ZF Aftermarket: Conserving resources is the best way to protect the climate
ZF Aftermarket presents remanufacturing success story at the ReMaTec in Hall 3, Booth 334 from 23-25 June in Amsterdam.
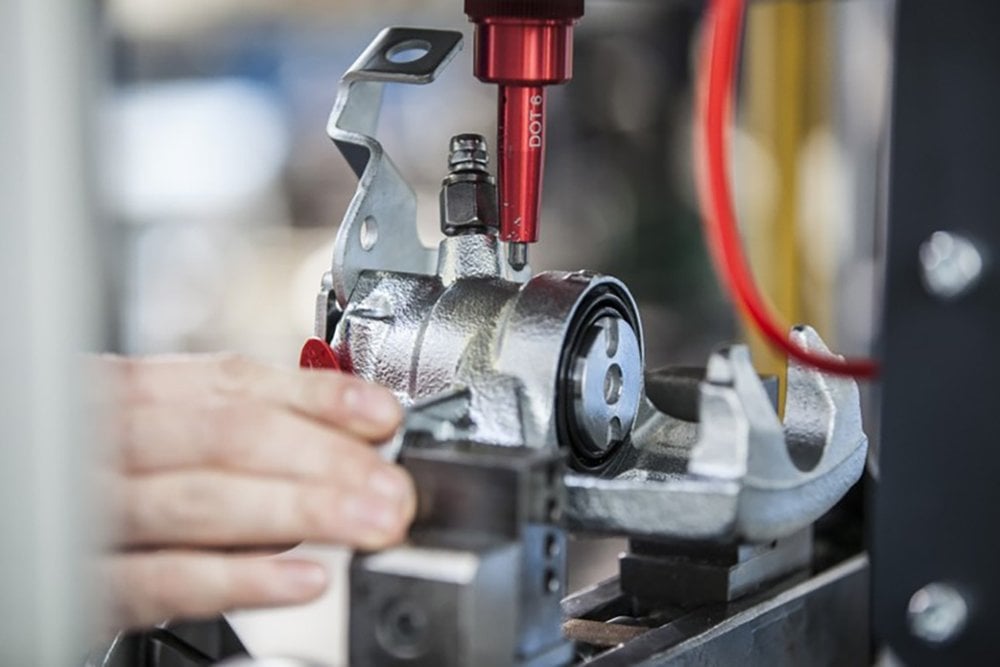
- Remanufacturing of vehicle components in 15 locations worldwide
- Sustainable savings of energy and material bring mobility in harmony with environment
Conserving resources is the best way to protect the climate. Remanufacturing makes it possible to save a great deal of energy and materials - compared with the supply of new parts. ZF anticipated this environmental goal very early in 1962 and has consequently expanded its remanufacturing program over the past years.
A broad range of vehicle components including brakes, transmissions, steering systems or torque converters is being remanufactured to original equipment quality at 15 locations – with the trend rising.
At the ReMaTec 2019, the world's leading remanufacturing trade show for industry professionals from 23 - 25 June in Amsterdam, ZF Aftermarket will not only present the overall remanufactured product portfolio but also highlight the whole success story of remanufacturing in the ZF group. The Cradle-to-Cradle certificate in gold is the accolade for sustainable production.
ZF has already received this award several time – the ZF location in Bielefeld for example for the remanufacturing of Sachs clutch pressure plates. For the certification according to the specifications of the Cradle to Cradle Products Innovation Institute based in Oakland, California, a manufacturer must reuse around 95 percent of the materials.
ZF Aftermarket convinces with quality and quantity. One example from Frýdlant, Czech Republic: More than 4,000,000 brake calipers or in other words around 766 brake calipers per working day, have been remanufactured at the ZF Aftermarket site, since the plant was founded in 1999.
“Together with our remanufacturing plant in Wrexham, Wales, we will bring the number of brake calipers produced in ZF Aftermarket production facilities to a new record level each year - namely 1,250,000 units," says Jirka Horvath, Director Operations & Remanufacturing Europe & EEMEA.
Remanufacturing – an industrial standard process
Remanufacturing begins in the workshop, by removing the old part from the vehicle. Arrived in one of the remanufacturing locations, ZF Aftermarket experts assess and evaluate the newcomer, dismantle and clean it. Then they sort out damaged individual components, dispose of them in an environmentally friendly manner or recycle them.
During assembly, ZF Aftermarket technicians replace defective and missing components with spare parts of original equipment quality, replace wearing parts, and update the software if necessary.
There are only deviations from the original series product quality if the current technology is more advanced than at the time of original equipment. In this case, a technical upgrade is included. Finally, the component is returned to the aftermarket with a new warranty, where it awaits its next use as a spare part.
“We call this process remanufacturing to emphasize that this is an industrial standard and not a repair job,” explains Erik Naumann, head of Manufacturing for the ZF Aftermarket Division.
He stresses that: “Natural resources are finite but our remanufacturing program allows us to reduce the demand for raw materials by up to 90 percent compared to manufacturing a new product. Additionally, we save about 90 percent in energy. These sustainable savings of energy and material bring mobility in harmony with environment and lowers also one's personal CO2 footprint.”
www.zf.com