www.magazine-industry-usa.com
29
'19
Written on Modified on
Monitoring metal sheet infeed during the pressing process
A tool punch presses the plate to be formed into the mold (die).
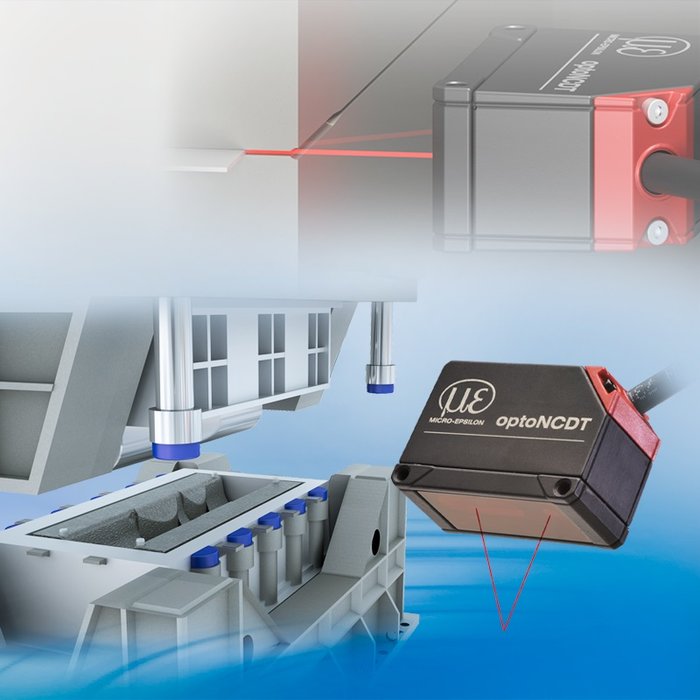
The measurement of the distortion is carried out using several optoNCDT 1420 laser triangulation sensors, which are placed around the metal sheet, either in the tool or on the side of the tool. Due to their extremely compact design, these sensors can be effortlessly integrated into a small space.
The arrangement is chosen in such a way that the laser beam measures on the edges of the sheet, which is between the top and bottom of the tool. Due to the extremely small measurement spot size, the laser is able to measure extremely tight gaps between the two tool parts of less than one millimeter.
The measured values are transmitted via analog or digitally to the controller. They allow a conclusion to be drawn on how much material has flowed. This enables, for example, the pressing force to be controlled during the ongoing process, reducing waste, material consumption, downtime and costs.
Even when exposed to harsh ambient conditions, laser triangulation sensors from Micro-Epsilon provide reliable measurement results. They are rugged and can withstand high mechanical loads such as vibration and shock. The Auto Target Compensation (ATC) feature rapidly compensates for different reflections caused by high-gloss through to dirty-matte sheet metal parts, while enabling a smooth distance signal.
www.micro-epsilon.com