Special geometric shank geometry achieves high pull-out forces
When joining plastics, light metals or steel together, press-fit screws are often used. Thanks to a new triangular-shaped quick fastening system, with locking threads on a triangular shaft, very high pull-out forces can now be achieved and clamping parts fixed rapidly.Thanks to a new triangular-shaped quick fastening system, with locking threads on a triangular shaft, very high pull-out forces can now be achieved and clamping parts fixed rapidly.
www.arnold-fastening.com
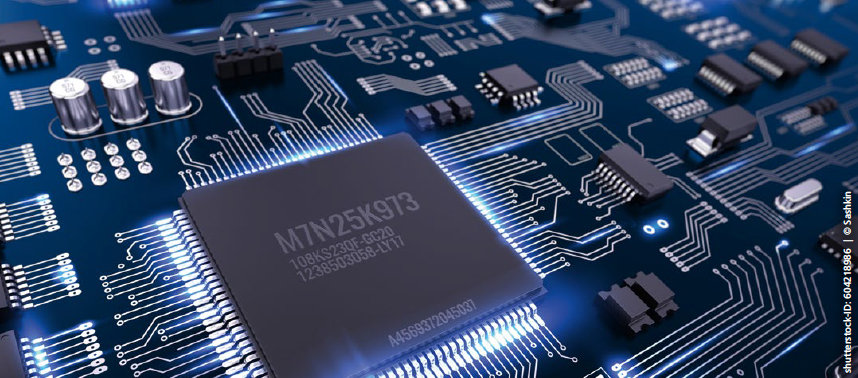
Thanks to a new triangular-shaped quick fastening system, with locking threads on a triangular shaft, very high pull-out forces can now be achieved and clamping parts fixed rapidly.
In comparison with screw fasteners, press-in components offer the advantage of shorter assembly times, independence from preload forces, and force-controlled press-fitting. In comparison with injection screws in plastics, shorter cycle times are possible and there is no need to insert metal parts into injection moulds.
The Tripress quick fastening system from Arnold Umformtechnik GmbH & Co. KG has been used reliably for years for fast assembly with press-fit screws, for example in the automotive and electronics industries. Now, with Tripress Plus, a geometrically enhanced version is available, capable of higher performance. While Tripress is a polygonal press-fit system with a uniform shape along its length, the characteristic feature of Tripress Plus is its polygonal shaft incorporating a twist. This is created when the part is profile rolled, i.e. directly during production.
The shaft geometry patented by Arnold Umformtechnik, the rotating polygonal cross-section implemented in Tripress Plus, ensures that the user can transfer significantly higher forces. Customers can thus use it for downsizing or weight reduction.
Tripress Plus quick fasteners can be inserted fully automatically, semi-automatically or using manual pressing techniques.
They are suitable for aluminium, copper, plastic and steel applications.
The fasteners can be used to attach light metals, such as aluminium, and also copper, plastic assemblies and steel. Areas of application include automotive engineering, especially add-on components and electronics, as well as electromobility components and systems. The main applications are those with no rotating elements, such as circuit board fastenings.
There are numerous reasons for using the Tripress Plus, for example to obtain a more lightweight construction due to its lower weight, or to reduce installation space and, of course, for significantly shorter cycle times. The positioning time is significantly shorter compared that of a conventional screw. There is also no dependency between speed and pitch, as Tripress Plus is pressed-in purely axially. This results in significant time saving.
Applications without clamping parts are also possible, as the reliable holding force of the Tripress Plus is independent of the preload force. The quick fastener is tamper-proof, because it is not possible to loosen it without destroying the part. And thanks to high holding forces with small press-in depths and a flat head, the fastener is also suitable for small installation spaces.
According to Arnold Umformtechnik, inquiries for press-fit screws are on the increase. There is demand for suitable fastening solutions for ductile light metals, such as aluminium and copper. The focus is mostly on assemblies such as control units, charging modules and components for power electronics.
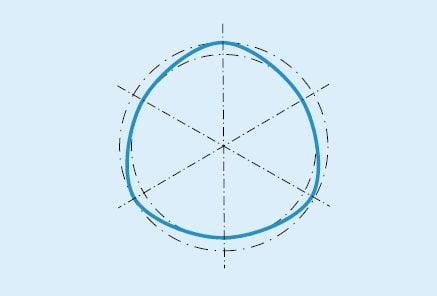
Areas of application for Tripress Plus include automotive engineering, in particular for add-on components and electronics, as well as electromobility components and systems.
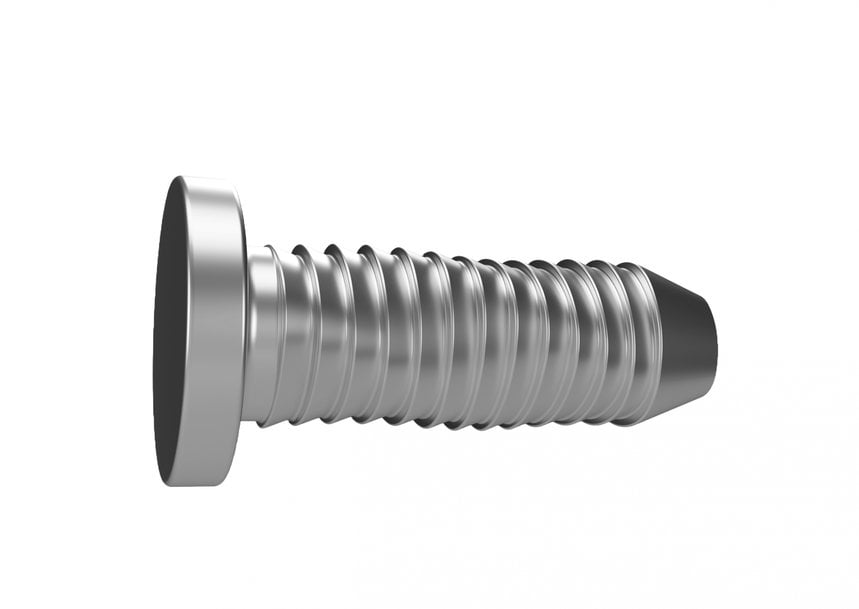
Tripress Plus has a polygonal cross-section that twists along the shaft. The locking threads on the triangular shaft ensure very high pull-out forces and enable the clamping part to be fixed rapidly.