www.magazine-industry-usa.com
30
'19
Written on Modified on
Vises 2.0: The Return of the Modern Classics
Are vises old – "On the contrary!" say the clamping technology experts at SCHUNK.
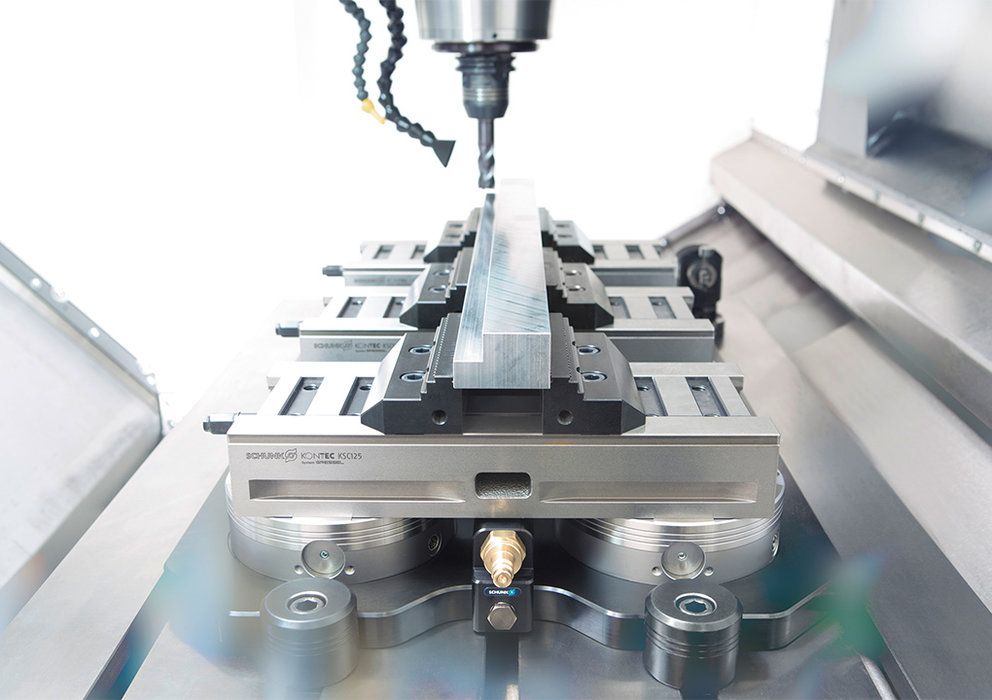
Just half a turn with the actuation key is enough to clamp workpieces process-reliably with grip jaws and a clamping depth of only 3 mm. Especially in modern production concepts with workpiece storage, the vises of the basic line serve as an economic basis for workpiece clamping. They provide valuable services on workpiece carrier pallets and tombstones in 24/7 operation.
Almost unnoticed by the public, the grip system, which eliminates additional work steps such as pre-embossing during raw part clamping, or quick adjustment of the clamping range, have found their way into production. Similar efficiency effects result in integrated quick-change interfaces: An interface to the quick-change pallet system allows the complete vise of the basic line to be exchanged in a matter of seconds with 100% repeat accuracy.
With the aid of a jaw quick-change system, workpiece-specific chuck jaws can be changed in just a few steps and a wide range of workpieces can be covered.
Large system program
The manually operated vises of the basic line of the SCHUNK KONTEC KSC series are highly efficient all-rounders for the machining of raw materials and finished parts. Its drive is provided by a spindle protected within a completely closed system. The vises can be easily and quickly operated with a torque wrench. Even with comparatively low torque, they achieve high clamping forces of up to 50 kN (size 160).
As the clamping takes place by tension, the bending load on the base body and thereby the lifting up of the vises are minimized, which adds to the accuracy and rigidity of the clamping.
A special feature of the SCHUNK vise of the basic line is the modular structure of the portfolio, which covers a wide variety of standard applications. The attractively priced clamping systems are available in three basic variants:
Centric clamping vises: The manual centric clamping vise KONTEC KSC is a multi-talent among the stationary workholding systems. From conventional clamping, low clamping depths for 5-sided machining, molded parts, plates or saw cuts: the KONTEC KSC is adapted in the twinkling of an eye and ensures high precision and high clamping forces in an extremely flat design. Workpieces can be reliably clamped in less than one second.
A preloaded center bearing free from play, as well as and fitted slides ensure a repeat accuracy of up to +/- 0.01 mm, enabling precise raw and finished part machining in a single clamping system. The fully encapsulated drive and an integrated chip outlet ensure particularly high process stability and minimum wear. As an attractively priced component, the KONTEC KSC enables particularly economical pallet storage equipment.
Single-acting vise: The KONTEC KSC-F single-acting vise with fixed jaw is specially designed for the use in automated machine loading. It scores with its quick setting of the clamping range, its flat design, and low weight – perfect prerequisites for the use in all machining centers. Due to the 160° quick clamping, workpieces are clamped precisely in no time at all with the torque wrench and the vise is securely locked.
The sizes KSC-F 80, KSC-F 125, and KSC-F 160 were designed specifically for the common pallet sizes 320 x 320 mm, 400 x 400 mm and 500 x 500 mm.
Double-acting vise: The KONTEC KSC-D is a light and flat double-acting vise, which is especially designed for demanding continuous operation in automated machine tools with workpiece storage. By means of a convenient third-hand function, two workpieces can be inserted next to each other for instance on tombstones, fixed, and securely clamped together. Due to the trapezoidal threads, high clamping forces can be achieved with little manual effort.
An induction-hardened base body, long jaw guidance, fitted slides, case-hardened chuck jaws, and a fully encapsulated drive ensure a high degree of precision, maximum wear resistance, and minimum cleaning effort. Completely nickel-plated, the vises are perfectly protected against corrosion for continuous operation in pallet systems or on tombstones.
Clever quick-change functions
All three variants are available in sizes 80, 125, and 160 with different base body lengths. On the workpiece side, users can choose from a large standard top jaw program, ensuring maximum flexibility. Due to the quick-change jaw system, both standard jaws and workpiece-specific jaws can be exchanged in just a few steps. Depending on the size, the vises cover enormously large clamping ranges between 0 and 458 mm (KSC), 0 and 463 mm (KSC-F), and 0 and 331 mm (KSC-D, two workpieces) via reversible jaws.
In order to minimize set-up times, KONTEC KSC vises from the basic line can be combined with the SCHUNK quick-change pallet system VERO-S. For this purpose, the clamping pins of the quick-change pallet system without adapter plate are directly mounted in the base body of the vise. It is thus possible to load the vises on the machine table, on tombstones or clamping pyramids within seconds and with maximum repeat accuracy. Again, the flat design of the KSC series pays off. For clamping long parts, several KSC vises can be combined.
Magnetic workpiece supports and stops
For EMO 2019, SCHUNK has expanded its base clamp program to include two useful extras: magnetic workpiece supports in different heights can be placed on the clamps in just a few steps without the need for screws. They ensure a defined clamping depth with a height accuracy of +/- 0.01 mm, maximizing parallelism of the bearing surface. In addition, the magnetic holding force prevents the supports from changing their position or falling out during the workpiece change.
Because the bearings are quickly and easily attached or removed, the first and second set-ups can be repeated on a single vise without the need for a jaw change. The magnetic stops are mounted and adjusted just as quickly, guaranteeing the exact position of the workpieces and a high repeat accuracy.
schunk.com