www.magazine-industry-usa.com
04
'15
Written on Modified on
Bulkscan® LMS511 Laser Volume Flowmeter
Anyone who uses conveyor systems in their working environment knows that incorrect measurements must be avoided, otherwise the machines and belts could be so badly damaged that production comes to a complete stop. Dedicated to harsh environment, the Bulkscan® LMS511accurately measures mass and volume flow continuously in a non-contact process and also identifies the fill level and the center of gravity of bulk materials on belts.
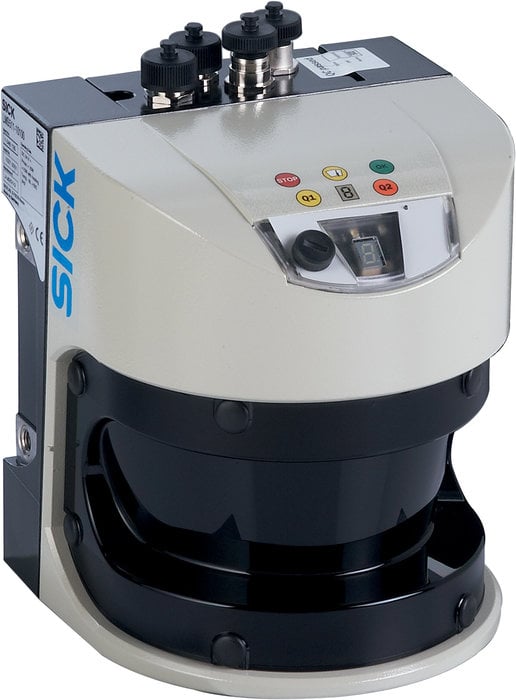
Those looking to measure quantities of bulk materials on belts can now opt for a precise measuring process in the form of the Bulkscan® LMS511. Up until now traditional belt scales have always been used. These are simple and cost-effective, but they do have their pitfalls. Operators tend to experience problems when it comes to the accuracy of the weight measurement. The low level of measurement stability and the sensitivity of these devices, particularly in harsh conditions, also interfere with the production process. This process is a lot easier if the system can monitor mass flow as well as volume flow. This requires non-contact laser technology to be installed in rugged hardware suitable for outdoor use.
Volume, level, and center of gravity
The Bulkscan® LMS511 measures volume flow continuously in a non-contact process and also identifies the fill level and the center of gravity of bulk materials on belts. And thanks to multi-echo technology, it always works regardless of the weather (rain, snow, fog, dust) or the composition of the material at hand. Not even reflections in glass can disrupt the laser volume flowmeter. The laser beam detects the height profile of the bulk materials as well as volume and throughput, at sensing ranges of up to 20 meters. For instance, stones of an excessive size can be detected in good time, before they are able to block downstream system components. Using the integrated center of gravity calculation, the scanner monitors the belt load over the complete conveying line and recognizes one-sided loads or one-sided belt loads. It can even detect movements in the belt at an early stage, helping to make sure that the belt does not suffer high levels of wear and tear.
Minimum maintenance, maximum cost-effectiveness
The special housing design ensures that the Bulkscan® LMS511 is rugged enough for outdoor use. It is installed above the belt, preventing it from being contaminated by the bulk materials. Furthermore, the measurement process is not affected by horizontal forces from the belt's rollers or plates. Functions for self-monitoring and auto-calibration increase the system availability; for instance, integrated sensors check the transparency of the front screen of the Bulkscan® LMS511 and generate an alarm signal if the value falls below an adjustable threshold. This function also reduces the maintenance work. The scanner reports automatically when cleaning is due. These devices can conduct measurements with the utmost operational safety, even in Siberian temperatures. An integrated heating system switches on at +5 °C and provides heat, even at temperatures as low as -30 °C. Even if a worst case scenario should occur, the system can be quickly put back into action. Finally, the modular concept ensures optimized spare part logistics and quick and straightforward replacement of the components concerned.
Xaver Meier, Head of Marketing & Sales for Industrial Instrumentation & 3D Compact Systems, SICK AG, Waldkirch, Germany
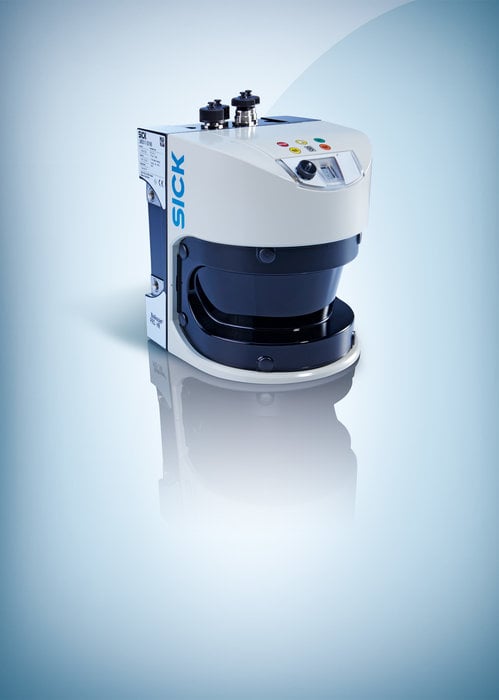
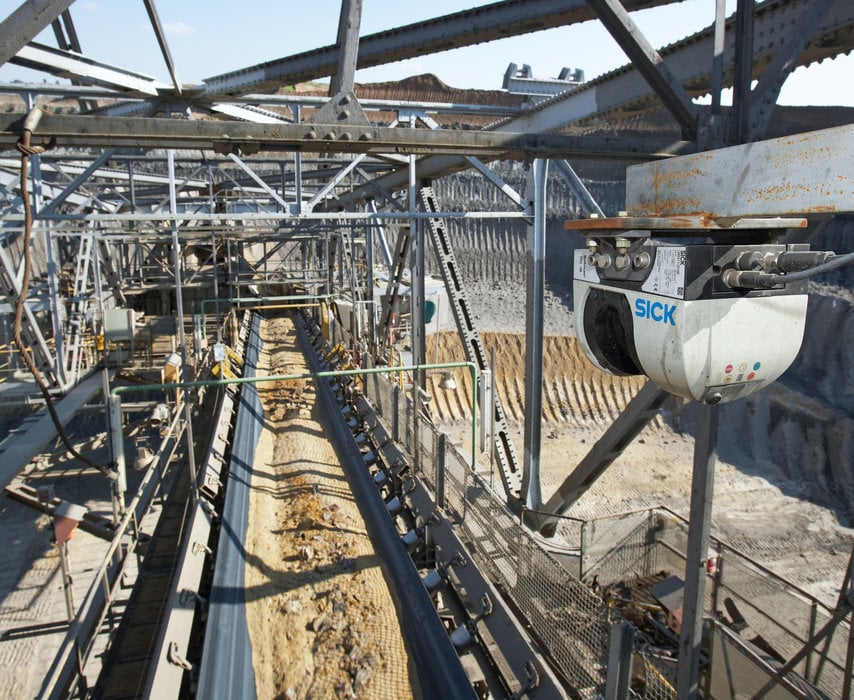