Next milestone in digital transformation: thyssenkrupp presents artificial intelligence "alfred”
thyssenkrupp Materials Services continues to drive digital transformation.
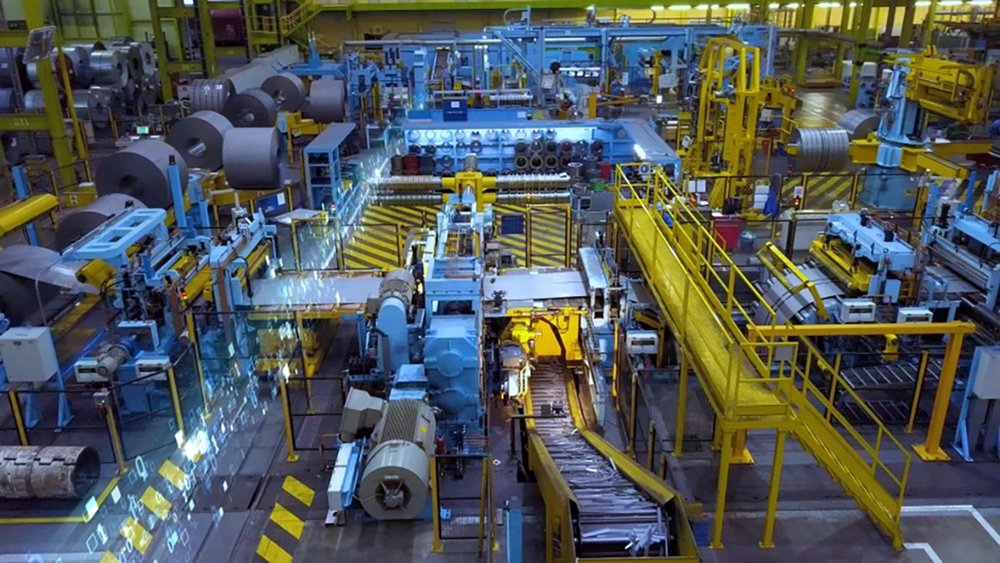
- thyssenkrupp Materials Services relies on Microsoft for in-house solution development
- AI as an essential component of the holistic digitalization strategy
- Customers benefit from individualized offers and more efficient processes
Since early 2019 an artificial intelligence solution (AI), supported by Microsoft’s cloud platform Azure, has been integrated into the processes of the largest materials distribution and service provider in the Western world. "alfred" supports his colleagues at Materials Services in dynamically managing the global logistics network with 271 warehouse sites and more than 150,000 products and services.
As with his namesake – Alfred Krupp – all information comes together at alfred. As a first step, alfred will help to optimize transport routes and thus save the transport of thousands of tons of material per year. In addition, materials will be available more quickly at the right locations in the future.
In the medium term, Materials Services will be able to make all processes along the supply chain more flexible, for example, in order to better take into account specific customer requirements for delivery speed, pricing or material quality.
Klaus Keysberg, CEO of thyssenkrupp Materials Services, summarizes alfred’s strengths: "Artificial intelligence is one of the technologies that will make a decisive contribution to competitiveness in materials distribution in the future.
With alfred we are taking an important step towards making our processes even more efficient and optimizing our value chain. At the same time, he gives us better insight into our customers' needs so that we can align our offerings accordingly. In the medium term, this holistic approach will also open up new business opportunities for us".
Using Big Data systematically
With the AI, the approximately 14 million order items received annually by Materials Services can be processed and analyzed much more efficiently. For the first time, the materials experts are also bringing all company data together on a single platform.
Using self-learning algorithms based on Microsoft Azure Machine Learning, alfred analyzes all relevant information, generates important findings and supports employees with appropriate recommendations:
Which materials have to be assigned to which industry? Where are materials processed? What would be the most intelligent transport route to supply the customers with materials in the best possible way? What are the needs of the individual locations? "The intention is very clear:
With alfred we are improving our own processes so that we can serve our customers all over the world more efficiently," says Axel Berger, Head of Digital Transformation Office at Materials Services.
The focus is on customer benefit
While we simplify cooperation with our suppliers in the area of procurement by means of a cloud-supported platform, for example, we create possibilities for networking internal machinery with our self-developed IIoT platform toii. toii allows us to flexibly coordinate and optimize the processes of warehousing and logistics.
In sales, we offer our customers access to 150,000 products and services at 271 warehouse sites sites in the world's largest virtual materials warehouse," says Klaus Keysberg.
As a link between all these areas, alfred fits into the ecosystem and ensures continuous optimization of speed and service quality through intelligent data processing with corresponding recommendations.
In the company's own Digital Transformation Office in Essen, all strands of digitalization flow together. Here, integrated teams of IT experts, engineers and business coordinators work under the direction of Axel Berger on various digitalization projects that arise directly from the core business of Materials Services – including alfred.
The materials experts were supported by Microsoft and its global cloud platform Azure. "Joining forces with Microsoft allows us to use advanced technologies for our in-house developments. This enables us to ensure that the projects are very closely linked to our core business on the one hand, and that they are technologically state-of-the-art on the other," says Axel Berger.
"At this point in history, manufacturers need to become digital companies to lead in their industries. thyssenkrupp Materials Services is not only adapting digital technologies, they are building their own digital capabilities and portfolio to elevate their logistics business with AI services to the next level.
They unlock new business opportunities by merging their industry know-how with the core of AI: large volumes of relevant data as well as strong machine learning methods and algorithms”, said Çağlayan Arkan, Global Lead Manufacturing & Resources, Microsoft.
Klaus Keysberg is also convinced of the synergies of the partnership. "The collaboration with Microsoft makes the implementation of projects like alfred much more efficient. Ultimately, it will enable us to apply our in-house developments more quickly, gather important insights there and develop new business models from them.
www.thyssenkrupp.com