Computational imaging improves imaging at source
Computational Imaging (CI) uses data extracted from a series of images acquired under different lighting or optical conditions to create an output image containing the details that are most important to a particular machine vision task.
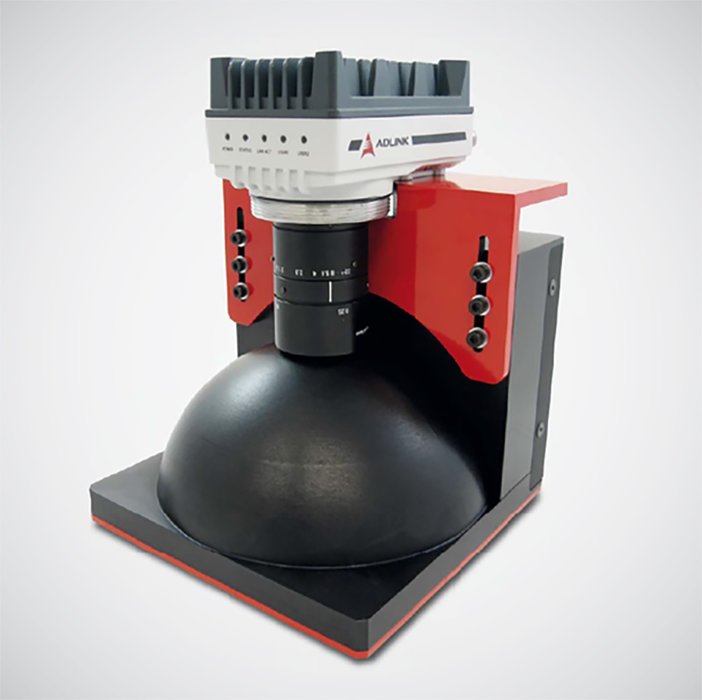
This approach offers powerful advantages over traditional one-shot imaging. It can improve the capability of a camera and reveal image detail not previously possible.Unlike traditional image acquisition, which often requires substantial post-capture image processing, CI is configured to directly output the required image, leading to more robust MV solutions.
Computational Illumination
A key requirement of CI is to optimise the lighting configuration and deliver a sequence of strobed images with different illumination for each frame. This might involve changing the intensity, angle or wavelength of illumination for each frame. By choosing from multi-segment, multi-spectral or multiple independent lights, a number of CI techniques are possible for applications such as image enhancement, image deblurring, geometry/material recovery and others.
Typical CI techniques include:
- High Dynamic Range imaging (HDR) – creating images with higher contrast ratios
- Ultra-Resolution Colour (URC) – creating higher resolution colour images with no interpolation artifacts
- Extended Depth of Field (EDOF) – improving measurements without losing light or reducing magnification
- Bright Field/Dark Field – combining the advantages of two well-known lighting techniques
- Multi-spectral Imaging – enhancing images with maximum contrast from multiple spectral bands
- 360° object capture – panoramic imaging with singly triggered, multiple scene acquisition
- Photometric Stereo (PMS) – generating edge and texture images using shape from shading
Machine vision lighting specialist, CCS Inc, offers a complete Computational Illumination Kit for use with any machine vision camera and most smart cameras. This includes an extensive choice of 4-quadrant ring or bar lights, full colour, multi-spectral or segmented full colour lights as well as a 4 channel light sequencing switch, software and cables.
Using an external system trigger, the light sequencing switch runs a pre-programmed sequence of lighting on the 4-channels and outputs a correlated camera trigger, automatically timing an external camera exposure to the programmed lighting sequence.
The frame time and exposure for a sequence can be set as well the strobe width for each of the independent channels. The system is fully compatible with leading machine vision software such as Sherlock from Teledyne DALSA, where Photometric Stereo is already implemented.
Shape from shading – the trevista process
One particularly important application of Computational Imaging is Photometric Stereo, or shape from shading. Inspecting shiny and curved surfaces or materials with variable brightness are extremely challenging tasks for machine vision systems.
The patented ‘trevista’ shape from shading method has been specifically developed to inspect the texture and the topography of the test specimen separately. The special technology offers fully automated, process-safe 100% inspection which can reliably detect even the smallest defects on such difficult surfaces.
The object is illuminated from 4 different directions using domed diffuse structured light to reduce any interfering ambient light. It combines the speed of 2D image processing and the precision of 3D recognition. The shape from shading algorithms are integrated into the system software environment for automatic evaluation of the topographic images.
The optical 3D shape measurement detects even defects down to a few microns which significantly increases inspection accuracy. The separate inspection of texture and topography leads to a minimum of pseudo rejects which significantly reduces related costs since real defects such as scratches can be easily distinguished from supposed defects such as dirt on surfaces. With short cycle times inspection time can be reduced and productivity enhanced.
The trevista systems
STEMMER IMAGING can offer a choice of dedicated trevista systems. The trevistaCAM is a completely self-contained system that features an Adlink NEON 4 megapixel industrial smart camera and lens, preconfigured with either iNspect Express or Sherlock measurement software from Teledyne DALSA. The camera is integrated into a domed diffuse structured lighting trevista illumination system.
The camera can readily be integrated into a manufacturing process with standard interfaces for higher level control. The two levels of software provide integrators with the option of a system that can be deployed without great image processing experience, or one that provides an advanced, rich set of tools and capabilities to solve more challenging applications.
All shape from shading algorithms are included in the software. Applications include the identification of embossed datamatrix codes and characters (or even raised braille text). Modular CVS trevista systems are also available which provide the flexibility of upgrading modules (such as utilising a higher resolution camera) in order to react to changing requirements. Three CVS trevista variants are available.
The CVS trevista Surface system has a user-selectable area scan camera for the inspection of static parts with cycle times up to 200 parts per minute. The CVS trevista Cylinder system uses a line scan camera for the inspection of cylindrical components, while the CVS trevista Multiline system is designed for the inspection of moving or rotating components.
This is perfectly suited to inspection tasks in production line processes, and uses a freely selectable area scan camera which reads out the individual sensor lines.
www.stemmer-imaging.com