www.magazine-industry-usa.com
02
'19
Written on Modified on
Fast, convenient water quality monitoring could hold the key
Water is used in so many ways throughout the food and beverage industry, even as the final product, which means the quality of that water needs to be carefully monitored.
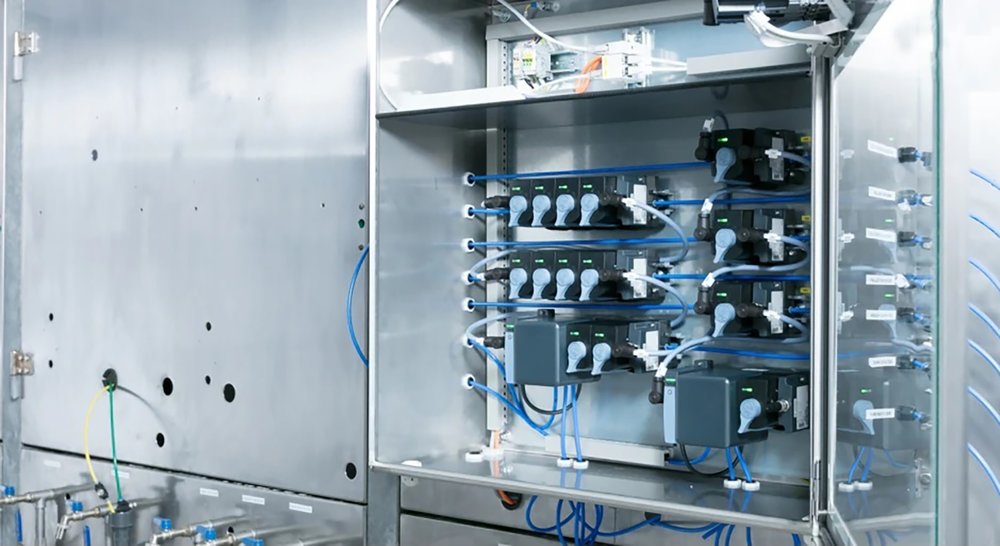
Water is an essential element in the manufacture of food and drink, from washing produce to being the main ingredient, each application has different water quality requirements. Having access to reliable, up-to-date data on water quality parameters is an important step in improving productivity as well as the quality of the final food products.
Source monitoring
In most cases, water will be supplied by the local water authority, which has the responsibility to provide a service within certain parameters. However, demands on the treatment plants, seasonal changes and the age of the network can have a big influence, and this means variability in the quality of mains-supplied water.
It is possible for the local authority to be unaware of an ‘out-of-consent’ incident until it is reported by consumers, but for some industrial customers, this notification will have come far too late.
Furthermore, water authorities are required to add sufficient levels of chlorine to reach the furthest points of the network. This means that those closest to the water treatment works may receive some free-chlorine, which can damage sensitive equipment such as reverse osmosis membranes for example.
The alternative is a bore hole, usually on or near the manufacturing site, but this source can be affected by temperature, rainfall and local agricultural activities, which means it needs to be tested for quality at least every month, preferably more frequently. On-site treatment should be looking to remove sediment, dissolved iron, nitrates and bacteria.
Filtration systems
Whichever source is used, manufacturers will employ a range of water treatment processes, depending on their application. Carbon filters can remove chlorine, biological contaminants and flavours, while a sand filter will remove iron. Ion-exchange processes are used to soften the water and both pH and conductivity monitoring can take place at this point.
Finally, filtration is used to remove unwanted particles, organic matter and bacteria. Depending on the quality of water required, manufacturers may use ultra-filtration, nano-filtration or reverse osmosis and each process can be equipped with sensors for turbidity, chlorine and pH to provide feedback on water quality.
Many businesses will use third party water services companies to monitor the water quality and address any issues on a regular basis. The problem with this approach is the frequency of the interventions and the reporting. In many cases, a monthly visit is deemed appropriate, so an issue could reasonably go undetected for over three weeks, which could affect a significant volume of products.
Capturing vital data
To resolve this situation, manufacturers need an accurate but flexible system that can be built around their application and connect directly into their control infrastructure. Some will only need pH and turbidity, while others require a more comprehensive solution that includes iron, chlorine, conductivity and oxidation reduction potential (ORP).
However, capturing the data is just the first step, validating it for accuracy and using the data for positive process control also need to be considered. To this end, calibration of the sensors is an important step that may require a certain amount of downtime and additional expense.
Of course, even reliable data is of little use unless the process control system can use it effectively. This requires common communication protocols and these may vary between manufacturers.
Modular, flexible solutions
There is an opportunity for food and beverage manufacturers to use the latest in sensing technology that has a proven track-record in accuracy and simplicity. As a compact and modular design, Bürkert’s Type 8905 Online Analysis System, offers a range of benefits that make it cost-effective and reliable for this purpose.
The Type 8905 offers a multi-channel, multi-function unit capable of measuring pH, ORP, conductivity, free chlorine and turbidity, chlorine dioxide and iron. Several of the measurements are conducted by compact plug-in sensor cubes, offering ease of use and convenience. The introduction of a chlorine monitor is an important addition due to its popularity in the disinfection process as an effective microbicide, disinfectant and sanitiser.
Bürkert has also developed an auto-cleaning process for the sensor cubes that uses a solution of clean, filtered water and mild citric acid, primarily to flush the turbidity sensor cube. The accuracy of the water analysis equipment can be maintained using a hand-held cleaning and calibration module that connects to the Type 8905.
This enables operators to follow simple step-by-step maintenance instructions and procedures for using calibration fluids. All the while, the base unit is constantly monitoring the process and recording the necessary data.
Simple installation
The compact design of the Type 8905 ensures a minimal footprint and the innovative sensor design means that sensor cubes can be installed or removed without affecting any others in the system. When a new sensor cube is plugged into a free slot, it logs in with the system and makes its features available to all of the other modules present in the system. Each sensor cube contains all the required data for operating the menus, configurations and its specific functions.
This enables operators to start with an initial set of parameters under analysis that can be added to at any point without affecting the existing system. For applications where multiple water flows need to be analysed, it is already possible to link two or more of the type 8905 units together and combine their operational controls to a single touch-screen display.
Of course, investment in water quality monitoring equipment needs to be carefully assessed and often supporting evidence is required to obtain the capital expenditure. With this in mind, Bürkert offers short-term rental solutions for the Type 8905, enabling end users to build a water quality profile while also creating a case to support a capital submission process.
For every business that needs to maintain high water quality standards and ensure the integrity of on-site water treatment facilities, taking advantage of the latest in analysis systems can deliver significant benefits. Saving time and reducing maintenance requirements, the Bürkert Online Analysis System is just one way to provide simple, accurate ‘live’ results to enhance long-term quality and productivity.
www.burkert.com