Revolutionizing Manufacturing with Magnetic Levitation
Stephen Hayes, managing director at Beckhoff Automation UK, explores how magnetic levitation enhances manufacturing precision, flexibility, hygiene, and modular adaptability to meet diverse industry needs.
www.beckhoff.com
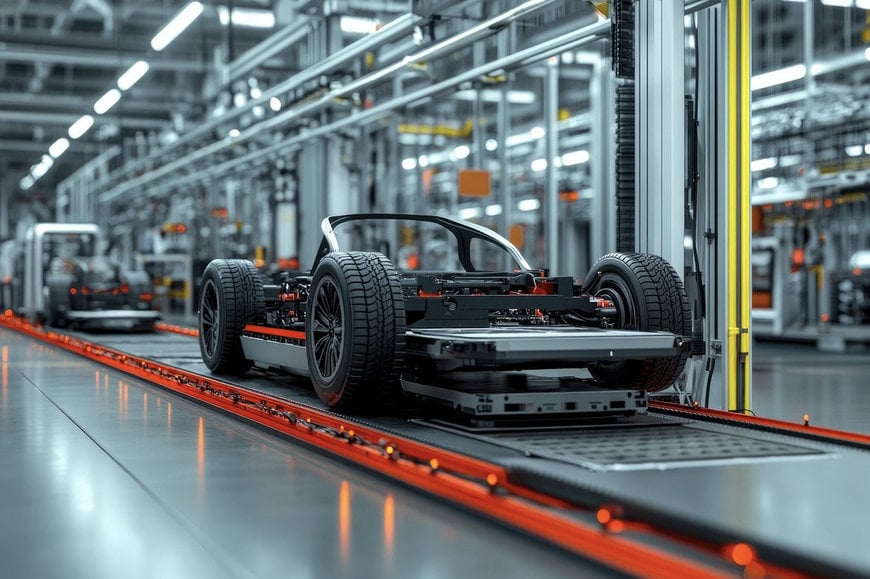
In recent years, manufacturers have been investing in magnetic levitation technology, enabling precision, flexibility, and efficiency in previously unimaginable ways. The technology uses different principles to a hoverboard, but tiles that float or levitate along production lines often reminds me of the famous hoverboard from Back to the Future.
This technology relies on magnetic forces to elevate and guide objects without direct contact, making it highly beneficial in fields requiring precise handling, hygiene, and customisation. An good example of magnetic levitation in manufacturing is Beckhoff's XPlanar system, which uses levitating, magnetically driven movers to achieve new levels of versatility in production environments.
How it works
Magnetic levitation relies on the interaction of magnetic forces to suspend objects in space. By controlling magnetic poles, an object can be held above a surface, floating freely without any direct contact. Electromagnets, which are magnets powered by electric currents, are commonly used in these systems, allowing for precise control of magnetic forces to balance the object against gravity.
The XPlanar system exemplifies this principle through the use of a planar grid with embedded magnetic coils that generate a magnetic field. These fields interact with magnets in the levitating movers, keeping them elevated while allowing multidirectional movement. XPlanar’s six degrees of freedom enable movements in all directions, rotation, and even tilting, giving it the flexibility to handle diverse manufacturing needs, from assembling electronics to packaging sensitive items.
Manufacturing benefits
Magnetic levitation systems offer exceptional precision in controlling movement. The best systems allow individual movers to follow unique paths, making it possible to adjust production processes dynamically without affecting other operations. This flexibility supports applications with varied batch sizes, from single units to large volumes, without the need for reconfiguration.
Since magnetic levitation eliminates direct contact with surfaces, friction and associated wear are minimised. This means components don’t degrade as quickly, reducing the need for regular maintenance and replacements. The contactless nature of magnetic levitation systems is also a significant advantage in industries with strict hygiene standards, such as pharmaceuticals and food production.
The technology also has benefits in terms of efficient use of space and resources, as it supports compact, modular designs. Manufacturers can arrange tiles in customised layouts, optimising space while allowing for future scalability by adding more tiles or movers as needed. This modularity makes it easier for manufacturers to adapt production lines to new requirements without major redesigns.
This technology can offer unique benefits for different sectors. Automotive production involves both heavy and delicate components, often requiring precise, programmable movement through complex assembly lines. The load-bearing capability and dynamic control in systems like XPlanar make them well-suited for such varied demands, allowing automotive manufacturers to streamline production while reducing machine wear and maintenance costs.
Unlike Marty McFly’s hoverboard, magnetic levitation technology has proven to be more than just a futuristic concept, with tangible benefits across diverse manufacturing industries. Through the example of Beckhoff's XPlanar, which is now a tried and tested system, it’s clear that the technology provides unmatched flexibility, precision, and hygiene standards, making it invaluable in automotive production. As magnetic levitation continues to evolve, its impact on manufacturing is expected to grow, driving new standards of efficiency and adaptability in industrial automation.
www.beckhoff.com