www.magazine-industry-usa.com
26
'18
Written on Modified on
Driverless on the race track with Dunkermotoren
Autonomous driving - a term that is currently the subject of many discussions and conversations.
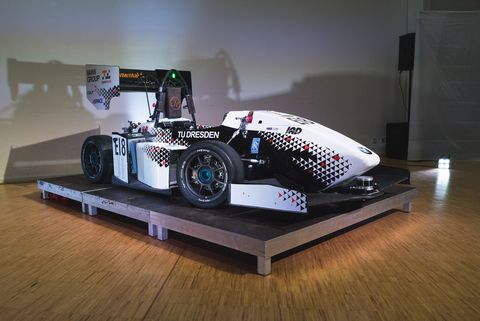
The origin of the developments was the Formula Student design competition in which the charitable association Elbflorace Formula Student Team TU Dresden e. V. takes part and competes against teams from other universities. The association was founded in 2006 by some students of the TU Dresden with the aim to promote the further education of the students during their academic education.
Initially, the association built racing cars with combustion engines from 2007 to 2009. By supplementing the electric class in 2010, the association then decided to switch to racing cars with electric motor solutions. A class for autonomous racing cars followed in 2017. In contrast to the changeover in 2010, it was decided in 2017 to add the autonomous racing class to the electric class.
As a result the team has been working on the development of an autonomous racing car. The aim was to participate in the Formula Student Driverless 2018 at the Hockenheimring with this electrically powered formula racing car.
The main supporter, participant and organizer of Formula Student is the automotive industry. Accordingly, it also contributes trends from automotive development to competition, including autonomous driving.
Together with SKF Actuation System AG in Liestal, Switzerland, Dunkermotoren realizes the brake unit in the autonomous racing car. The linear unit consisting of an electric cylinder CASM 32 and the brushless DC motor BG 45x30 CI, which are responsible for actuating the brake pedal.
The principle is quite banal: If the piston of the cylinder moves out, it presses on the upper end of the brake pedal, if the piston moves in again, the pedal is released. The concept immediately convinced the participants, because the actuating speed and the forces that could be achieved matched perfectly.
An environmental sensor on the front of the formula racing car recognizes the distance to obstacles in the environment. The measured distances are processed in an integrated computer which calculates the distance to be covered. After that the computer uses CAN communication to control the drive motors and actuators for steering and braking so that the vehicle follows the track.
But how do the entire sensor acquisition and the path calculation of the formula racing car work? As already explained, the environmental sensor detects the distance to obstacles in the environment. For example, the distance to pylons on the racetrack.
This information is processed by calculating a mesh of triangles and placing it over the pylons. Now the formula racing car drives along all the centers of the triangle edges. This ensures that none of the pylons is bypassed.
After several weeks of testing, the TU Dresden race car was used for the first time at a race event on the Riccardo Paletti Circuit in Varano de' Melegari in Italy. The team used the event preparing the Formula Student Driverless at the Hockenheimring. The team was quite satisfied with the result, because other teams are already building their formula cars one year longer.
This year, the priorities for the construction of the racing car were predominantly on a stable, modular autonomous system - reliability before performance. The team will participate again in the Formula Student Driverless at the Hockenheimring in 2019, therefore the whole concept will be further developed. These developments relate predominantly to the software.
The hardware, which also includes the CASM electric lifting cylinder with the BG 45 CI, was deliberately selected, so that there are no limits set to the top. The physical limits of the basic vehicle can be fully exploited, so that, for example, all tires can be blocked. The CASM cylinder can easily apply the required force.
Due to the high extension speed of the cylinder, there are no disadvantages compared to braking by a driver. Therefore the electric lifting cylinder is the perfect solution for the brake unit.
We wish the Team Elbflorace of the TU Dresden all the best for the future and hope for a great competition at the Formula Student Driverless 2019.
www.dunkermotoren.com