Industrial bearings support the GenAI revolution
By Chris Johnson of SMB Bearings emphasises how industrial bearings equipped with sensors can support GenAI by providing real-time data and insights.
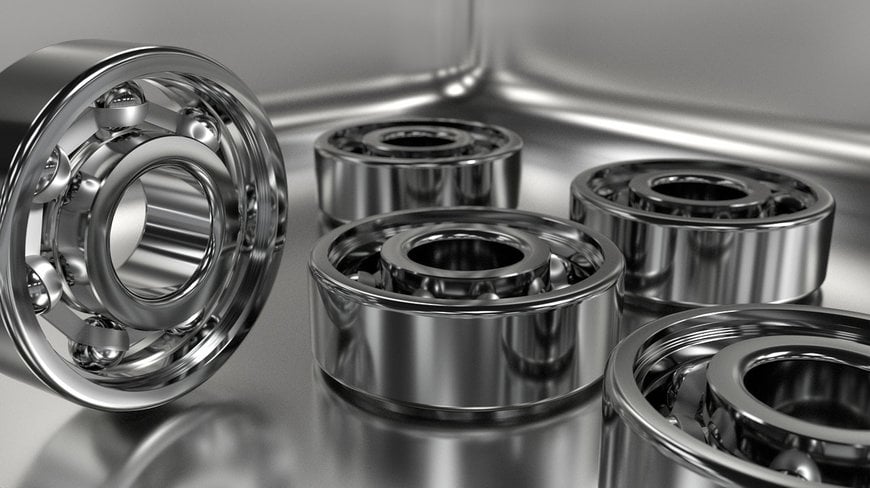
According to PwC, 70 per cent of CEOs worldwide believe Generative AI (GenAI) will significantly transform the way their companies create, deliver and capture value. That includes manufacturers, who can use the systems to spot equipment failures and minimise downtime.
GenAI is a remarkable form of Artificial Intelligence with the unprecedented ability to produce an array of data types, including images, videos, audio, text and 3D models. Put simply, GenAI can delve into existing data, deciphering patterns, and leveraging this knowledge to generate entirely new outputs.
Its capabilities extend far beyond mere replication, as it crafts highly realistic and intricate content that mirrors human creativity, thus positioning itself as an invaluable tool across various industries, such as gaming, entertainment and product design.
GenAI, which generates new, original content like text or images using patterns learned from data, also has immense potential in manufacturing which will also help drive the growth predicted in PwC’s report. For manufacturers, the technology can predict equipment failures and minimise downtime, significantly enhancing operational efficiency.
As such, GenAI could be a vital tool in Maintenance 4.0. These sensors can monitor parameters such as temperature and vibration, detecting potential issues before they escalate. This proactive monitoring not only enhances equipment performance and reduces downtime but also optimises production processes. Moreover, the data collected can train GenAI algorithms, enabling continuous improvement over time.
Efficient operation of plant machinery
Smart bearings, integrated with sensors, have been utilised in automotive anti-lock braking systems (ABS) for years and are now being increasingly adopted in various industries. The rise of the Industrial Internet of Things (IIoT) allows manufacturers to remotely monitor processes and convert physical machine actions into digital signals.
In this Industry 4.0 landscape, the performance of bearings remains vital to the efficient operation of plant machinery. Replacing a single bearing is far more cost-effective than replacing an entire motor, making the choice of smart bearings an economically sound decision.
The benefits of smart bearings, particularly for predictive maintenance, are substantial. IIoT-enabled smart bearings can self-diagnose potential faults and failures through sensor data embedded within the bearing housing. Examples include wheel hub bearings with built-in sensors for ABS brakes, or bearings with sensors that collect data on temperature, vibration, and speed from multiple bearings, transmitting this information to an industrial control system.
Analysing critical bearing data
Real-time monitoring of speed, pressure, force, temperature, and vibration can yield critical data, enhancing the overall predictive maintenance strategy.
However, it's essential to analyse smart bearing data alongside other critical asset data for a comprehensive operational overview. Proper use of smart bearings can extend their service life, reduce energy consumption, and predict early equipment failures.
Component manufacturers are increasingly incorporating smart bearings, and bearing manufacturers are partnering with IIoT innovators to offer extended cloud-based predictive maintenance services for various industrial machines. This integration can also lower training costs, as less-experienced operators can achieve desired performance levels more rapidly.
While it’s impossible to predict every detail, the advantages of smart bearings with predictive maintenance capabilities are clear. Their use is expected to grow significantly in sectors like aerospace, defense, wind turbines, railways and automotive.
Smart bearings and GenAI
Let's consider an automotive manufacturing plant. Within the plant, there's a robotic assembly line responsible for fitting components into vehicles. Each robot arm is equipped with various bearings to ensure smooth movement and precise positioning of components.
Now, these bearings are not ordinary; they are smart bearings embedded with sensors capable of monitoring parameters such as temperature, vibration, and load distribution in real-time. This data is continuously fed into a centralised AI system powered by GenAI algorithms. As the assembly line operates, the GenAI system analyses the data streaming from the smart bearings. It detects subtle changes in vibration patterns or temperature fluctuations that might indicate early signs of bearing wear or potential faults.
Here's where GenAI shines: based on historical data and patterns learned from thousands of similar scenarios, it predicts the likelihood of a bearing failure within a specific timeframe. For instance, if the vibration patterns deviate beyond a certain threshold or if the temperature exceeds optimal levels, the GenAI system can forecast that a bearing is likely to fail within the next few days.
With this predictive insight, the manufacturing plant can take proactive measures to prevent unplanned downtime. The GenAI system automatically generates maintenance alerts, scheduling a preventive maintenance task to replace the affected bearing before it fails. Maintenance technicians receive these alerts well in advance, allowing them to plan the maintenance activity during scheduled downtime, minimising disruption to production schedules.
Furthermore, the data collected from these smart bearings doesn't just stop at predicting failures. It also feeds into the GenAI system's continuous learning loop. By analysing patterns of bearing performance and failure across various operating conditions, the AI algorithms become more adept at fine-tuning their predictive capabilities over time. This iterative learning process enhances the accuracy of future predictions, ultimately optimising maintenance schedules and maximising equipment uptime.
In this way, bearings with smart sensors support GenAI by providing real-time data insights that enable predictive maintenance strategies. By harnessing the power of AI-driven predictive analytics, manufacturers can proactively address equipment issues, optimise maintenance schedules, and ultimately drive efficiency and productivity in their operations.
By leveraging affordable sensors, manufacturers can ensure that critical machine components play a vital role in preventing equipment failure. In this new era, industrial bearings are more essential than ever, driving the GenAI revolution forward.
www.smbbearings.com