www.magazine-industry-usa.com
24
'19
Written on Modified on
'Bastion choses Renishaw to bring metal additive manufacturing in- house'
Global engineering technologies company, Renishaw, has supplied Bastion Cycles with an AM250 system to improve its in-house additive manufacturing (AM) capabilities.
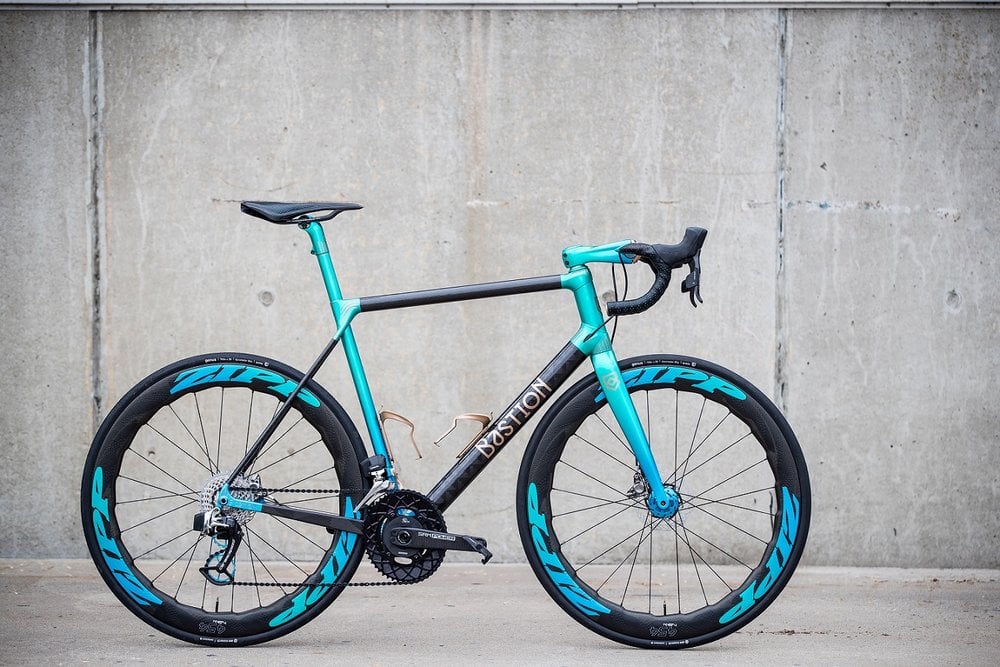
Bastion Cycles design, develop, trial and market a high-performance road bike which utilises a modular design of AM titanium lugs, paired with filament wound carbon fibre tubes. It prides itself on building premium bike frames locally in Australia using the latest technologies and materials.
The company originally outsourced some of the production process to a local AM bureau, which produced the titanium lugs for its bike frames. However, as sales and demand increased, the company decided to bring the AM process in-house.
Ben Schultz, James Woolcock and Dean McGeary, the founders of Bastion Cycles met with Mike Brown, General Manager at Renishaw Oceania, based near Melbourne, to find out about the Renishaw AM system.
Bastion Cycles tested this and three other machines from various suppliers but found that the AM250 produced the best surface finish, material performance and mass customisation capabilities.
The titanium lugs, printed on the AM system are unique to Bastion Cycles in their exploitation of very thin-walls, outer-skins and a structural internal lattice, resulting in an extremely high stiffness-to-weight AM part.
“Additive manufacturing is the secret to the customisation and performance of our bikes,” explained Ben Schultz, Managing Director at Bastion Cycles. “With the help of Renishaw's technology we were the first company in the world to design, develop, test and market a commercially viable, high performance road bicycle using additive manufacturing, something that we are very proud of.”
For the first three years of operation, Bastion Cycles outsourced production to RAM3D, an AM bureau, located in Tauranga, New Zealand. RAM3D also utilised the Renishaw AM250 platform to manufacture the titanium components of the bike frame to Bastion's supplied design. At the end of 2018, the decision was made by Bastion Cycles to bring the AM process in-house.
“We chose Renishaw to supply an AM system because of the support it could provide,” continued Schultz. “Australia has a fairly small AM market and Renishaw is the only company with a local headquarters with dedicated staff that could get an engineer to our site in a few hours. That is a valuable service for a small business like us,” added Ben Schultz.
“AM technology means we can design and manufacture parts that could not be produced using traditional bike manufacturing methods,” explained Mike Brown, General Manager at Renishaw Oceania.
“By using the AM system, Bastion Cycles is able to design, prototype and produce high-performance titanium lugs for its frames and meet the demand of its customers.”
www.renishaw.com