www.magazine-industry-usa.com
20
'12
Written on Modified on
Cleancon – Technical cleanliness of fasteners
In modern systems in the automobile industry and electronic equipment, particles as small as 500, 200 or even 100 microns can cause malfunctions or total system failure. In many cases these problem particles on components originate from fasteners. The Cleancon cleanliness concept developed by Arnold Umformtechnik provides a process that eliminates the risk of system failure due to particles by taking an integrated approach from fastener production to assembly.
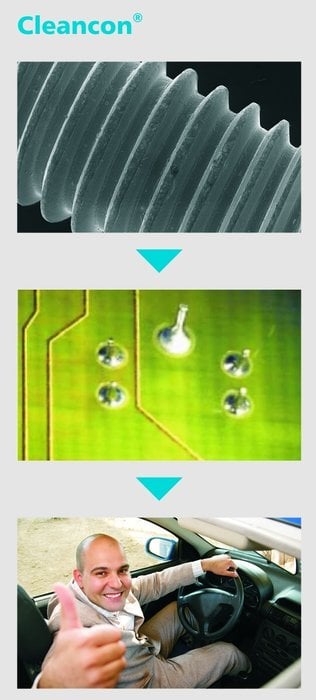
Increasing compactness of units and assemblies makes them more and more susceptible to problems from particle contamination. Even microscopic metal particles can cause enormous damage, for example if they cause shorts between tracks on circuit boards. These problem particles end up on components not only during production, but also during transport and assembly or from fastener elements such as bolts and nuts.
A solution for need-compliant cleanliness
To eliminate fasteners as a source of contamination and achieve the necessary technical cleanliness in a cost-effective manner, Arnold Umformtechnik has developed the integrated Cleancon concept (Figure 1). Along with cleanliness-compliant production, quality control and packaging of bolts and nuts, it encompasses fastener assembly and the assembly environment. In this concept manufacturers of fasteners and cold-formed parts cooperate with partners in the areas of process technology and cleanliness analysis.
The first step is to generate a requirements profile together with the customer, which defines the required technical cleanliness, specifications for cleanliness checks, packaging specifications and data about the application and the process environment.
A optimised process from design to packaging
The later cleanability and economically achievable cleanliness of fasteners and cold-formed parts must be considered as early as the design stage. This also ensures that the parts do not have geometric features, such as sharp edges, that can act as particle sources due to abrasion during transport and subsequent processing. Production processes are also designed to minimise the occurrence of microscopic particle contamination, by means such as cleaning between the individual production steps.
To fulfil strict cleanliness requirements, the parts undergo microcleaning in a cleanroom at the end of the production process. A low-friction coating is also applied in this cleanroom environment if necessary. In parallel with series production, cleanliness tests conforming to VDA 19 for particle size distribution and gravimetrics are performed in the Cleancon lab.
The parts are also packaged in the cleanroom. Arnold Umformtechnik has developed the Cleanpac packaging system (Figure 2) for this purpose. This multilayer transport packaging consists of an anti-static inner retainer and an outer shell. The retainer prevents relative motion between the parts during bulk transport and the resulting abrasion and particle formation. The Cleancon concept significantly reduces the number of metallic particles on the components in comparison with conventional production processes.
Avoiding recontamination in assembly
As soon as the parts are unpacked for assembly, there is a risk of recontamination – either from the assembly environment or from the assembly process itself. Arnold Umformtechnik works together with partner companies to support customers in these areas as well. This is based on the recommendations for cleanliness-compliant assembly in the VDA 19 Part 2 guideline, “Technical Cleanliness in Assembly – Environment, Logistics, Personnel and Assembly Equipment”, published in 2010.
The main consideration in the processing technology area is threaded fastener systems, since the number of particles and particle sizes can be reduced significantly by using suitable technology in joining processes with both manual fastener tools and stationary driver systems. Among other things, step conveyors and "dirt brakes" such as those developed by Weber Schraubautomaten GmbH in Wolfratshausen (Germany) play a role in this.
Along with numerous assembly processes in which particles can end up on the components, the assembly environment is a potential source of contamination. Data on the particle burden in the assembly environment can be provided by particle monitoring, for example using particle traps.
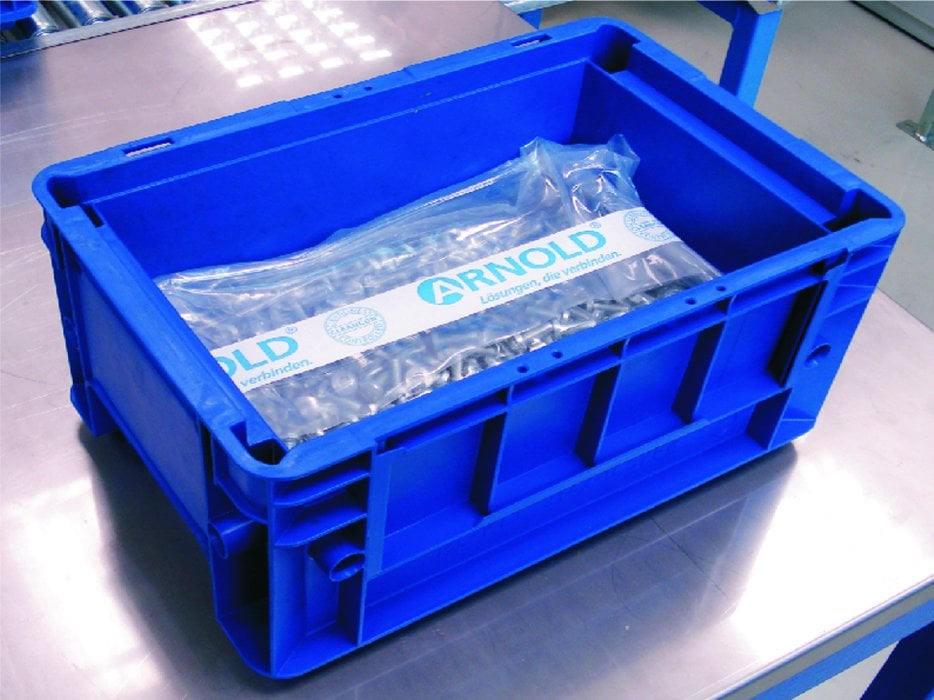
Caption: Arnold-Cleanpac. Bulk fasteners are held securely in place in packaging specifically developed for cleanliness critical fasteners. This prevents particle generation due to relative motion.
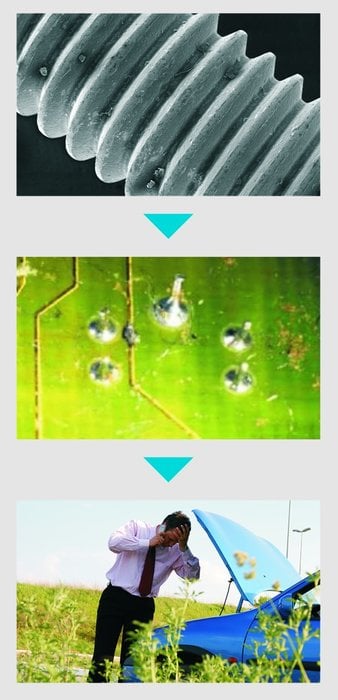