Future-proof your factory with high-density barcode verifiers
The most advanced laser marking technology on the market today can produce codes barely visible to the human eye.
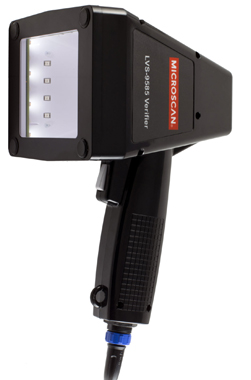
The cell size for a two-dimensional barcode can now be as small as 2 mil – or just two thousandths of an inch. That’s about the width of a single human hair.
Miniscule barcodes are often essential for adding necessary identifying information in machine-readable form to crowded printed circuit boards (PCBs) and other items with little room for larger symbols. Surgical instruments and similar medical devices also tend to have minimal space available for barcodes, and the automotive industry also frequently makes use of extremely compact laser markings.
Staying one step ahead
Although international standards organization GS1 currently lists the minimum allowed cell size, or x-dimension, for direct part marks (DPMs) on medical devices as 3.9 mil, it’s quite likely that this specification will be lowered in the coming years. That’s why it’s important for manufacturers to invest in high-density barcode verifiers and be one step ahead of today’s expectations.
Omron offers a couple of options for high-density barcode verification. The LVS-9580-HD and LVS-9585-HD handheld barcode verifiers have recently been updated with high-definition lenses that bring the minimum verifiable code size down to 2 mil. This advanced technology ensures that manufacturers can take on any verification challenge of today and tomorrow.
With advanced lighting and powerful software, the LVS-9580-HD and LVS-9585-HD verifiers test both DPMs and printed labels to a variety of global standards and provide comprehensive reporting. Their auto-find feature automatically locates symbols and cycles through illumination settings to find the one that works best.
Why verification is essential
To ensure that poorly formed markings don’t slow production down with no-reads, it’s essential to verify all DPMs and printed barcodes to all the relevant quality standards. In many cases, markings need to be readable not just throughout the production process but throughout the supply chain as well – or even throughout a part’s entire service life.
To make sure barcodes start off with a sufficiently high level of quality, it’s necessary to verify them thoroughly according to standards developed by the International Organization for Standardization (ISO). More than simply validating that the imagers on hand can read a code, verification is a complex process that grades codes against several key ISO standards.
For two-dimensional barcodes and DPMs, these standards include:
- symbol contrast, the intensity difference between light and dark cells
- modulation, the degree to which contrast varies throughout the symbol
- print growth, the degree to which one cell type is larger or smaller than the other
- and several more
Production materials often place a limit on the grade that a marking can achieve. For example, slight changes in the color of a PCB can make it impossible to apply a laser marking that gets a perfect score for contrast. Applying DPMs to shiny or curved surfaces will also be unlikely to get a high grade. Sometimes, however, that’s the best you can do.
With high-resolution markings and ultra-high-density barcode verifiers, manufacturers in many industries – including consumer electronics and medical device manufacturing – have far more options for code placement. Omron’s verifier upgrade helps ensure that companies can take full advantage of the new flexibility offered by today’s advanced laser marking equipment.
www.omron.com