www.magazine-industry-usa.com
31
'18
Written on Modified on
Getting into Position
With a vast array of clamping, positioning and workholding methods available, how do you go about choosing the right one? Paul Mulvey, UK Sales Director of norelem UK, explains what to look for when deciding.
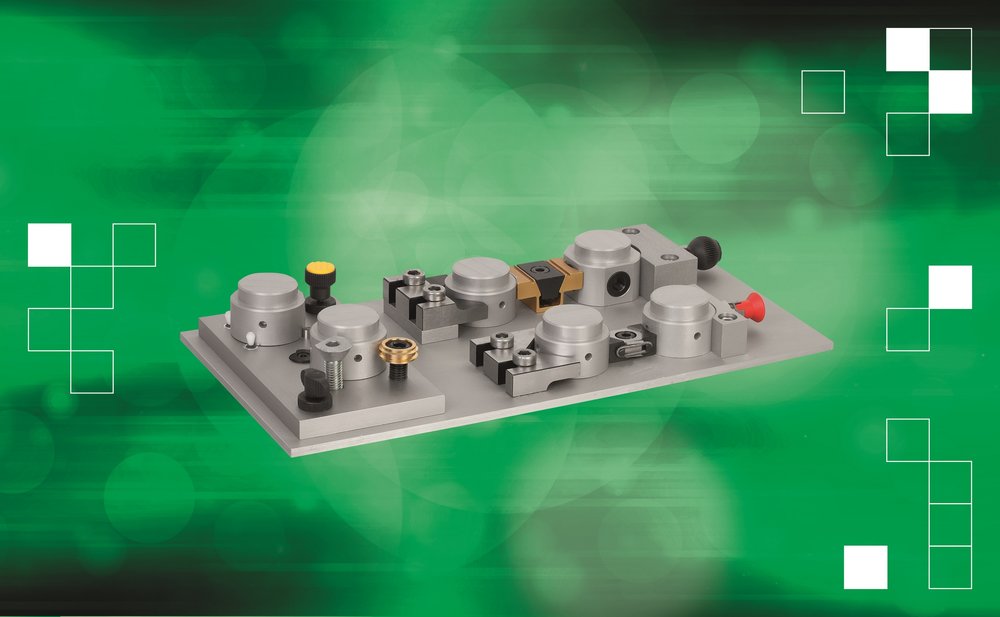
Of course, the more parts, the more important efficiency in the manufacturing process becomes to meet demand.
This begs the question. Are our factories working as efficiently as possible? Especially when it comes to the basic functions of clamping, positioning and workholding?
While workholding can seem small and insignificant, in reality it contributes greatly to commercial success. With consistent workholding processes, employees can increase their productivity, reduce downtime, decrease potential strain-related injuries and layoff, and reduce the need for setting clamps into position.
There are many hundreds of different workholding methods available. Selecting the right one often comes down to usage, flexibility, comfort, space, and efficiency. Here are some of the choices and methods available, and where you would use them.
Wedge Clamps (machinable)
Wedge clamps work by holding two workpieces together simultaneously. The first big feature of wedge clamps is that there are no protruding edges on the working surface through the clamping elements.
This benefits users by not obstructing them during their operation of job, and because of their compact design they are space-saving on the work surfaces.
Secondly, as explained, two workpieces can be held together at once. This is much more efficient if you need to machine two workpieces in one pass, and saves you from having to reposition for the next workpiece. Tightening the screw forces the jaws outwards, meaning you have an equal positive clamping force on both pieces, left and right of the clamp.
When buying wedge clamps, look for ones which have milling allowances on the jaws, such as the various wedge clamps from norelem’s range. These wedge clamps can be milled down to a desired form and size and ensures the workpieces can be clamped stress-free around their shape. Therefore, there is a reduced risk of stress-damage and breakage to the workpiece.
Precision Indexing Plungers
Indexing plungers, also known as cam action indexing plungers, are amongst the standardised construction components that allow moving machine components to be adjusted quickly. Pulling the pull-button or pull-ring retracts a pin from the counter piece so that machine parts can be put in the suitable position and then clamped again.
These are most suited for applications where a high repeat accuracy is required, along with rapid positioning. Ensure you use indexing plungers made from steel or stainless steel. These will provide higher levels of stability and corrosion resistance.
Lateral Spring Plungers
Lateral spring plungers are designed to position and hold flat, round or irregularly shaped workpieces in tight spaces.
Due to the way they can ‘spring’ back to accommodate the workpiece that is inserted, these are ideal for a variety of applications, including engraving, labelling, fittings, assembling, welding, soldering, drilling and reaming.
Cam Screws and Talon Grips
If you are working on rough surfaces, then cam screws are an ideal clamping solution.
Cam screws, which are also called fixture clamps, can be combined to solve numerous clamping problems in fixtures and equipment construction. One of the big benefits of this clamping method is the minimal height that cam screws offer.
Use cam screws with brass hex washers, as these will offer a gentle yet extremely stable and safe clamping of workpieces. Entire pallets can be set up by combining cam screws together. Main applications of cam screw clamping will be in saw cuts, castings and forgings.
Talon grips, on the other hand, are meant to bite into the workpiece. Talon grips will be installed into vice jaw plates, and a tapped hole with counterbore is sufficient for the mounting.
How talon grips work is that the sharp edges on the talons (hence the name) will bite down onto the workpiece and once secured, it prevents lateral and horizontal movement.
The low clamping height of talon grips (for example, a clamping height of 1.5mm is specified on norelem’s talon grips), saves on material costs, making this a cost effective clamping solution.
Talon grips are especially useful for round, contoured or oversized workpieces, which can be quickly and securely clamped down and fits around the form of the workpiece.
Looking at use
As Shigeo Shingo, the Japanese industrial engineer who is considered as one of the world leading experts on manufacturing practices, once said, “The most dangerous kind of waste is the waste we do not recognise.”
The foundation of engineering and manufacturing is always improvement, no matter how small and incremental. This boils all the way down to the way we work and clamping and positioning is no different.
Whenever we are undertaking workholding it is always important to first understand the workpieces that you’ll be working with, and the goal – is it accuracy, speed, flexibility, efficiency, secure clamping forces, or all the above? From this, you can then determine what the best clamping and positioning method will be.
Whether it is awkward workpieces, high volume production, or space saving solutions, norelem can work with you to find the best method for your application.
To learn more about norelem and its range of standard components, visit www.norelem.co.uk.