www.magazine-industry-usa.com
04
'15
Written on Modified on
Valve Doctors® provide bespoke solution to increase power generation at nuclear plant
When the engineers at Exelon's Peach Bottom Atomic Power Station (PBAPS), located in Pennsylvania, had to upgrade the facility's residual heat removal (RHR) system, they called upon the expertise of IMI Critical Engineering, a leading global provider of flow control solutions. The result was a bespoke solution and customised testing programme that have complied with very demanding specifications to ensure efficiency, safety and regulatory compliance.
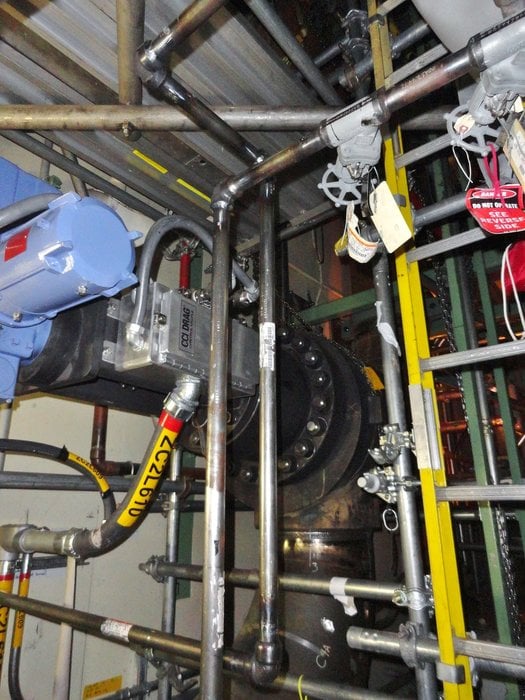
At the heart of that RHR system lie eight motor-operated control valves. These ensure precise distribution of the water flow between heat exchangers, while protecting the costly RHR pumps.
At PBAPS, IMI Critical Engineering’s Valve Doctors® – top-class engineers who have completed an internationally recognised training programme - and the facility's own engineers worked closely together to create a fully customised control valve that meets the very demanding specifications involved. The solution is based on IMI CCI's DRAG® velocity control technology, designed to prevent cavitation and pipe vibration, and takes the form of a durable MOV, with a cartridge-trim assembly containing six distinct flow control zones across the valve's 12” stroke.
Particular benefits of the solution include a minimum-flow region to protect against line vibration, a quadri-linear normal operating region and a large window over-capacity region for emergency flow use.
Given the complexity of the valve, and the plant's rigorous requirements for accurate flow evaluation, IMI CCI and PBAPS had to develop a customised – and very extensive – Cv test programme. The process was made particularly challenging by the strenuous accuracy requirements that applied in this case. The ANSI/ISA S75.02 standard for valve Cv testing stipulates that an accuracy of ±5% is attainable by using the recommended methodologies and instruments. However, in this case an accuracy of ±0.5%, ten times tighter, was required.
The evaluation took place at two test facilities using both compressible and incompressible fluids. In order to meet the accuracy requirements, IMI CCI used specialised flow testing equipment housed at a major research university, as well as IMI CCI's own facility in California. The trim hardware was fine-tuned in response to the testing outcomes at IMI CCI's factory. As a result, the testing programme successfully validated the valve's capabilities.
The unique design of the IMI CCI valve, with its counter-balanced cartridge trim design, made it straightforward to install. The bespoke nature of the solution and the testing programme ensured that the final system functioned precisely as required, and PBAPS is set to install the remaining valves for its second unit during planned downtime later in 2015. Once again, the globally-recognised expertise of the Valve Doctors® has proven its value.
For further information visit www.imi-critical.com