www.magazine-industry-usa.com
04
'23
Written on Modified on
DURR Modular components for scalable plant engineering in the paint shop
EcoProWet PT is a flexible and scalable wet system for body pretreatment that takes much less space and time to build than classic immersion tanks. The system saves on energy and materials, and is particularly suitable for small to medium production capacities.
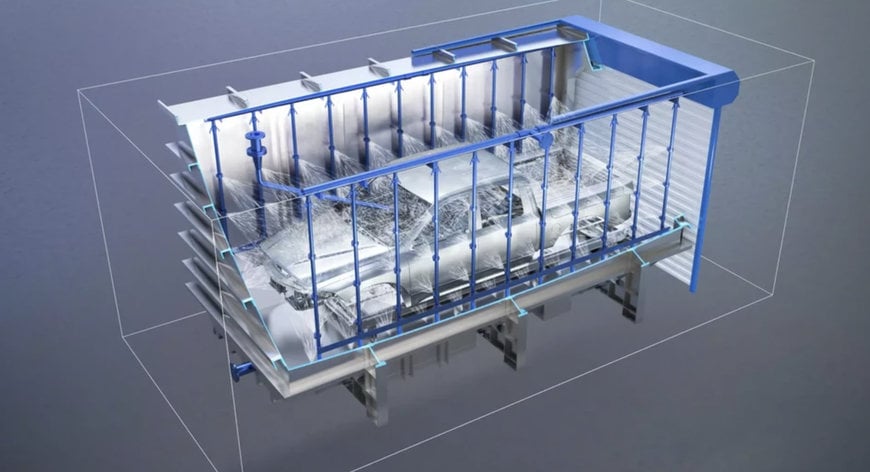
In vehicle painting, pretreatment is still one of the process steps that takes up the most space in a plant. This is because the tanks for cleaning and electrocoating are designed for the biggest vehicle body dimensions and for the longest process times in each case. With EcoProWet PT, Dürr has developed a new modular pretreatment system that is revolutionizing systems for small and medium capacities with a scalable, space saving and sustainable solution.
Modular design instead of big immersion tanks
The first station in the painting process is pretreatment, where vehicle bodies coming through from the body shop are cleaned, degreased and prepared for subsequent coating. The second process step is electrocoating, which applies a primer to the body to protect against corrosion. Up to now, the RoDip® rotational dip process has been used at Dürr for efficient immersion and draining processes. The EcoProWet PT pretreatment system is a completely new alternative to the established method.
Instead of using large tanks, the innovative system design from Dürr envisages compact chambers, which are flooded or designed as spray chambers depending on the process step. At the process level, the body is loaded through a roller shutter door into the tunnel on the cross transfer cars, which bring them to the respective process chambers. For future series systems, up to five of these cross transfer cars are planned, which work in previously defined sections and bring the bodies to the chambers.
Like the chambers themselves, all elements of the system have a modular design not only for efficient logistics, but also short assembly and commissioning times during construction. This applies to the tunnel, the steel structure, the conveyor technology and the door that securely seals the flooding chamber. Thanks to the solid construction, it can withstand the water pressure even during flooding or when the chamber is completely full. The optional insulation in the door greatly contributes to the system’s energy efficiency by reducing the amount of heat loss to a minimum.
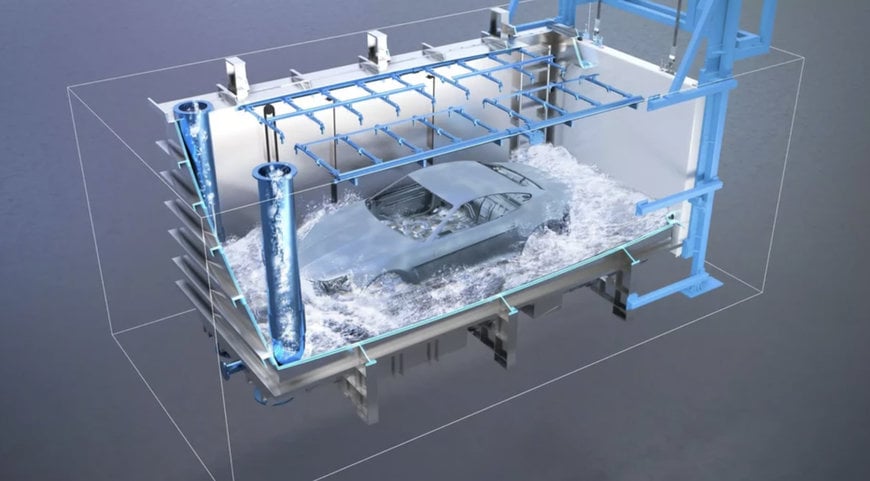
Environmentally friendly pit stop for deep cleaning
In the spray chamber, the bodies are treated using a large number of nozzles, which can be directed to different areas and can be flexibly switched on and off according to the size and shape of the bodies. In this way, even critical areas like door sills can be reached. A lance with a special rotating nozzle also ensures targeted and efficient cleaning of the interior.
In the flooding chamber, the treatment fluid is fed into the chamber from a buffer tank located above. The resulting momentum further helps to clean the body, and only as much fluid is used as needed for the respective size of the car body. The filtration process to recycle the cleaning fluid takes place in the full volume flow on the way back from the counter tank to the buffer tank.
In series operation, the cycle times and system modules are coordinated with each other in such a way that the buffer tank is filled whenever fluid is needed. Since the pumps are likewise controlled in accordance with the actual need, the energy required for them to run can be reduced to a minimum.
Modern thin-film process instead of zinc phosphating
In automotive paint shops, the previously common pretreatment process of zinc phosphating is being replaced by new thin-film processes that minimize the use of environmentally harmful chemicals and the cost of wastewater treatment. These thin-film processes have become successfully established on the market, and already today meet the high requirements for corrosion protection. The EcoProWet PT pretreatment system developed by Dürr is perfect for thin-film processes. The system was developed in close cooperation with the leading chemical manufacturers. Together with the two European market leaders BASF/Chemetall and Henkel, Dürr has already carried out extensive test series to validate the new system concept at its headquarters in Bietigheim, Germany, in a purpose-built pilot system.
The evaluation of the test results by the chemical suppliers proves just how well suited the system concept is to modern, environmentally friendly thin-film processes. It also confirms the high flexibility of the system, which enables an optimized process design for different substrates and body types. Through the close cooperation, Dürr has succeeded in developing a system that meets the sustainability requirements of future production processes to a special degree.
www.durr.com