HOW MODULAR CLAMPING SYSTEMS ARE REVOLUTIONIZING PRECISION IN METROLOGY
In this article, Almir Jakupovic, Sales Director at norelem, discusses how modular clamping systems are revolutionizing precision in metrology, providing engineers with an adaptable, efficient and sustainable solution to meet the demands of high-precision industries.
norelem.co.uk
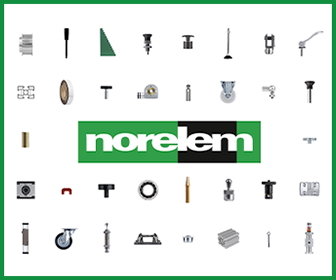
Precision metrology is essential in modern production, ensuring product quality, safety and operating efficiency. In high-precision sectors such as automotive, aerospace and electronics, engineers are constantly trying to balance accuracy, efficiency and cost. However, traditional metrology tools - such as gauges, calipers, micrometers and bevel protractors - struggle to meet these evolving demands.
As quality expectations continue to rise, the need for precision metrology grows, placing engineers at the heart of quality control. Their role is essential to ensure that every part and product meets strict specifications, as even minor errors can affect performance and safety. However, traditional fixturing setups used with coordinate measuring machines (CMM) and optical devices often fall short of modern demands, meaning engineers face time-consuming setups, high custom fixturing costs and limited flexibility for new projects.
This is where modular clamping systems offer a solution. These innovative setups provide engineers with customizable, high-precision measuring options that maintain quality without compromising results.
By addressing these common issues, modular clamping systems provide engineers with a versatile, efficient and cost-effective solution. These systems, designed with standardized and interchangeable components, allow engineers to quickly assemble, reconfigure and adapt setups for fixturing. This streamlines metrology processes and offers exceptional support.
Let's take a closer look at how these systems benefit engineers:
1. Flexible, fast setup
Modular clamping systems empower engineers with rapid, tool-free adjustments. With quick-change interfaces, these systems allow parts and components to be swapped out seamlessly, minimizing setup times and enhancing adaptability to different tasks. For engineers, this means less downtime and more focus on high-value activities. In industries that require rapid response to changing project demands, modular systems enable engineers to handle a high volume of parts and configurations without slowing down.
One of the key advantages is their compatibility with a wide range of measurement technologies, including CMMs, optical systems and multi-sensor devices, which means engineers can use a single modular system across multiple measurement platforms. This multi-use adaptability reduces setup complexity and saves engineers the hassle of switching between fixtures, providing a streamlined workflow that keeps production moving.
2. Precision and stability
Alongside speed, engineers prioritize accuracy, which is why modular clamping systems are designed to provide precise and repeatable measurements. Modular systems, made from high-quality, wear-resistant materials, ensure fixture stability and consistent measurements over repeated uses, which is crucial for engineers requiring reliable results each time. These components are designed to be reassembled with reproducible accuracy, allowing engineers to conduct consistent measurements without recalibration - a significant time-saver in high-volume production environments.
With every setup guaranteed to be identical, engineers can rely on modular clamping systems to meet stringent standards, reduce errors and contribute to high-quality production outcomes. This stability offers peace of mind for engineers working on safety-critical components, knowing that each measurement is as precise as the last.
3. Cost-effective and sustainable solutions
For engineers managing budgets, modular clamping systems are a game-changer. Modular systems reduce the need for costly custom fixturing by enabling reusable, adaptable setups. Engineers can reconfigure components for new projects, minimizing waste and promoting sustainability without compromising on quality. For those overseeing long-term projects, this approach not only saves material costs but also extends the lifespan of each setup, saving valuable time and reducing the potential for errors.
Engineers also benefit from a more sustainable solution that aligns with corporate environmental goals. The modular design means fewer resources are spent on disposable fixtures, allowing companies to support environmental standards without sacrificing productivity or quality.
4. Accessible measurement points for enhanced usability
Engineers often need help reaching all necessary measurement points on complex parts. Rather than messing around with moving the part, modular clamping systems are designed to provide full access to every critical point. This ensures that engineers can take measurements in a single setup without repositioning. This accessibility allows engineers to complete inspections quicker and with fewer adjustments, reducing the potential for errors and saving valuable time.
Thanks to compatibility with both tactile and optical measurement systems, modular clamping solutions offer a flexible approach that engineers can adapt to various metrology tasks. By eliminating the need to reposition parts during inspection, engineers achieve a more straightforward, efficient measurement process that delivers consistent, reliable data.
The impact on engineering
norelem's modular clamping systems are revolutionizing quality control in metrology by offering exceptional flexibility and accuracy for engineering workflows. These systems significantly reduce setup time and fixture costs while delivering precise and repeatable results that empower engineers to manage complex projects with increased efficiency and confidence.
Engineers using norelem's solutions can spend less time on adjustments and more on optimizing processes. The modular design of these clamping systems equips engineers to handle high-stakes challenges with precision, ensuring that setups can accurately support intricate measurements, even for complex parts. Moreover, norelem's systems align with modern sustainability standards, allowing engineers to meet environmental goals without compromising performance.
This adaptability and reliability have led to widespread adoption across the automotive, aerospace and electronics industries.
The result? norelem is paving the way for a new era in engineering, setting a high bar for precision, performance and sustainable practices that enable professionals to excel. To learn more about norelem's modular clamping systems, visit www.norelemusa.com/en-us/.