www.magazine-industry-usa.com
24
'19
Written on Modified on
Erdemir group relies on Paul Wurth expertise for construction of two new Blast Furnaces
Paul Wurth has been awarded with orders for two new blast furnaces to be built by Erdemir Group, Turkey’s largest steelmaker, at their Ereğli and Iskenderun integrated steel plants. In both cases, one completely new furnace will replace an older production unit.
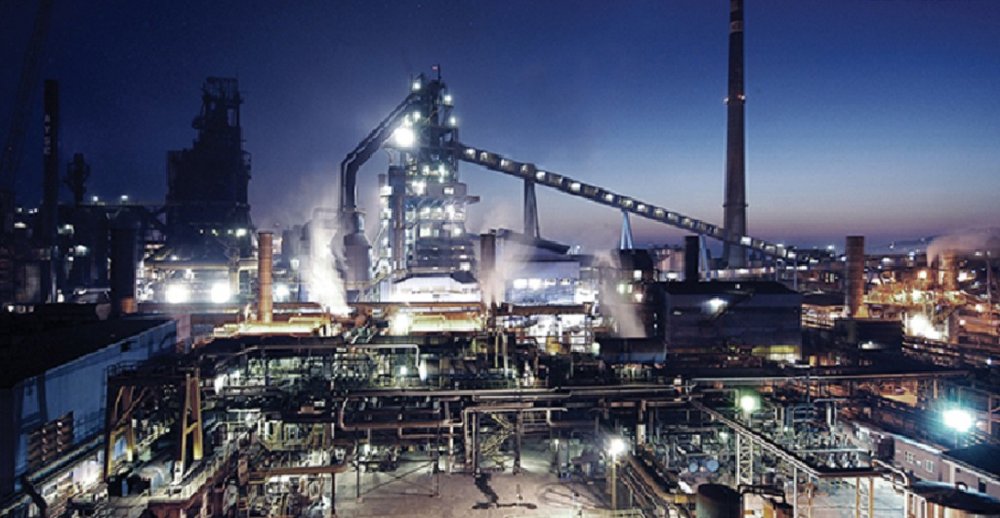
At Isdemir works in Iskenderun at the Mediterranean Sea, the new BF1 will be sized at 12.5 meters in the hearth and 3,587 cubic meters of inner volume; it will be fitted with 32 tuyeres and four tapholes and will produce 7,900 tons daily, which further increases the hot metal capacity at this site.
Paul Wurth will execute both projects on an EP basis including the supply of technological key items and related supervision of erection and commissioning. The orders include basic engineering of the blast furnaces with profile, cooling and lining concepts as well as the design of the stockhouses, top gas cleaning plants, slag granulation plants and BF cooling units.
Paul Wurth will provide detail engineering for some non-supply items like process vessels, especially (but not only) the BF shells, and for the piping of the BF cooling systems. While Erdemir’s new furnace will be plate cooled, the thin-wall concept with vertically arranged staves will be applied to the furnace at Isdemir.
For both furnaces, Paul Wurth will supply Bell Less Top® charging systems and bleeder valves, refractories for the hot blast mains and bustle pipes, tuyere stocks with tuyere phenomena detection system (TPDS), technological and critical items for the top gas cleaning plants (consisting of axial cyclones, annular gap scrubbers) as well as for in total three INBA® slag granulations systems.
Extensive sets of TMT* probes and process recorders include, inter alia, 3D TopScan™ burden surface profilemeters and SOMA™ acoustic top gas temperature measurement. Under the same contracts, TMT will also supply fully hydraulic taphole machinery for equipping all the six tapholes in total.
At Erdemir, some auxiliary plant units will be re-used fully or partially making necessary a certain scope of customized adaption engineering. In the case of Isdemir, Paul Wurth will additionally supply key items for the 4-stoves hot blast generation plant (Paul Wurth top-fired stoves), the common L1 automation of the BF plant and a Level 2 BFXpert® package.
Challenging project schedules foresee blow-in of the new blast furnaces for March 2021 (Erdemir) and May of the same year (Isdemir).
www.paulwurth.com