www.magazine-industry-usa.com
01
'18
Written on Modified on
Human-robot collaboration.Teaming up with machines for more flexibility
What are the benefits of human-robot collaboration?
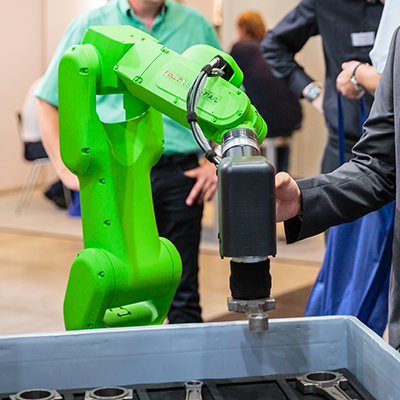
However, the emergence of the collaborative robot is redefining human-robot relations. No longer hemmed in by fences, this new breed of robots is safe and smart enough to work with or alongside humans across a variety of manufacturing environments.
Aside from the obvious floor-space savings, human-robot collaboration offers manufacturers many advantages. By taking over the laborious, repetitive and potentially dangerous tasks, collaborative robots improve working conditions for humans and allow them to focus on higher-value tasks that require manual dexterity and human ingenuity. This opens up a whole new world of possibilities for more efficient and flexible working.
So how do collaborative robots keep humans safe?
Unlike conventional industrial robots, collaborative robots are equipped with advanced sensor technology that enables them to interact safely with humans. In addition to monitoring the robot’s position and speed, these sensors stop and retract the robot safely should contact occur with a human.
Additional safety features prevent the robot from trapping body parts such as limbs and fingers, and allow the human to simply push the robot back should it get too close. Passive safety features include no sharp edges and soft covers on some models. All FANUC collaborative robots are certified to ISO safety standards.
Secondary suppliers also provide dedicated grippers for collaborative robots that ensure humans remain safe should they make contact with the gripper.
What about programming them?
Programming FANUC collaborative robots is just like teaching any other FANUC robot and can be done easily using the FANUC Teach Pendant or offline device.
By using the FANUC Hand Guidance option, the operator can even program the robot by leading it through and recording the motion points or trajectory necessary to complete the task.
How does human-robot collaboration benefit your business?
Human-robot collaboration can add benefit your business in many ways. One of these is improved working conditions for humans. With collaborative robots on the team, humans no longer need to complete physically demanding tasks and are free to focus on more rewarding work. As a result, humans stay physically healthy for longer and issues, such as repetitive strain and other work-related injuries, cease to be a problem. Human-robot collaboration also goes some way to easing the problems associated with ageing populations in industrial societies.
Moreover, Human-robot collaboration provides manufacturers with a much greater degree of flexibility. Not only are collaborative robots easy to integrate into existing production environments but they also occupy a smaller footprint versus traditional robot work cells.
Compared to fully automated solutions, collaborative robots are very cost effective – something that makes them attractive to SMEs and other companies that might not have thought about investing in automation. On top of this, they allow businesses to make better use of human staff and, thanks to easy programming and fast setup times, provide a viable option on small production runs. Future-proofed, they are fully Industry 4.0 ready and make processes more transparent and sustainable.
What applications are collaborative robots best suited to?
Collaborative robots are ideally suited to a whole range of industrial applications. Wherever they are used, their strength, precision and repeatability compliment human skills perfectly.
On machining and assembly lines, they prevent humans from having to lift and position heavy components. They are also ideally suited to machine-tending applications that frequently require an operator’s presence. In addition, since they do not need safety fences, they can be moved easily between machine tools.
Eliminating the need for an additional workstation, collaborative robots also provide an efficient way to conduct seamless quality control checks as part of the overall handling process.
They are also great at carrying out dull, repetitive, dirty and dangerous handling tasks on packaging and palletising lines that are unpopular with humans but cannot feasibly be done in a dedicated robot cell.
Whether they are used to apply sealants, adhesives, paints or other fluids, collaborative robots can also work safely next to humans across a range of dispensing processes.
www.fanuc.com