www.magazine-industry-usa.com
05
'10
Written on Modified on
Composite Connectors qualified by ESA Space Applications
Souriau, the worldwide leader of composite connectors for severe environments has obtained the qualification of the European Space Agency (ESA) for its rectangular miniature range: microComp®. The microComp® connector is the perfect replacement for ESA/ESCC D-Sub connector, which is widely used today in satellite payloads. The microComp® allows a space saving up to 40% and a weight reduction down to 60%.
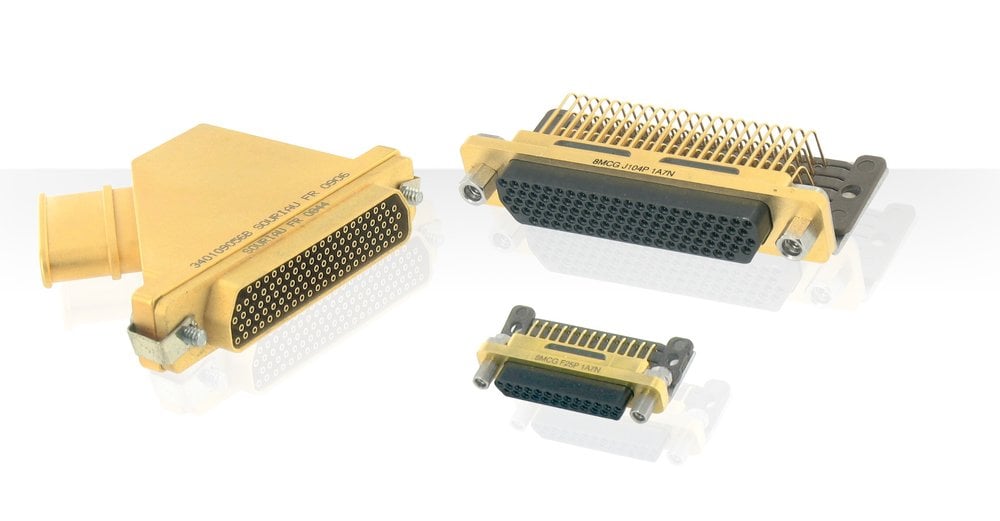
Connectors currently used on equipment and harnesses of telecommunication satellites or scientific missions are of the same type as those on laptop and home computers. These connectors, commonly called D-Subminiature, use materials and manufacturing processes which are more than 40 years old and do not take advantage of the miniaturization trend In the electronics industry.
Reliability is the key word in the space industry - for both launchers and satellites. All the mounted components have to be qualified and are subject to an extensive manufacturing follow-up with full traceability. This traceability permits the identification of the batch of raw material in case of failure in order to isolate the potentially defective components.
In this context, Souriau worked in partnership with the European Space Agency to develop a complete range of rectangular connectors in composite material for the space environment.
Composite material is the best solution for coping with miniaturization and mass saving trends in on-board equipment. Souriau is at the forefront of this technology and is already a major supplier of composite connectors for all new generation of airplanes.
Since the end of 1980s, Souriau has worked on the choice of composite materials and their characterization. As a result, Souriau has developed expertise in composites, both in their formulation and in the industrial processes like high pressure moulding, and of the adhesion of metallic coating (nickel, gold) on these composite materials.
For this new rectangular range microComp®, the complete shell is made of composite and metalized in order to ensure an effective electrical continuity between the plug, the receptacle, the backshells and the harness braid. This is essential to provide good protection of the transmitted signals against electromagnetic interference. The electrical crimp contacts are removable and allow the user to wire and unwire their equipment. It gives flexibility and saves cost during the development phase.
Contact :
Bertrand GAUTHIER
microComp® Product Manager
Tel.: + 33 1 45 10 78 39 This email address is being protected from spambots. You need JavaScript enabled to view it.
Reliability is the key word in the space industry - for both launchers and satellites. All the mounted components have to be qualified and are subject to an extensive manufacturing follow-up with full traceability. This traceability permits the identification of the batch of raw material in case of failure in order to isolate the potentially defective components.
In this context, Souriau worked in partnership with the European Space Agency to develop a complete range of rectangular connectors in composite material for the space environment.
Composite material is the best solution for coping with miniaturization and mass saving trends in on-board equipment. Souriau is at the forefront of this technology and is already a major supplier of composite connectors for all new generation of airplanes.
Since the end of 1980s, Souriau has worked on the choice of composite materials and their characterization. As a result, Souriau has developed expertise in composites, both in their formulation and in the industrial processes like high pressure moulding, and of the adhesion of metallic coating (nickel, gold) on these composite materials.
For this new rectangular range microComp®, the complete shell is made of composite and metalized in order to ensure an effective electrical continuity between the plug, the receptacle, the backshells and the harness braid. This is essential to provide good protection of the transmitted signals against electromagnetic interference. The electrical crimp contacts are removable and allow the user to wire and unwire their equipment. It gives flexibility and saves cost during the development phase.
Contact :
Bertrand GAUTHIER
microComp® Product Manager
Tel.: + 33 1 45 10 78 39 This email address is being protected from spambots. You need JavaScript enabled to view it.