CMB.TECH Uses Metal 3D Printing to Advance Sustainable Dual-Fuel Hydrogen Technology
Additive manufacturing (AM) is a sustainable production method that enables innovations like CMB.TECH's dual-fuel technology, resulting in 80% reduction in harmful emissions.
cmb.tech
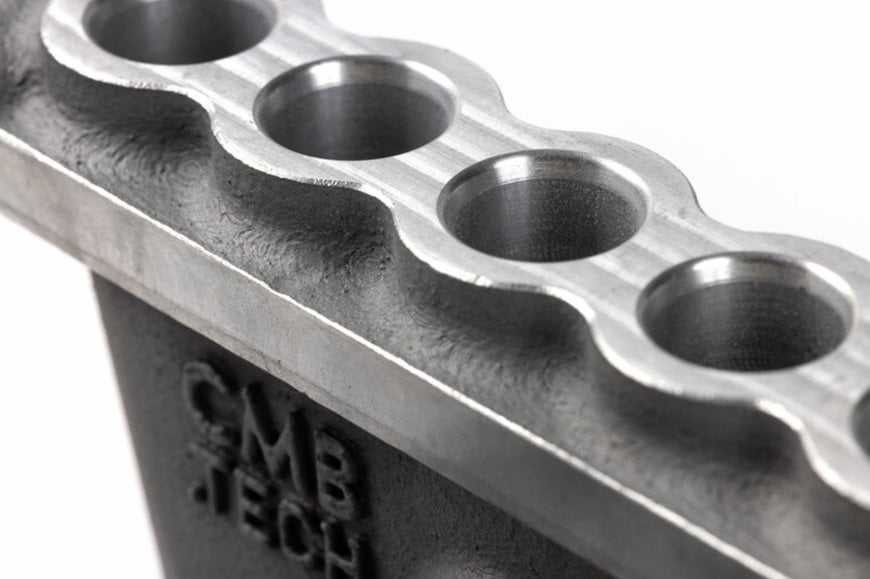
CMB.TECH, the cleantech division of CMB, has spent more than ten years working on a hydrogen-diesel dual-fuel combustion technology. It’s mission? To help decarbonize heavy duty automotive, marine, and other industrial applications as part of the global transition towards a zero-emission society. Thanks to the design freedom and production benefits of metal 3D printing, this mission is moving forward at pace.
Sustainable innovation for the real world
CMB.TECH’s innovative technology enables existing diesel combustion engines to be converted into dual-fuel combustion engines, by aspirating hydrogen into the combustion chamber. This requires less diesel injection, saves emissions, and generates the same engine power.
“The best way to mix the hydrogen and air is with an internal ring structure to disperse hydrogen through little holes. We realized the only feasible way to develop that quickly and easily was through additive manufacturing,” explains Roy Campe, CMB.TECH’s CTO.
3D printed in aluminum using selective laser melting (SLM) to match the materials preferred by most engine manufacturers, an injection ring developed with the help of additive manufacturing specialist Materialise, fits right into its environment.
It also answers two important real-world requirements. In line with global component lightweighting trends relating to minimized fuel/power consumption, the metal 3D printed ring weighs just 654g. What’s more, because printing (rather than casting) the part removes costs linked to die development and material wastage, it is approximately 25% cheaper to make.
“AM changed our whole perception of what was possible and improved the overall concept” added Roy. “We couldn’t easily incorporate those design features into anything made through casting or any other traditional manufacturing process.”
Scaling up with metal 3D printing
To make significant progress on their goals, the team at CMB.TECH needed to produce more than just a one-off prototype. After creating a proof of concept, followed by several test pieces, it was time to move into volume production.
Working through a dedicated ‘New Product Implementation’ (NPI) process designed to help organizations it works with transition from prototyping to serial production, Materialise began manufacturing the injection ring for CMB.TECH at its dedicated facility in Belgium.
“Everything from machining to the assembly process is much simpler when you can remove the complexity in the build phase by using AM. Materialise takes care of all of it, so we receive a fully finished part,” explained Roy.
Making a measurable difference
The injection ring has already been used to successfully convert a fleet of diesel heavy goods trucks, and the system has been shown to reduce CO2 emissions by up to 80% in comparison to traditional diesel engines, depending on the application and the circumstances.
Roy added: “So far, the hydrogen injection ring is the best method to provide hydrogen into the air stream in a pre-mixed way. It allows us to offer C02 savings immediately. The demand and the interest from customers to be able to do that is absolutely massive.”
A revolution is on the horizon
The dual-fuel revolution is around the corner, and CMB.TECH is at the forefront of that movement. As orders roll in, CMB.TECH can comfortably produce the parts they need, knowing they can rely on AM and its intrinsic benefits. Short lead times will allow them to order on-demand, lessening risk and storage costs.
CMB.TECH’s will continue to optimize the technology’s design, expanding the project to different applications - reducing materials and costs where possible.
“For us, it’s essential that we can rapidly come up with design options and alternatives, have them evaluated by the Materialise team, and get guidance on AM to really speed up the process,” says Roy. “Going forward, the designs will just get better and more optimized, ultimately resulting in cheaper parts with less material. For us, it's a really key part of the future strategy.”
www.cmb.tech.com