www.magazine-industry-usa.com
07
'25
Written on Modified on
Why ToF cameras are ideal for industrial automation applications
E-con Systems explores how ToF cameras enhance industrial automation with precision and efficiency, reshaping daily operations in factories and warehouses.
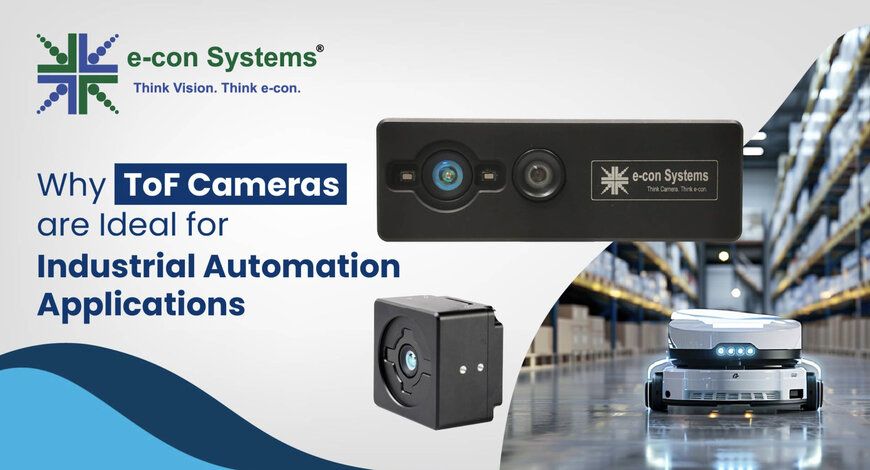
Time-of-Flight (ToF) cameras are transforming industrial automation by bringing a new dimension of accuracy and consistency to tasks that rely on spatial awareness. They capture depth information by measuring the time it takes for light pulses to reflect off objects, enabling highly accurate 3D mapping.
From streamlining complex assembly lines to improving quality control, ToF cameras are paving the way for smarter, faster, and more reliable automation solutions. The market has also clearly noticed this trend, as many reports are touting the growth potential. A recent report estimates the ToF sensor market size to grow from $5.52 billion in 2024 to $10.12 billion by 2029 (at a CAGR of 21.07%).
Understanding Time-of-Flight Sensors
ToF sensors determine depth by measuring the time that the light takes to go from the camera to an object and back. This measurement is converted into distance information, enabling the creation of detailed 3D maps of a scene.
These sensors emit near-infrared (NIR) light, which reflects off surfaces and returns to the sensor. By calculating the delay, the sensor provides accurate depth data unaffected by variations in textures or lighting conditions. This capability makes ToF sensors a preferred choice for applications requiring precise and fast spatial measurements.
Key Components of a ToF Camera
ToF cameras are composed of three components: the illumination module, the ToF sensor, and the depth processor.
Illumination module
The illumination module emits modulated light, typically in the NIR range, to illuminate the scene. Common wavelengths include 850nm and 940nm, chosen for their ability to operate reliably in diverse environments. The light source is usually a laser diode or LED, and a diffuser ensures the emitted light matches the camera's field of view. A laser driver is responsible for controlling the rise and fall times of the light waveform, which is crucial for accurate measurements.
The design of the illumination module allows ToF cameras to function seamlessly in both low-light and brightly lit environments, making it highly adaptable across various applications.
ToF sensor
The ToF sensor is the central component that captures the reflected light and converts it into depth information. It is engineered to collect light efficiently and measure its return time with high accuracy. To enhance its functionality, the sensor is paired with optics featuring a wide aperture for maximum light collection.
Also, a band-pass filter is integrated into the sensor module. This filter allows only specific wavelengths of light, such as 850nm or 940nm, to pass through while blocking unwanted interference. This capability ensures that the depth data remains reliable, even in challenging scenarios.
Depth processor
The depth processor is tasked with converting raw pixel data into usable depth information. It analyzes the phase and time delay of the captured light signals, generating a detailed depth map of the scene. The processor also performs critical tasks such as noise reduction and distortion correction.
In addition to creating depth data, the processor outputs a passive 2D infrared image. This adds another layer of functionality, enabling applications like object detection, tracking, and gesture recognition.
How ToF Cameras Can Overcome Multiple Camera Interference
Multiple Camera Interference (MCI) is a common challenge in environments where multiple Time-of-Flight (ToF) cameras operate simultaneously. These cameras rely on emitting and receiving light signals to calculate depth. Still, when more than one camera is active nearby, the signals may interfere with one another, thereby compromising data quality.
Understanding MCI
MCI occurs when two or more ToF cameras operate in overlapping fields of view, leading to interference between their light signals. ToF cameras calculate depth by emitting light pulses and measuring the time taken for the light to reflect from objects. When multiple cameras are active in the same environment, the emitted light from one camera can inadvertently be captured by another. This cross-talk leads to distorted or inaccurate depth measurements.
MCI is problematic in industrial automation since multiple ToF cameras are used for tasks such as assembly line monitoring and quality control.
Impact of MCI on ToF camera performance
When MCI occurs, the depth data captured by ToF cameras becomes unreliable. The overlapping signals can result in the following problems:
- Cross-talk: Signals from one camera are misinterpreted by another, leading to incorrect depth calculations.
- Increased noise: The presence of extraneous light signals amplifies noise in the data, reducing the quality of the depth map.
- Data distortion: Depth maps may display inaccuracies, which can severely impact tasks such as navigation, object tracking, or inspection.
How ToF cameras overcome MCI
ToF camera manufacturers have implemented innovative methods to address MCI and ensure accurate depth data in multi-camera environments. Here are three key strategies based on the source blog:
1) Adjusting camera angles
One of the simplest methods for mitigating MCI involves adjusting the angles of the cameras. By ensuring that each camera covers a distinct field of view, the likelihood of interference between their emitted light signals is minimized.
This approach works best in scenarios where cameras can be strategically placed to monitor separate zones. For example, in a warehouse setting, cameras can be positioned to focus on different aisles, eliminating overlap in their fields of view. While this method reduces interference, it may not be suitable for applications requiring overlapping camera coverage.
2) Operating cameras at different frequencies
ToF cameras can be designed to operate at distinct modulation frequencies, reducing the possibility of cross-talk. By assigning unique frequencies to each camera, their signals can be separated, allowing them to function independently even in overlapping fields of view.
For instance, the latest ToF cameras offer near and far modes, each operating at different frequencies. The near mode is optimized for shorter distances (0.2m to 1.2m), while the far mode covers greater distances (1m to 6m). This frequency separation ensures that multiple cameras can coexist without interference, making it ideal for environments requiring extensive coverage.
3) Time multiplexing
In this approach, cameras are synchronized to operate at different time intervals. Each camera emits light and captures data in its assigned time slot, ensuring that only one camera is active at any given moment.
This method completely eliminates the risk of cross-talk by preventing simultaneous operation. While time multiplexing may reduce the overall frame rate, it guarantees accurate depth measurements and reliable performance in multi-camera setups. It is particularly well-suited for applications like industrial automation and surveillance, where consistent accuracy is prioritized.
Choosing the right method
Each method for overcoming MCI has its advantages and limitations, making it important to select the one that best fits the application. For example:
ToF camera manufacturers have implemented innovative methods to address MCI and ensure accurate depth data in multi-camera environments. Here are three key strategies based on the source blog:
1) Adjusting camera angles
One of the simplest methods for mitigating MCI involves adjusting the angles of the cameras. By ensuring that each camera covers a distinct field of view, the likelihood of interference between their emitted light signals is minimized.
This approach works best in scenarios where cameras can be strategically placed to monitor separate zones. For example, in a warehouse setting, cameras can be positioned to focus on different aisles, eliminating overlap in their fields of view. While this method reduces interference, it may not be suitable for applications requiring overlapping camera coverage.
2) Operating cameras at different frequencies
ToF cameras can be designed to operate at distinct modulation frequencies, reducing the possibility of cross-talk. By assigning unique frequencies to each camera, their signals can be separated, allowing them to function independently even in overlapping fields of view.
For instance, the latest ToF cameras offer near and far modes, each operating at different frequencies. The near mode is optimized for shorter distances (0.2m to 1.2m), while the far mode covers greater distances (1m to 6m). This frequency separation ensures that multiple cameras can coexist without interference, making it ideal for environments requiring extensive coverage.
3) Time multiplexing
In this approach, cameras are synchronized to operate at different time intervals. Each camera emits light and captures data in its assigned time slot, ensuring that only one camera is active at any given moment.
This method completely eliminates the risk of cross-talk by preventing simultaneous operation. While time multiplexing may reduce the overall frame rate, it guarantees accurate depth measurements and reliable performance in multi-camera setups. It is particularly well-suited for applications like industrial automation and surveillance, where consistent accuracy is prioritized.
Choosing the right method
Each method for overcoming MCI has its advantages and limitations, making it important to select the one that best fits the application. For example:
- Adjusting camera angles works well for non-overlapping coverage but may be impractical in confined spaces.
- Operating at different frequencies offers flexibility in overlapping fields of view but requires cameras with frequency separation capabilities.
- Time multiplexing is the most comprehensive solution for eliminating interference but may impact real-time performance due to lower frame rates.
How ToF Cameras Work in Popular Industrial Automation Systems
Robotic vision for complex operations
In robotic automation, ToF cameras play a crucial role in providing accurate spatial data for object manipulation. For pick-and-place operations, the cameras enable robots to detect object locations, orientations, and distances with high precision. Unlike 2D imaging systems, ToF cameras generate real-time depth information, allowing robots to adapt to irregular shapes or cluttered environments.
For example, in automotive assembly lines, ToF cameras guide robotic arms to handle components like bolts, wiring, or panels with precision, ensuring alignment and reducing assembly time.
Automated quality assurance
ToF cameras are transforming quality control processes by enabling three-dimensional inspection of manufactured products. Traditional 2D systems may struggle to detect subtle defects like dents or uneven surfaces, especially on complex geometries. ToF technology, however, captures detailed depth data to identify inconsistencies, measure dimensions, and verify product designs.
In semiconductor manufacturing, for instance, ToF cameras inspect micro-components for defects, ensuring compliance with stringent quality standards. This reduces material waste and prevents defective products from advancing through production pipelines.
Dynamic inventory tracking in warehouses
ToF cameras streamline inventory management in automated warehouses by providing real-time 3D mapping of storage areas. They enable robots or automated guided vehicles (AGVs) to navigate and retrieve items accurately by identifying free spaces, item positions, and height profiles. In high-density storage facilities, where space optimization is critical, ToF cameras allow for automated stacking and retrieval of goods without collisions.
For instance, in e-commerce warehouses, this technology facilitates faster order fulfillment by enabling seamless interaction between robotic systems and dynamic storage layouts.
Collision avoidance in autonomous systems
By creating real-time 3D maps of the environment, these cameras help detect obstacles and calculate their exact distance. This depth data allows the system to dynamically adjust its path or movements to avoid collisions, even in fast-paced industrial settings. For example, in material handling, AGVs equipped with ToF cameras can navigate through crowded warehouses, avoiding stationary and moving obstacles while maintaining operational efficiency.
Conveyor belt monitoring and sorting
ToF cameras improve conveyor belt automation by providing accurate 3D data for sorting and monitoring objects. Unlike traditional vision systems, ToF cameras can identify variations in height, shape, and position of items moving at high speeds. This is especially useful in industries like logistics and manufacturing, where automated sorting and quality checks are crucial.
For example, in electronics manufacturing, ToF cameras assist in separating defective components based on dimensional irregularities, ensuring that only correctly assembled parts proceed further.
Features of ToF Cameras for Industrial Automation
Streaming 3D depth and IR imaging
ToF cameras provide real-time 3D depth mapping and infrared (IR) imaging, enabling machines to perceive their environment with a high degree of detail. These cameras emit infrared pulses that reflect off objects and return to the sensor, enabling the calculation of distances with remarkable accuracy. This drives object detection, spatial awareness, and navigation, all of which are critical in industrial automation.
IR imaging also extends its application in environments with variable lighting, ensuring uninterrupted performance even in low-light conditions. For industries like manufacturing and logistics, where around-the-clock operations are important, this improves system reliability.
Hardware trigger for synchronization
ToF cameras equipped with a hardware trigger enable synchronization with other devices in an automated setup. It ensures precise timing for image capture so that the camera operates with other components, such as conveyor belts, robotic arms, or motion controllers.
In sectors relying on automation for inspection and assembly, such synchronization reduces delays and enhances consistency.
Seamless integration with development kits
ToF cameras must integrate easily with advanced development platforms such as NVIDIA® Jetson AGX Orin™, which are widely used in industrial automation. These platforms bring powerful computing capabilities, enabling real-time analysis and decision-making based on the data captured by the cameras.
The compatibility between ToF cameras and such platforms accelerates the deployment of machine vision solutions. Developers can access pre-configured libraries and tools to create applications tailored to specific industrial tasks, ranging from robotic guidance to automated quality checks.
Multi-camera synchronization
In industrial environments, the simultaneous operation of multiple cameras is often necessary to cover expansive areas or monitor complex processes. ToF cameras address this requirement by enabling multiple units to work together without signal interference. Advanced modulation techniques ensure that each camera produces accurate data independently, even in close proximity to others.
It can be valuable in scenarios like warehouse management or automated vehicle navigation, where overlapping fields of view are common.
Depth range of up to 8.5m
ToF cameras' ability to capture depth information over a range of up to 8.5 meters makes them crucial in environments requiring extended spatial awareness. In automated systems, an extended depth range allows for flexibility in system design. So, robots can navigate and interact with objects at varying distances, ensuring that even complex layouts do not hinder performance.
Performance with 940nm pulsed laser in daylight
Industrial applications frequently encounter challenging lighting conditions, including outdoor environments or areas with bright artificial light. ToF cameras equipped with a 940nm pulsed laser are designed to maintain consistent performance under such conditions, minimizing the impact of ambient light on depth sensing.
The Need for RGB Data in Depth Cameras
Time-of-Flight (ToF) cameras are widely used for their ability to measure depth and create 3D maps of environments. While they excel at capturing depth information, these cameras typically lack the ability to capture color data. However, integrating RGB and depth data into a single ToF camera can provide an edge in applications requiring object classification and detailed spatial analysis.
Why depth cameras exclude RGB data by default
Depth cameras measure distances to objects or surfaces, focusing exclusively on spatial information. The following factors explain why RGB data is generally absent in these systems:
Robotic vision for complex operations
In robotic automation, ToF cameras play a crucial role in providing accurate spatial data for object manipulation. For pick-and-place operations, the cameras enable robots to detect object locations, orientations, and distances with high precision. Unlike 2D imaging systems, ToF cameras generate real-time depth information, allowing robots to adapt to irregular shapes or cluttered environments.
For example, in automotive assembly lines, ToF cameras guide robotic arms to handle components like bolts, wiring, or panels with precision, ensuring alignment and reducing assembly time.
Automated quality assurance
ToF cameras are transforming quality control processes by enabling three-dimensional inspection of manufactured products. Traditional 2D systems may struggle to detect subtle defects like dents or uneven surfaces, especially on complex geometries. ToF technology, however, captures detailed depth data to identify inconsistencies, measure dimensions, and verify product designs.
In semiconductor manufacturing, for instance, ToF cameras inspect micro-components for defects, ensuring compliance with stringent quality standards. This reduces material waste and prevents defective products from advancing through production pipelines.
Dynamic inventory tracking in warehouses
ToF cameras streamline inventory management in automated warehouses by providing real-time 3D mapping of storage areas. They enable robots or automated guided vehicles (AGVs) to navigate and retrieve items accurately by identifying free spaces, item positions, and height profiles. In high-density storage facilities, where space optimization is critical, ToF cameras allow for automated stacking and retrieval of goods without collisions.
For instance, in e-commerce warehouses, this technology facilitates faster order fulfillment by enabling seamless interaction between robotic systems and dynamic storage layouts.
Collision avoidance in autonomous systems
By creating real-time 3D maps of the environment, these cameras help detect obstacles and calculate their exact distance. This depth data allows the system to dynamically adjust its path or movements to avoid collisions, even in fast-paced industrial settings. For example, in material handling, AGVs equipped with ToF cameras can navigate through crowded warehouses, avoiding stationary and moving obstacles while maintaining operational efficiency.
Conveyor belt monitoring and sorting
ToF cameras improve conveyor belt automation by providing accurate 3D data for sorting and monitoring objects. Unlike traditional vision systems, ToF cameras can identify variations in height, shape, and position of items moving at high speeds. This is especially useful in industries like logistics and manufacturing, where automated sorting and quality checks are crucial.
For example, in electronics manufacturing, ToF cameras assist in separating defective components based on dimensional irregularities, ensuring that only correctly assembled parts proceed further.
Features of ToF Cameras for Industrial Automation
Streaming 3D depth and IR imaging
ToF cameras provide real-time 3D depth mapping and infrared (IR) imaging, enabling machines to perceive their environment with a high degree of detail. These cameras emit infrared pulses that reflect off objects and return to the sensor, enabling the calculation of distances with remarkable accuracy. This drives object detection, spatial awareness, and navigation, all of which are critical in industrial automation.
IR imaging also extends its application in environments with variable lighting, ensuring uninterrupted performance even in low-light conditions. For industries like manufacturing and logistics, where around-the-clock operations are important, this improves system reliability.
Hardware trigger for synchronization
ToF cameras equipped with a hardware trigger enable synchronization with other devices in an automated setup. It ensures precise timing for image capture so that the camera operates with other components, such as conveyor belts, robotic arms, or motion controllers.
In sectors relying on automation for inspection and assembly, such synchronization reduces delays and enhances consistency.
Seamless integration with development kits
ToF cameras must integrate easily with advanced development platforms such as NVIDIA® Jetson AGX Orin™, which are widely used in industrial automation. These platforms bring powerful computing capabilities, enabling real-time analysis and decision-making based on the data captured by the cameras.
The compatibility between ToF cameras and such platforms accelerates the deployment of machine vision solutions. Developers can access pre-configured libraries and tools to create applications tailored to specific industrial tasks, ranging from robotic guidance to automated quality checks.
Multi-camera synchronization
In industrial environments, the simultaneous operation of multiple cameras is often necessary to cover expansive areas or monitor complex processes. ToF cameras address this requirement by enabling multiple units to work together without signal interference. Advanced modulation techniques ensure that each camera produces accurate data independently, even in close proximity to others.
It can be valuable in scenarios like warehouse management or automated vehicle navigation, where overlapping fields of view are common.
Depth range of up to 8.5m
ToF cameras' ability to capture depth information over a range of up to 8.5 meters makes them crucial in environments requiring extended spatial awareness. In automated systems, an extended depth range allows for flexibility in system design. So, robots can navigate and interact with objects at varying distances, ensuring that even complex layouts do not hinder performance.
Performance with 940nm pulsed laser in daylight
Industrial applications frequently encounter challenging lighting conditions, including outdoor environments or areas with bright artificial light. ToF cameras equipped with a 940nm pulsed laser are designed to maintain consistent performance under such conditions, minimizing the impact of ambient light on depth sensing.
The Need for RGB Data in Depth Cameras
Time-of-Flight (ToF) cameras are widely used for their ability to measure depth and create 3D maps of environments. While they excel at capturing depth information, these cameras typically lack the ability to capture color data. However, integrating RGB and depth data into a single ToF camera can provide an edge in applications requiring object classification and detailed spatial analysis.
Why depth cameras exclude RGB data by default
Depth cameras measure distances to objects or surfaces, focusing exclusively on spatial information. The following factors explain why RGB data is generally absent in these systems:
- Purpose of depth cameras: Technologies such as stereo cameras and ToF sensors prioritize depth calculations. Stereo cameras use the disparity between two images to estimate depth, while ToF sensors rely on light detection or pulsed lasers to build depth maps or point clouds. These methods do not require color information to achieve their objectives.
- Increased processing requirements: Adding RGB capture to a depth camera increases the computational demands on the system. Processing both color and depth simultaneously requires additional hardware and software resources, which can impact system performance.
For these reasons, traditional depth cameras are not equipped with the ability to deliver RGB data.
The value of RGB data in industrial automation
In many industrial and autonomous applications, color information is essential for recognizing and differentiating between objects. A few examples highlight the need for RGB data:
The value of RGB data in industrial automation
In many industrial and autonomous applications, color information is essential for recognizing and differentiating between objects. A few examples highlight the need for RGB data:
- Object recognition: Identifying the type of an object requires color data. For instance, distinguishing between a human, an animal, or a machine part is not possible with depth data alone.
- Action-based object classification: Consider an autonomous tractor. The tractor needs to recognize whether an approaching object is a human, an animal, or a piece of equipment. Based on this classification, the tractor may need to adjust its stopping distance for safety.
Depth data alone cannot achieve this level of recognition; RGB data is required to provide visual clues about the object's nature. This combination becomes crucial in scenarios demanding both spatial awareness and visual classification.
Why deliver depth and RGB data in a single frame?
Integrating depth and RGB data into a single frame provides clear advantages over capturing them separately. The most prominent benefits include:
Avoiding pixel-to-pixel mapping challenges
When depth and color data are captured in separate frames, the two data sets must be aligned through pixel-to-pixel mapping. This process is computationally intensive and prone to errors, especially when objects or cameras are in motion. A single frame containing both depth and RGB data eliminates this step entirely, improving processing speed and accuracy.
Streamlined processing
With both data types in the same frame, downstream applications can immediately use the combined information without requiring additional synchronization or calibration steps. This reduces the complexity of real-time decision-making systems.
Improved accuracy
In applications involving movement—whether it's the camera, the object, or both—capturing RGB and depth data in separate frames can lead to misalignment due to temporal shifts. Delivering both data types in one frame eliminates these alignment issues, ensuring consistent results.
Advantages of Time-of-Flight (ToF) Cameras in Industrial Automation
Enhanced object detection
ToF cameras excel in detecting objects with remarkable accuracy by emitting light signals and measuring the time taken for them to reflect from surfaces. Unlike traditional vision systems, which struggle with reflective, translucent, or low-contrast materials, ToF technology captures depth information in real time. So, they can help perform industrial automation tasks like detecting irregularly shaped objects on conveyor belts or monitoring assembly lines.
ToF cameras can also distinguish overlapping or closely spaced objects, enabling seamless handling of complex sorting processes by providing three-dimensional data. It makes them very useful for applications where conventional cameras might fail, such as detecting objects in cluttered environments or those with varying textures and colors.
Better quality control
Maintaining high standards in manufacturing requires an advanced a high degree of inspection. ToF cameras offer depth data that enables detailed analysis of objects, components, or finished products. They capture volumetric information so that manufacturers can detect defects that might be invisible to traditional vision systems, including surface irregularities, improper assembly, and deviations in dimensions.
For instance, in electronics manufacturing, ToF cameras can inspect soldering joints or identify faulty components with exceptional accuracy. It reduces the probability of defective products entering the supply chain, minimizing rework and waste.
Accurate robotic guidance
ToF cameras play a critical role in guiding robotic systems within industrial environments. Their depth-sensing capabilities equip robots to perceive spatial information, thereby ensuring accurate positioning and interaction with objects. That's how ToF cameras contribute to increased accuracy, reducing the likelihood of errors in automated processes.
For instance, this depth data is important for complex tasks like picking and placing objects, welding, or assembling parts, where perfect alignment and positioning are required.
Accurate depth measurements
ToF cameras are uniquely equipped to provide accurate depth measurements by calculating the distance between the camera and objects in its field of view. This empowers applications that rely on accurate spatial data, such as volume estimation, bin picking, or pallet stacking.
In logistics, for example, ToF cameras can measure the dimensions of packages on conveyor belts to optimize storage or shipping. Similarly, in manufacturing, they help determine the exact placement of components within assemblies so that parts fit correctly without manual intervention.
Fast response times
In industrial automation, speed is as critical as accuracy. ToF cameras operate with minimal latency, capturing depth data in real time. Such rapid response makes them ideal for applications that demand high-speed processing, like dynamic object tracking or motion detection. For instance, in high-speed production lines, ToF cameras can monitor objects moving at high speeds, providing actionable data without delay.
Consistent performance
Industrial environments pose challenges for sensing technologies, including variable lighting, dust, vibrations, or extreme temperatures. ToF cameras can perform reliably under such conditions since they rely on light signals emitted by the camera itself. It means they remain unaffected by ambient light variations, ensuring consistent performance in well-lit and poorly lit areas.
Also, their rugged design and ability to function in dusty or high-vibration environments make them suitable for heavy industries like mining, construction, and automotive manufacturing.
Futuristic Impact of ToF Cameras on Industrial Automation
One promising avenue is the integration of ToF cameras with advanced robotics, enabling machines to handle soft, deformable, or irregularly shaped materials with greater dexterity. For example, the textile and food industries, which rely on critical handling tasks, can use ToF cameras to provide robots with depth-perception capabilities that adapt in real time to varying conditions. This development could replace labor-intensive manual operations with scalable, automated solutions that maintain consistency and quality.
Another groundbreaking potential of ToF cameras is in dynamic factory floor reconfiguration. Future automation systems equipped with ToF sensors could map and adjust to changing layouts without halting operations, a feature critical for agile manufacturing practices.
Such systems could identify the optimal pathways for robotic fleets or pinpoint underutilized spaces in real time, enhancing spatial productivity. Additionally, when paired with AI-driven analytics, ToF cameras could evolve into decision-making tools, offering predictive insights based on real-time spatial data trends.
e-con Systems’ Time-of-Flight camera for industrial automation applications
e-con Systems has been working with depth-sensing technologies for over ten years. We have designed and developed DepthVista – a cutting-edge Time-of-Flight camera that delivers depth information and RGB data in one frame. This is tremendously useful for simultaneous depth measurement and object recognition. This is made possible by a combination of a CCD sensor (for depth measurement) and the ARO234 color global shutter sensor from Onsemi (for object recognition). The depth sensor streams a resolution of 640 x 480 @ 30fps, while the color global shutter sensor streams HD and FHD @30fps.
www.e-consystems.com
Why deliver depth and RGB data in a single frame?
Integrating depth and RGB data into a single frame provides clear advantages over capturing them separately. The most prominent benefits include:
Avoiding pixel-to-pixel mapping challenges
When depth and color data are captured in separate frames, the two data sets must be aligned through pixel-to-pixel mapping. This process is computationally intensive and prone to errors, especially when objects or cameras are in motion. A single frame containing both depth and RGB data eliminates this step entirely, improving processing speed and accuracy.
Streamlined processing
With both data types in the same frame, downstream applications can immediately use the combined information without requiring additional synchronization or calibration steps. This reduces the complexity of real-time decision-making systems.
Improved accuracy
In applications involving movement—whether it's the camera, the object, or both—capturing RGB and depth data in separate frames can lead to misalignment due to temporal shifts. Delivering both data types in one frame eliminates these alignment issues, ensuring consistent results.
Advantages of Time-of-Flight (ToF) Cameras in Industrial Automation
Enhanced object detection
ToF cameras excel in detecting objects with remarkable accuracy by emitting light signals and measuring the time taken for them to reflect from surfaces. Unlike traditional vision systems, which struggle with reflective, translucent, or low-contrast materials, ToF technology captures depth information in real time. So, they can help perform industrial automation tasks like detecting irregularly shaped objects on conveyor belts or monitoring assembly lines.
ToF cameras can also distinguish overlapping or closely spaced objects, enabling seamless handling of complex sorting processes by providing three-dimensional data. It makes them very useful for applications where conventional cameras might fail, such as detecting objects in cluttered environments or those with varying textures and colors.
Better quality control
Maintaining high standards in manufacturing requires an advanced a high degree of inspection. ToF cameras offer depth data that enables detailed analysis of objects, components, or finished products. They capture volumetric information so that manufacturers can detect defects that might be invisible to traditional vision systems, including surface irregularities, improper assembly, and deviations in dimensions.
For instance, in electronics manufacturing, ToF cameras can inspect soldering joints or identify faulty components with exceptional accuracy. It reduces the probability of defective products entering the supply chain, minimizing rework and waste.
Accurate robotic guidance
ToF cameras play a critical role in guiding robotic systems within industrial environments. Their depth-sensing capabilities equip robots to perceive spatial information, thereby ensuring accurate positioning and interaction with objects. That's how ToF cameras contribute to increased accuracy, reducing the likelihood of errors in automated processes.
For instance, this depth data is important for complex tasks like picking and placing objects, welding, or assembling parts, where perfect alignment and positioning are required.
Accurate depth measurements
ToF cameras are uniquely equipped to provide accurate depth measurements by calculating the distance between the camera and objects in its field of view. This empowers applications that rely on accurate spatial data, such as volume estimation, bin picking, or pallet stacking.
In logistics, for example, ToF cameras can measure the dimensions of packages on conveyor belts to optimize storage or shipping. Similarly, in manufacturing, they help determine the exact placement of components within assemblies so that parts fit correctly without manual intervention.
Fast response times
In industrial automation, speed is as critical as accuracy. ToF cameras operate with minimal latency, capturing depth data in real time. Such rapid response makes them ideal for applications that demand high-speed processing, like dynamic object tracking or motion detection. For instance, in high-speed production lines, ToF cameras can monitor objects moving at high speeds, providing actionable data without delay.
Consistent performance
Industrial environments pose challenges for sensing technologies, including variable lighting, dust, vibrations, or extreme temperatures. ToF cameras can perform reliably under such conditions since they rely on light signals emitted by the camera itself. It means they remain unaffected by ambient light variations, ensuring consistent performance in well-lit and poorly lit areas.
Also, their rugged design and ability to function in dusty or high-vibration environments make them suitable for heavy industries like mining, construction, and automotive manufacturing.
Futuristic Impact of ToF Cameras on Industrial Automation
One promising avenue is the integration of ToF cameras with advanced robotics, enabling machines to handle soft, deformable, or irregularly shaped materials with greater dexterity. For example, the textile and food industries, which rely on critical handling tasks, can use ToF cameras to provide robots with depth-perception capabilities that adapt in real time to varying conditions. This development could replace labor-intensive manual operations with scalable, automated solutions that maintain consistency and quality.
Another groundbreaking potential of ToF cameras is in dynamic factory floor reconfiguration. Future automation systems equipped with ToF sensors could map and adjust to changing layouts without halting operations, a feature critical for agile manufacturing practices.
Such systems could identify the optimal pathways for robotic fleets or pinpoint underutilized spaces in real time, enhancing spatial productivity. Additionally, when paired with AI-driven analytics, ToF cameras could evolve into decision-making tools, offering predictive insights based on real-time spatial data trends.
e-con Systems’ Time-of-Flight camera for industrial automation applications
e-con Systems has been working with depth-sensing technologies for over ten years. We have designed and developed DepthVista – a cutting-edge Time-of-Flight camera that delivers depth information and RGB data in one frame. This is tremendously useful for simultaneous depth measurement and object recognition. This is made possible by a combination of a CCD sensor (for depth measurement) and the ARO234 color global shutter sensor from Onsemi (for object recognition). The depth sensor streams a resolution of 640 x 480 @ 30fps, while the color global shutter sensor streams HD and FHD @30fps.
www.e-consystems.com