www.magazine-industry-usa.com
30
'24
Written on Modified on
New state-of-the-art paint shop for Liebherr-Werk Bischofshofen
Liebherr’s wheel loader plant in Bischofshofen, Austria, has recently broken ground on an exciting project, a new paint shop, which will be equipped with state-of-the-art technology and utilise sustainable energy sources.
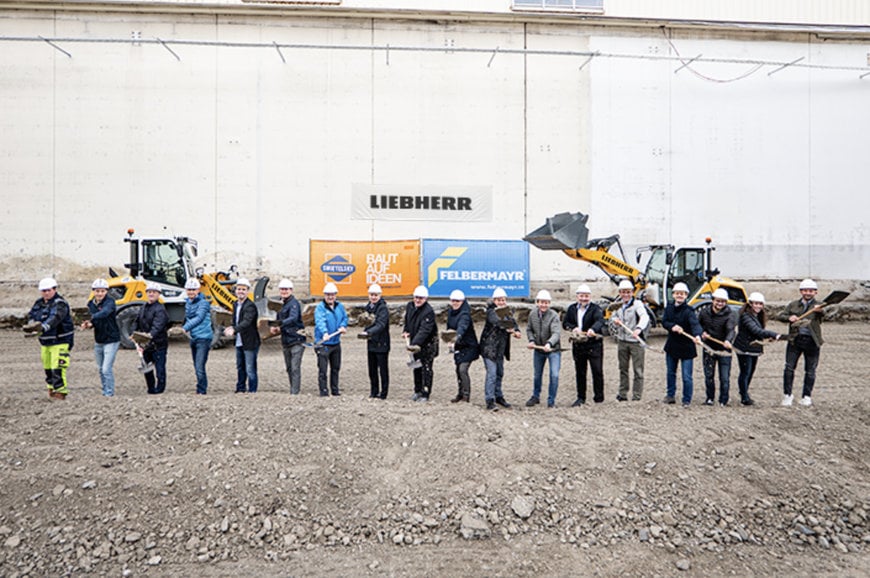
It will expand the capacities of the existing plant and meet the latest technological standards. The new production hall will cover an area of around 6,000 m² and will be spread over three levels, enabling optimum utilisation of the available plant space. With the new paint shop, Liebherr is endeavouring to make production more efficient, reduce energy consumption and create attractive jobs. Completion is planned for the second half of 2025.
With an investment of €18.5 million, Liebherr is laying the foundations for a forward-thinking paint shop at its manufacturing facility in Bischofshofen. The new building will include an office area and will be characterised by its sustainable energy use thanks to heat pump technology, infrared radiation and district heating. “The increasing demand on the wheel loader market has pushed our existing paint shop to its limits.
The new production hall will enable us to meet these challenges and at the same time fulfil the latest technological standards. With the new paint shop, we are also creating attractive jobs in the field of painting and surface technology on site,” explains Peter Schachinger, Managing Director of Production and Operations at the Liebherr plant in Bischofshofen.
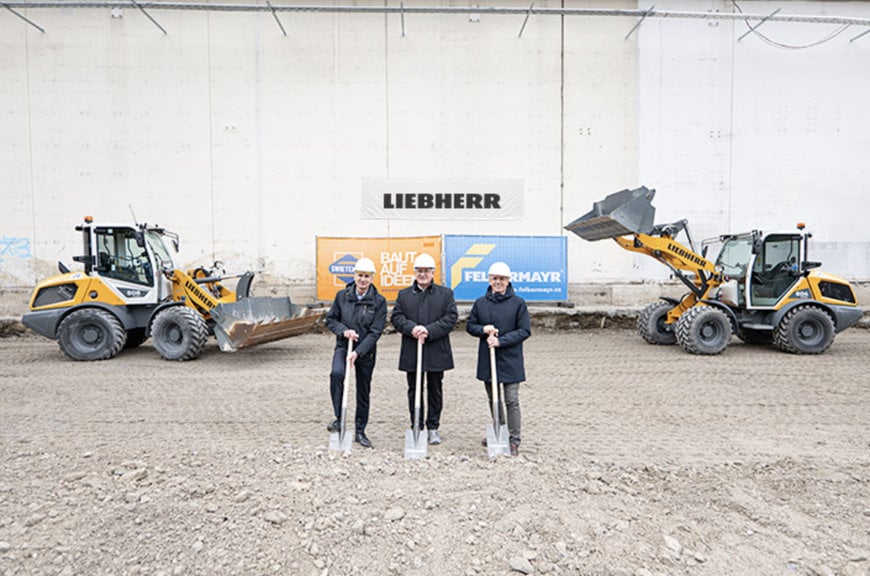
From left: Peter Schachinger (Managing Director of Production and Operations at the Liebherr plant in Bischofshofen), Manfred Bründl (Managing Director of beta-systeme GmbH) and Horst Felbermayr (Managing Director of Felbermayr Holding) at the start of construction of the new paint shop.
Versatile working thanks to innovative technologies
The production hall, measuring approximately 6,000 m², will be divided into three levels, saving floor space and enabling more efficient utilisation of the other areas. On the ground floor (first level), steel components will be cleaned and pre-treated and coating materials will be stored. Coating booths and masking stations are to be located on the second level, which will be around eight metres high.
“Unlike before, the painting boxes will be able to be moved or disposed of in a more versatile way. This will enable us to organise our processes even more efficiently in future,” says Schachinger. The innovations include an electrostatic painting robot system, which will supplement the two manually operated painting boxes. Finally, fully automatic drying of the components will take place on the upper level.
Efficient and sustainable use of energy
As for energy supply, Liebherr favours sustainability. The new paint shop will utilise heat pumps, infrared radiation and district heating based on regional biomass in order to move away from using natural gas. This will enable efficient heat recovery and reduce energy consumption. Thanks to the special energy technology, it will not only be possible to heat, but also to cool. This will allow the workstations to be air-conditioned in summer.
The new paint shop is scheduled for completion in the second half of 2025. With this investment, Liebherr is positioning itself as a future-orientated company that is ready to meet the challenges of growth, technology and sustainability.
www.liebherr.com