www.magazine-industry-usa.com
27
'15
Written on Modified on
New building insulation production line is a cut above - thanks to Prosaw, Brammer and NSK bearings
Combating contamination in bearings is one of the single most effective ways to extend bearing life and consequentially to reduce the maintenance requirement of the machinery they are fitted to. When high quality band saw manufacturer Prosaw found that bearings were regularly failing on automated saws that had been supplied to a prominent manufacturer of building insulation, both Prosaw and the end user needed a solution quickly.
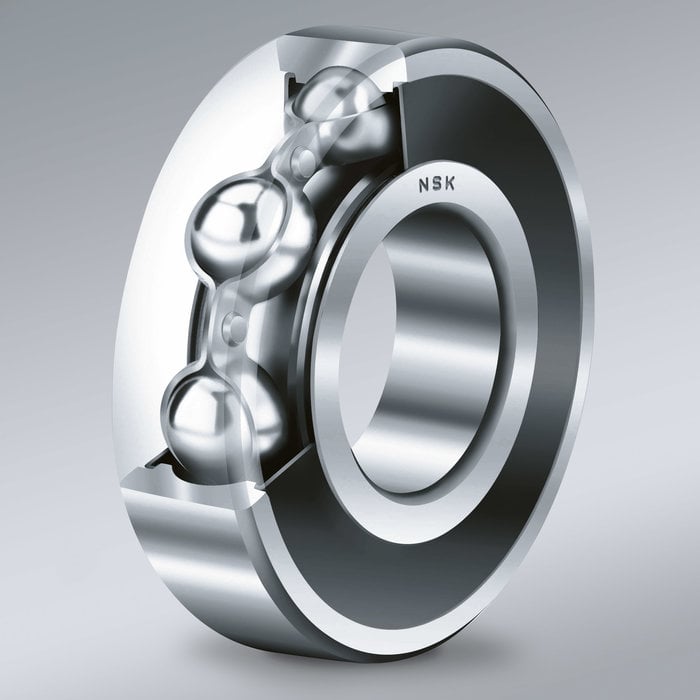
Since such a large number of NSK bearings are employed as replacement items and can often deliver huge savings in bottom-line costs, NSK operates a specific service, available via NSK authorised distributors to identify and deliver cost savings. NSK’s Added Value Programme, AIP, uses the expertise of NSK engineers to help customers improve efficiency, reduce breakdowns and improve profitability.
The AIP process can involve a comprehensive review and analysis of a company's operation before making a number of recommendations for improvements which can deliver significant savings for the client. In the instance of Prosaw, it was one application, but often the scope of the service can extend to an entire production facility.
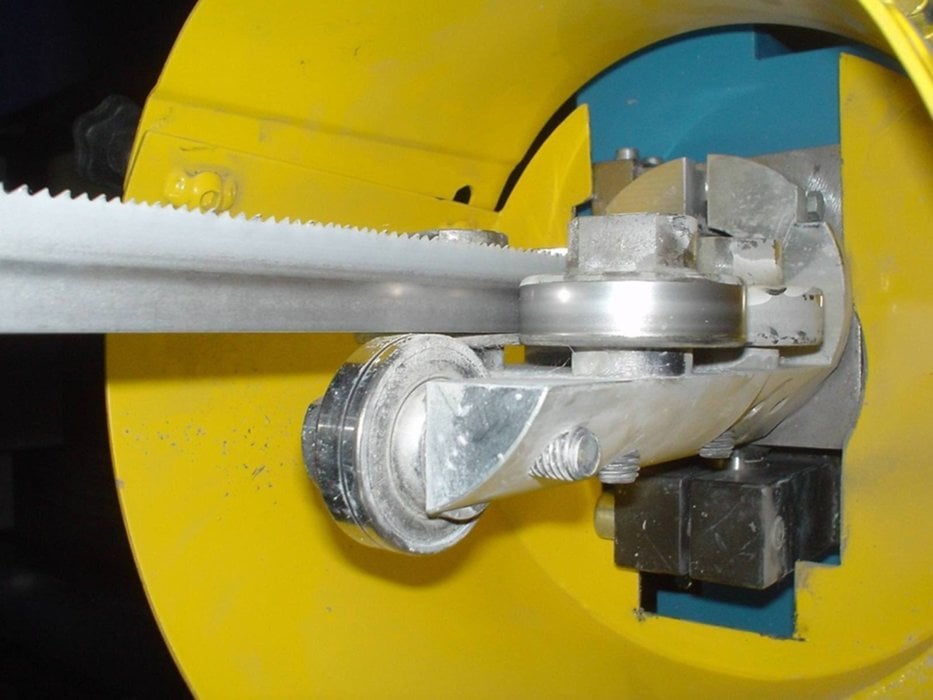
Simon Grant, Business Development Manager at NSK who was involved in the project, explains how severe the problem was and how a solution was found. ‘Once Brammer, the client’s chosen MRO supplier and an NSK authorised distributor, had alerted us to the situation the first thing that stood out was that both Prosaw and the customer’s maintenance team were fitting good quality bearings from recognised brand manufacturers. The second was the severity of the issue; these bearings, used primarily on the followers that keep the saw blade in position, were in some cases only lasting a matter of hours before they seized.
To the casual observer cheap bearings look the same, or similar, to quality branded bearings, it is our job to explain that there are differences in everything from the internal geometry of the bearing design, to the dimensional accuracy of the raceways and the rolling elements, to the hardness and purity of the steel that they are made from. The overall result of all these differences combined can be night-and-day in terms of life-span between a cheaper bearing and a good quality branded item.
We are often called-in by OEM machine manufacturers and end users looking for improvements in machine longevity or reduced maintenance; these requirements are easily met when the customer is using cheap bearings, exchanging for a good quality bearing can be transformative in terms of performance and operating life. When they are not using cheap bearings, however, then innovation is called for.
In this case we needed to look further into the application for the cause of the issue. The band saws were being used for cutting insulation panels to size on a busy production line. The downtime that the bearing failures were causing was totally unacceptable. Prosaw had supplied the saws with good quality general application bearings fitted which had performed well in other applications in the past and hence gave no reason for it to expect this type of failure mode.
As soon as we saw the application we realised that, although perfectly stable in its solid form, the insulation material produces fine abrasive particles when it is being cut with a saw blade. While no issue on a building site, the particles were an issue in production; working their way through the standard bearing seals, sticking to the lubricant inside and creating a fine lapping paste which was wearing the bearings out extremely quickly.
Just to be sure, and to provide the customer with some empirical evidence that we were correct in our prognosis, the application engineer carried out a bearing inspection at the European Technology Centre based at NSKs largest UK manufacturing site in Newark. The results were conclusive; the bearings were failing due to particulate ingress.’
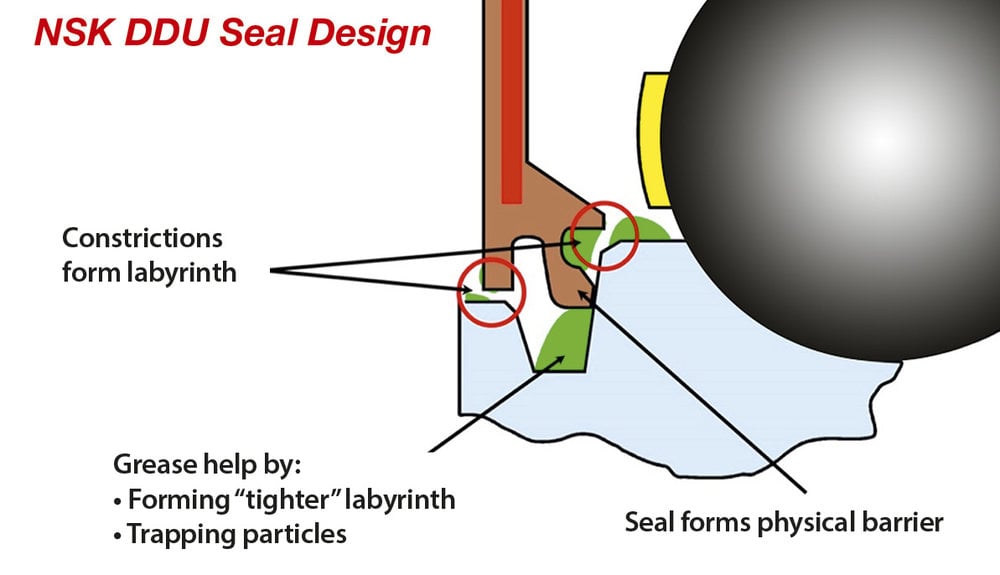
The obvious solution was to recommend the use of NSK Deep Groove Ball bearings with the high performance DDU sealing arrangement. These bearings are designed specifically for use in dusty environments and employ a face riding contact seal located in a groove in the inner ring. This unique design allows the DDU seal to form a labyrinth as well as a contact seal, further improving grease retention and resistance to contamination ingress.
NSK DDU seals give improved seal performance particularly when compared to traditional ‘2RS’ seal designs which only seal against the smooth cylindrical surface of the inner ring shoulder or at best against a recess in the inner ring side face. The DDU design keeps particulates at bay and effectively protects the bearing grease in a dusty environment.
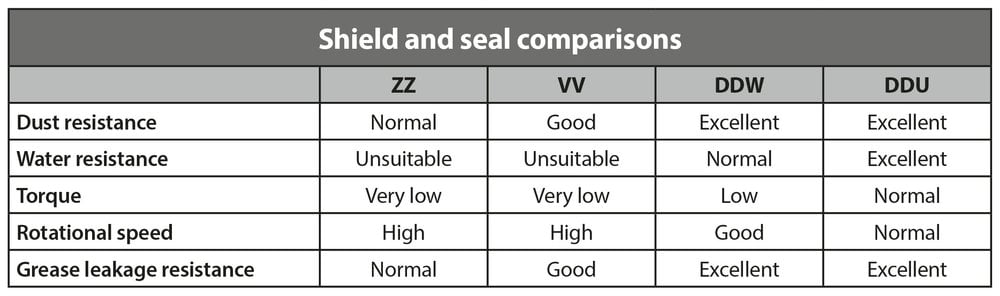
The results have been spectacular; the bearings on the saws now last several weeks rather than hours and are replaced during scheduled maintenance windows. The overall saving, including the cost of downtime, is in the order of hundreds of thousands of Pounds.
This result is a perfect example of an MRO supplier, in this case Brammer, providing the type of maintenance support service they strive to deliver and shortcutting the process of returning to full production by calling in an expert component supplier to find a solution.
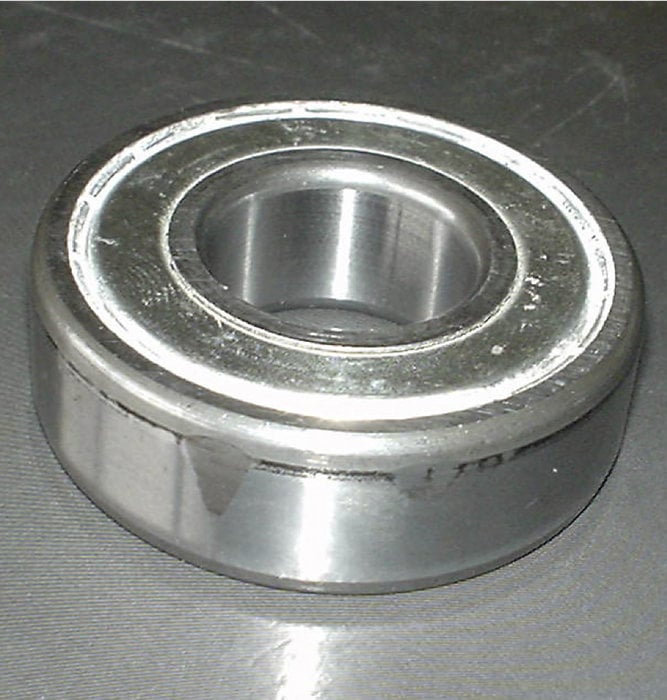