www.magazine-industry-usa.com
10
'18
Written on Modified on
Boom! This car’s ready to go!
A lean team of young engineers at Vancouver-based Electra Meccanica designed, simulated, and manufactured its new electric car in two years using Siemens software
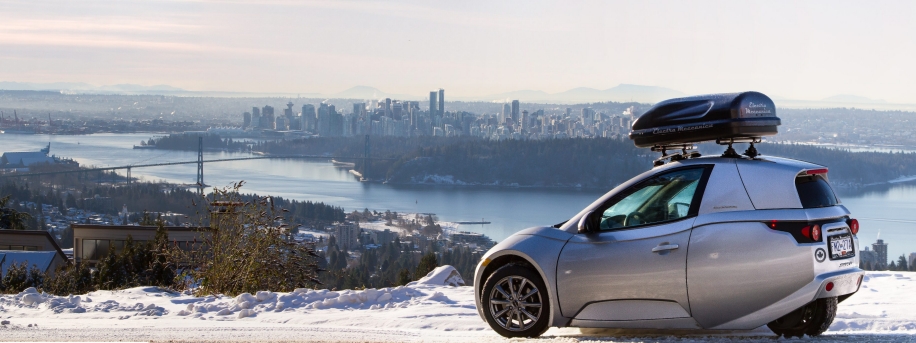
“We knew right away that if we were going to try to stay within any kind of timeline, there was never a chance that we would be doing this on paper,” says Henry Reisner, President Intermeccanica International. “It had to go from a sketch into a digital design immediately.”
Reisner’s parents started the company in Turin, Italy, in 1959. He remembers that by the age of 16 he was working on an almost daily basis with his father, and he’s been developing the company ever since.
Two friends, one great idea
Working with his business partner and friend Jerry Kroll, President and CEO of Electra Meccanica, the idea was born to develop a completely new and innovative car: a single-passenger, three-wheeled electric commuter vehicle.
Even experienced experts in the automotive business were skeptical. “We were told that automotive firms have 200 engineers in a room and that it takes them a year and a half to design a tail-light,” says Ed Theobald, General Manager of Electra Meccanica. But the company’s success with this car proved that their idea could work: “We just designed the whole car.”
Obtaining the tools for engineering excellence
Rich Hoyle is Principal Engineer, Aligned CAE. He joined the team to do finite element analysis, chassis design, and development. “What we see is a totally different way of thinking and approaching problems in these smaller companies. They have small budgets, but they have more nimble teams,” Hoyle says. “What they try to do is acquire the tools that will help them achieve engineering excellence on a small budget with small teams. NX and Simcenter allow them to do exactly that.”
Better value for the end buyer
The potential of the PLM software was unknown to the management before they began. “We brought in some fresh-scrubbed young engineers in mechatronics, mechanical engineering, and electrical engineering,” Kroll remembers. “The team has done a fantastic job of pulling in what they know as well as what Henry and I didn’t know. They told us that if we could get them this software, it would be awesome: faster to market, fewer errors, a better value for the end consumer of the car.”
Saving lots of time and money
One of the software-loving team members is Tammy Yu, Mechanical Engineer at Electra Meccanica. “Simcenter helps a lot with certification, predicting what might go wrong. And it helps us accelerate the process,” she says. “If we were to send the whole assembly out for testing and it comes back with feedback that it failed, that would take two or three months. If I do an analysis on it, that only takes a week or two to set up. That’s much faster and saves a lot of time and money.”
A 3D printer is also having a great impact on the company’s design processes. “With Siemens and a 3D printer, we can design a part and print it out,” Yu says. “We can get the part the next day or even two or three hours later and put it right in the car.”
Having all their data in one system is another benefit of using PLM software. “We have a fully parametric link into our CAM software, which is inside NX as well, and then straight to our CNC machining center,” Hoyle says. “With Simcenter, we have a direct parametric link back to the CAD data, all in the same GUI (graphical user interface). That means we can analyze and work on the design to see, for example, whether we can remove something to reduce its mass; then we go back into the design, iterate it, and with two clicks we have our results updated.”
Software that makes life easier
Electra Meccanica has big plans: 75,000 SOLO cars are planned to be released in the next three years, and the company is reaching out to more and more manufacturing people. “When I speak to a top-level manufacturer and tell them what software we used to fully design and engineer our car, it makes both of our lives a lot easier when it comes to delivering those cars to consumers,” Kroll says.
Inside the company, the software has enriched the exchange of ideas and methods. “The engineers are so inspired that we all come up with new ideas all the time. And from the sketch it just takes an instant and – boom – it’s ready to go. That’s amazing,” Kroll says. “You’re literally unlocking the potential of the human being to not just think of a solution that will work, but to immediately create it. And there’s magic in that.”
www.siemens.com