THE SHIFT FROM 2D TO 3D INSPECTION
In order to meet the demands of emerging quality control applications, the industry is undergoing a fundamental transition from 2D to 3D technology.
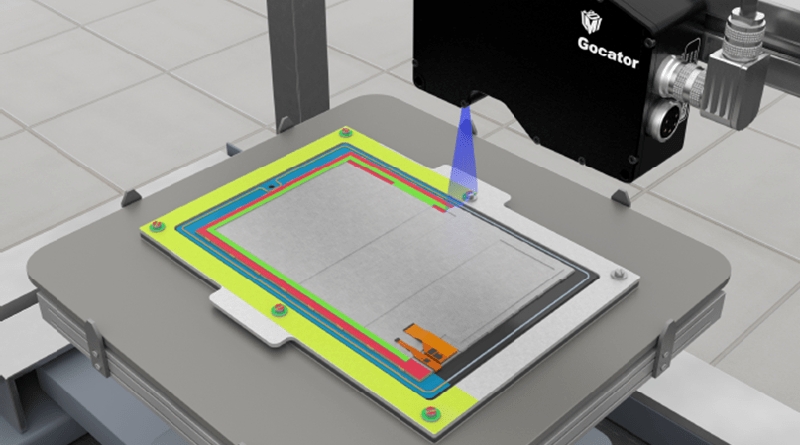
The reason? There are many applications where 3D is the only viable solution for automated quality control. As the level of automation increases and product quality becomes more critical given the high volume and cost of goods in industries such as automotive and consumer electronics, there is a corresponding increase in production processes that require the use of 3D.
For example, 2D technology cannot be used for adhesive and sealant inspection because 2D vision is unable to distinguish transparent glues from the surrounding material. In addition, 2D is unable to measure height data and volume. 3D smart sensors on the other hand are capable of providing high-resolution height data, which allows users to accurately determine glue bead location and volume.
Another application is battery inspection, which is a critical process from both a safety and a reliability point of view. Once again, 3D provides the necessary height data, while 2D does not measure flatness and cannot perform the inspection required to ensure proper battery assembly (i.e., proper weld seams). 2D solutions are also typically component-based and have a higher total cost of ownership than all-in-one 3D solutions.
3D is also a natural solution over 2D in robotic applications such as bin-picking. Manufacturing is moving rapidly into these types of robotic applications, further driving the need for robust 3D solutions as the global industrial world moves toward increased automation with robots.
3D vision provides a deeper layer of data that is essential to robust inspection. As a result, 3D solutions will continue to evolve as more quality control applications emerge that require their unique capabilities.