Comau’s Advanced Automation Solutions Increase Stellantis Manufacturing Efficiency And Flexibility in Brazil
The automatic manufacturing system grants full flexibility to handle multiple model configurations for each of the two distinct SUV body frames in addition to the brand’s other vehicles.
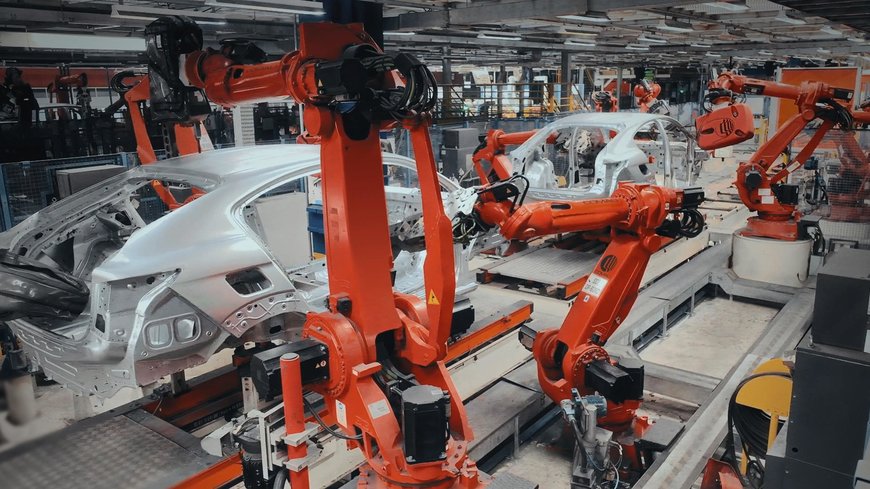
- Comau has designed new and retooled lines featuring 74 automatic and 10 manual stations to sustainably manufacture the mainline, body sides, respot assembly and welding activities for both vehicles
- The solution also minimizes tool change processes, saving time, costs and line intervention requirements, with a subsequent impact on sustainability
- Virtual Commissioning and process simulation were leveraged to program the complex stations and optimize on-time delivery targets
Comau has designed and deployed its advanced automation solutions at the Stellantis Automotive Plant in Betim - Minas Gerais as part of a comprehensive retooling project to produce both the Fiat Pulse, the brand’s first SUV model in Brazil and the Fiat Fastback, its first SUV Coupe and one of the company’s main launches for the local market. As part of the comprehensive project, Comau has enhanced an existing manufacturing platform to provide high-speed body assembly solutions for the main body, the body sides and the respot operations such that the two distinctly different SUVs could be produced on the same line.
In particular, Comau has responded to the customer’s needs by leveraging its technical know-how in diverse engineering fields to integrate 74 automatic and 10 manual stations with vision systems, digital applications and turn-key equipment. The complete solution places a strong focus on the geometry precision and welding accuracy of the underbody and sides.
Comau also utilized Virtual Commissioning and process simulation to optimize the design and retooling of the complex welding lines, allowing the team to test their functionality prior to the onsite commissioning. By doing so, the team was able to anticipate eventual issues in robot sequencing and communication between robots and PLC. In creating a comprehensive view of the plant in a virtual environment, Comau and Stellantis engineers were able to identify improvement points, enhance processes monitoring and make better use of the legacy plant equipment – essential aspects for an effective design-to-cost approach.
Furthermore, the Industry 4.0 initiative deploys IO-Link technology to help monitor the water and compressed air feeding, essential elements for the line functionality. This lets the system provide real-time data analysis and detect eventual issues in a fast and highly effective way. It also allows remote configuration and monitoring. Similarly, the integration of PLC software to optimize maintenance activities and the possibility to conduct robot backup activities via the corporate network help increase the long-term reliability of the entire line.
With safety and flexibility as two essential pillars of the project, the highly productive manufacturing line has been designed to minimize tool change processes, reducing commissioning time and line interventions with a subsequent impact on overall sustainability. This will allow the customer to easily manage its multi-model manufacturing needs in a more efficient and cost-effective manner.
“Beyond addressing the inherent automation challenges, the Comau team was quick to propose and integrate key technologies to meet our quality and cycle-time objectives,” said Glauber Fullana, Manufacturing Vice-president for Stellantis South America. “This project, which is part of our Industry 4.0 strategy, has given us more agility and the flexibility to manufacture different versions and other models on the same lines.”
“The successful launch of this complex project is proof of Comau’s strong commitment to excellence and technological innovation” said Laerte Scarpitta, Comau Leader for the Americas. “Our turn-key manufacturing solution allows Stellantis to enhance an existing platform to fully meet its near-term productivity, quality and market volume goals, all while ensuring the possibility for future expansion as needed.”
Backed by a solid set of skills derived from decades of experience with the customer, Comau has leveraged its local presence and 50 years of expertise in automation, digitalization, and intelligent technologies to meet the demanding requirements of this project. Indeed, as a global automation leader Comau brought its manufacturing methodologies and cutting-edge technology to serve the Brazilian industry.
www.comau.com