www.magazine-industry-usa.com
06
'19
Written on Modified on
Complete Machining Services, INC. (CMS) Expands Capabilities to Include Micro Laser Welding for Mold Repair and Tool & Die Maintenance
The largest concentration of mold makers in North America is in Metropolitan Detroit, Michigan and Windsor Ontario.
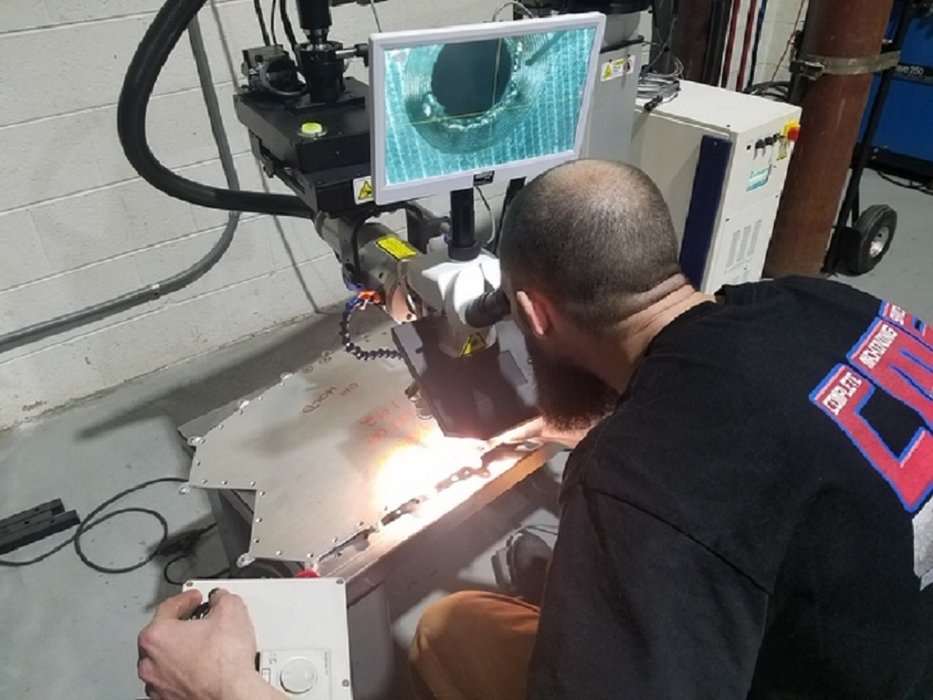
Over the past 15 years, CMS, Inc. has continued to target their precision machining and fabricating services to market demands. Having the ability to accomplish that typically includes the addition of state-of-the art capital equipment. For CMS, that includes 3,4 and 5-axis CNC milling machines. In some cases, it might be a new machine, or it can be a slightly used machine equipped with new tooling, controls and software upgrades.
Jeff Dainty, CMS president and CEO says, “When your business is contract machining and fabricating you have to have the right tools with the best level of technology to provide the needed high-quality parts manufacturing capability at a competitive cost…and delivered on time.”
Dainty adds, “Last year we began receiving numerous requests for plastic injection mold repair services. Beyond our MIG and TIG welders, this was a capability we did not have. It was obvious there was a lack of contract precision laser welding services in the area for plastic injection molds, which was surprising because the largest concentration of mold makers in North America resides in Windsor, Ontario and Detroit, Michigan, close to where CMS is located.
Coincidentally, my manufacturing manager and I were scheduled to attend the 2018 IMTS Show the following week in Chicago, so we went looking for the ideal laser welding systems for mold repair. After researching the laser welding systems at the Show, we settled on the LaserStar 8700-3 Series Universal Jig Welding Workstation, a micro welding laser system that was going to give CMS the high-quality capability for plastic injection mold repair.”
Gary Paresky, LaserStar regional sales manager, says “ When CMS talked to us at IMTS about expanding their capabilities by adding laser welding for plastic injection mold repair and also tool & die maintenance, we explained that they were going to need not just a laser welding machine, but a workstation that provided the flexibility to handle a wide variety of parts and materials.
That meant they needed at least 300-watt capability that could weld aluminum, and that means a fiber laser. YAG lasers are typically 200-watt devices. We directed them to our 8700-3 Series fiber laser welding workstation which provides high-peak power, optimal performance and throughput, and that means high up-time, exactly what a job shop like CMS needs.”
Paresky further explains “The fiber laser source on the 8700-3 has a permanently sealed design that protects against dust and dirt, which sometimes is an issue in a job shop environment. It does not require adjustment, has no consumable parts and requires basically no maintenance.
The technology of the fiber laser produces a sharp, focused light beam that consistently melts a very small area of metal. The benefit of the technology is that vey little heat is generated at the weld point, allowing users like CMS to easily laser weld >0.25 mm from complex, heat sensitive intricate parts.”
Jeff Dainty points out, “Because we needed to maximize the flexibility of the laser welder, we opted to add a number of options to the workstation that included a tower gantry for ease of moving the laser next to the molds, a motorized work table, and a camera and monitor to aid in training operators.
Fortunately for CMS, we were able to find an operator with experience using LaserStar equipment, so we were able to start putting work through the process right after it was installed, and we are now successfully producing mold repair work for a variety of customers, on a weekly basis.”
www.complete-machining.com