www.magazine-industry-usa.com
12
'19
Written on Modified on
Fraunhofer is helping speed up development of fiber-reinforced plastic components
Fiber-reinforced plastics are the basis for many applications in state-of-the-art lightweight design, and they offer numerous advantages.
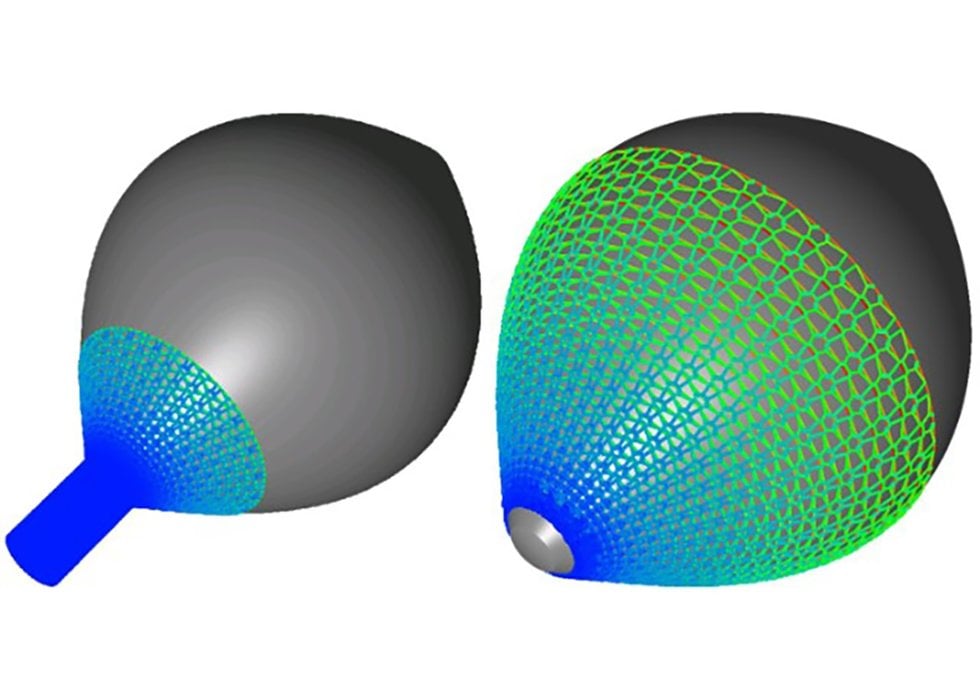
Demand for lightweight design is steadily rising in vehicle body, aircraft and building construction. After all, it accommodates a wide array of applications while keeping material consumption to a minimum. Fiber-reinforced plastics are a prime example of a solution that typifies these advantages.
They are lightweight and moldable, yet also robust. In addition, new manufacturing techniques and fibrous materials are being developed – also by Fraunhofer Institutes, among others – that lower manufacturing energy consumption.
“But there are countless ways to arrange the textile fibers in plastic components. Which fibers lie how close together and in what orientation to one another, and how are they interconnected? Every combination of these parameters has a major impact on the component’s drapability, visual appearance and stability,” says Dr. Julia Orlik, project manager at Fraunhofer ITWM.
“That’s why it’s currently common for development departments to approximate the fiber structure for every particular component based on their experience, then produce successive batches of sample parts until they achieve the best result.”
Because of this, development accounts for one-third of total component costs and product manufacturing for two-thirds. Smaller companies often shy away from this high development effort in terms of personnel, time and materials.
Are such high costs and efforts avoidable?
Researchers at Fraunhofer ITWM in Kaiserslautern asked themselves: if the properties of the component design depend on the stated parameters, then is the reverse approach possible? Can the properties be calculated from the parameters? A realistic simulation could thus reduce the required development effort and consumption of resources.
This is the goal of the OptiDrape project, a collaboration between Fraunhofer ITWM, RWTH Aachen’s Institut für Textiltechnik (ITA) and the Assoc. Institute for Management Cybernetics e. V. (IfU), also based in Aachen. ITA first analyzed different fibers and textiles and determined their tensile, shear and bending properties and their critical shear angle – the structure-dependent angle up to which different fiber strands can be moved relative to each other before defects arise.
Fraunhofer ITWM already had a wealth of experience in the mathematical simulation of textile structures at its disposal, so now it used self-developed software that, based on an extensive mathematical analysis, virtually simulated the properties in parallel. Using the ITA’s findings, the calculated results could now be validated.
Successful simulation of experimental results
“The results speak for themselves: TexMath – the textile software we developed – calculates the characterizing properties, and does so in the same tolerance range as physical test methods. Both arrive at a variance of around 5 percent, which means that the critical shear angle can also be calculated in advance, accurate to within 2 to 3 degrees,” says Stephan Wackerle, a scientist at Fraunhofer ITWM.
“The new OptiDrape software builds on this and uses machine learning to find the best textile for each draping application; if desired, it will also optimize the component geometry.”
The simulation enables companies to continuously vary all design parameters and thus craft the optimal textile layout and design for any application and specification, effectively minimizing the need for experimental test results and savingtime, effort and expense.
The project is supported by a committee made up of automotive and aircraft industry suppliers and software manufacturers. Thanks to their input, Fraunhofer ITWM has already compiled suitable catalogs of draping options for construction companies and vehicle body manufacturers. Above all, OptiDrape will soon let even SMEs benefit from the advantages of fiber-reinforced plastics.
www.fraunhofer.com