drives in large multi-tasking machines. Wherever there is a need for highly dynamic, heavy-duty motion, design engineers will find many advantages with the latest cooling-optimized rack and pinion drives from REDEX.
These benefits include low temperature at the point of contact between the pinion and rack, whatever the feed speed. Moreover, there is no critical speed at high feed rates as the rack and pinion mesh at low speed. Further advantages include modular and unlimited travel capability using rack segments, and high and constant stiffness independent of position.
Cooled rack and pinion drive systems also enable easier handling of a machine tool’s linear movement without any signs of metal expansion, which can sometimes result when using a ball screw or non-cooled rack and pinion drive.
Keep cool under pressure
Special cooling options devised by REDEX protect the drive from heat accumulation in highly dynamic machine tools such as multi-tasking models. The company bases its success in this technology on decades of experience. Indeed, it was around 40 years ago when REDEX pioneered water-cooled, two-speed gearboxes for high-speed, high-torque spindle drives on machine tools. It was also the first manufacturer to offer cylindrical gearboxes with hollow shafts for maintaining a satisfactory operating temperature when integrated between the motor and spindle. This gearbox offered an operating temperature delta (Delta T) some 10°C less than the machine’s spindle and motor, despite speeds up to 12,000 rpm.
REDEX has developed its current technological advances in line with the latest generation of geared motors, integrating both the motor and reducer with a cooling circuit capable of dissipating heat. By maintaining an ultra-low operating temperature, machine tool builders ensure the stable spindle structure necessary for precision in turn-mill machining operations.
REDEX can recount numerous examples of designing and implementing solutions built according to the specific requirements of individual machine tool builders. All of the company’s solutions are subject to rigorous systematic testing protocols, running tests with full temperature checks and verification of nominal gearbox ratings. REDEX has even developed modeling systems using digital twins in support of accurate simulations.
First-rate performance
The nominal ratings of planetary gearboxes result from theoretical bearing and gear capacities according to the load level at several different speeds, as well as the calculated service life. REDEX design engineers have developed a numerical model capable of predicting the operating temperature of gearboxes, specifically their thermal behavior and efficiency. This model enables the extrapolation of a torque curve corresponding to the constant (thermal) power of the system in a given configuration. An intensive testing program involving the REDEX RP series of high-precision planetary gearboxes demonstrated the correlation between theoretical and experimental data.
With this approach, REDEX can anticipate and assess thermal operating limits to propose the optimal heat dissipation solution and determine the most appropriate cooling method.
The REDEX RP series offers two levels of cooling: standard and optional. Standard configuration presents a highly effective form of external forced lubrication, where cooling by recirculation of the lubricating oil bath within a closed loop allows the dissipation of losses via an oil/water or oil/air exchanger. As a key point of market differentiation, REDEX includes holes as standard in both its circular gear (pinion) and linear gear (rack) solutions, facilitating the internal circulation of cooling fluid.
Whenever application requirements exceed a drive’s thermal capacity, the standard cooling option for REDEX RP series drives is ideal. It is the most simple and cost-effective option for the cooling of drives on large multi-tasking machine tools. Notably, this solution is only available from REDEX.
The optional level introduces a cooling jacket to the solution. Although the cooling jacket adds size, weight and cost to the system, it can prove highly effective in certain applications.
In all cases, the highly skilled REDEX engineering team can provide advice on machine tool gearboxes and the associated cooling options based on decades of real-world experience.
www.redex-group.com