www.magazine-industry-usa.com
30
'22
Written on Modified on
METALWORKING: DIGITAL AND FUTURE-ORIENTED
The who's who of the industry will meet at AMB from September 13 to 17, 2022 at Messe Stuttgart. SCHUNK is also part of the community that is burning with passion and commitment for metalworking. After a long hiatus, this community is finally coming together again in person. The technology leader will be showcasing automation and digitalization options for machining as well as new developments in the field of sustainable, resource-efficient clamping devices.
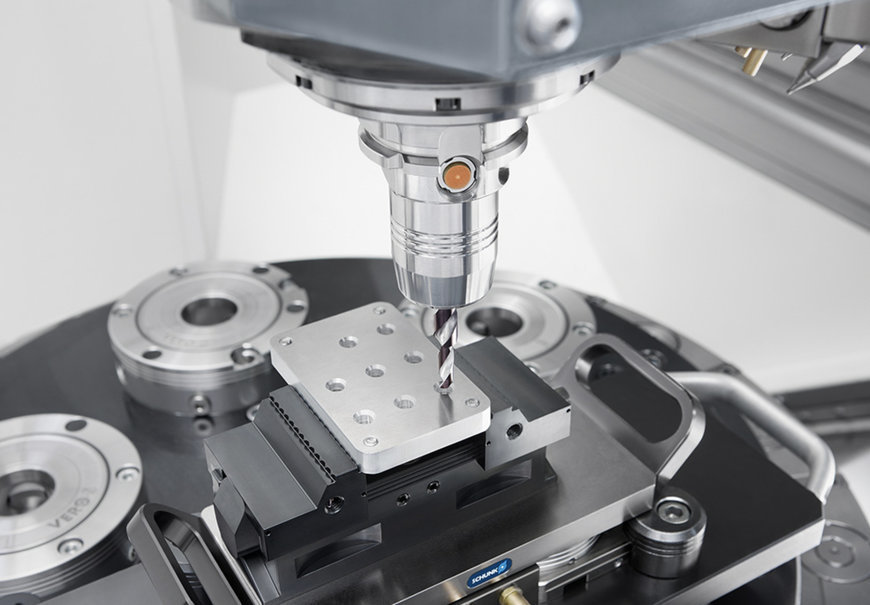
Metalworking is in a state of great transition. The latent shortage of skilled workers together with supply chain problems, environmental aspects and the resulting changes in sales markets are placing new demands on the industry. Where the focus used to be exclusively on precision and time savings, flexible approaches are now required in order to be able to process small quantities or to change tasks in a cost-effective manner. At AMB SCHUNK will be showcasing what has to be done to make metalworking processes more efficient, flexible, and sustainable. Modularity, networking, and automation capability have allowed the function-integrated clamping devices from the technology leader to reach a whole new level.
Flexible machine loading and unloading
The application expert is now offering even more options in the field of automated machine loading. The TANDEM3 modular system for stationary use now has an additional component for flexible workpiece clamping with the new KRP3 centric clamping vise. With this powerhouse, even round workpieces can now be clamped automatically from the outside and inside in confined spaces. Like all stationary clamping devices from SCHUNK, it can be quickly and easily mounted on the VERO-S quick-change pallet system using console plates, which allows changes to be made as required. The clamping force block is also available in hydraulic (KRH), spring-loaded (KRF) and electric (KRE) versions. If you are still at the beginning of your journey and planning a cost-effective partial automation of your machine tool with a cobot, the new MTB application kits offer a convenient approach to automation. The grippers and power vises included are adapted for metal cutting machining and can be combined with robot-specific connections.
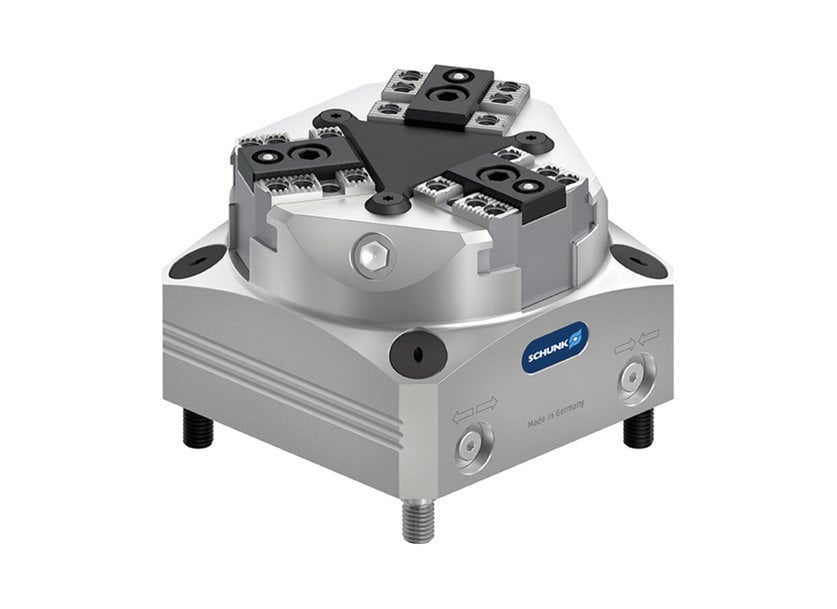
The TANDEM3 modular system for stationary use now has an additional component for flexible workpiece clamping in automated machine loading with the new KRP3 centric clamping vise.
More process transparency
With its sensory modules, SCHUNK is now offering even more transparency in the clamping process. These modules provide the parameters of the clamping situation during operation. The SCHUNK portfolio includes, for example, the VERO-S NSE-S3 138 quick-change pallet module. Pallet presence and module clamped/opened can be permanently monitored, allowing users to always keep the overview of the process status. SCHUNK is now also offering additional monitoring options for the quick-change pallet modules from the NSE3 series. The new VERO-S AFS3 IOL sensor identifies the respective clamping status and reliably reports whether the modules are open or clamped. An inductive proximity sensor also indicates whether there is a pallet above the modules. This smart interaction of the electronic monitoring system offers users more safety in automated workpiece clamping. Data is exchanged via the IO-Link interface.
Variety in workpiece clamping
SCHUNK is also looking forward to finally being able to demonstrate the unprecedented versatility and low-maintenance features of its manual chuck ROTA-M flex 2+2 live. The centrically compensating 4-jaw chuck has a long compensating stroke. Whether round, cubic or irregularly shaped, this allows countless workpiece geometries to be clamped on mill/turn centers with just one clamping device. Special seals ensure reliable clamping force and long maintenance intervals. This multi-talent for machining raw and finish-machined parts has been further developed and optimized. The new KSC3 manual clamping force block is corrosion-protected due to its nickel-plated base body, thereby providing longer process reliability in use. The even flatter design and a wide variety of jaws also offer more application options in the parts spectrum. Its encapsulated spindle as well as a preset cleaning position of the chuck jaws reduces the maintenance costs.
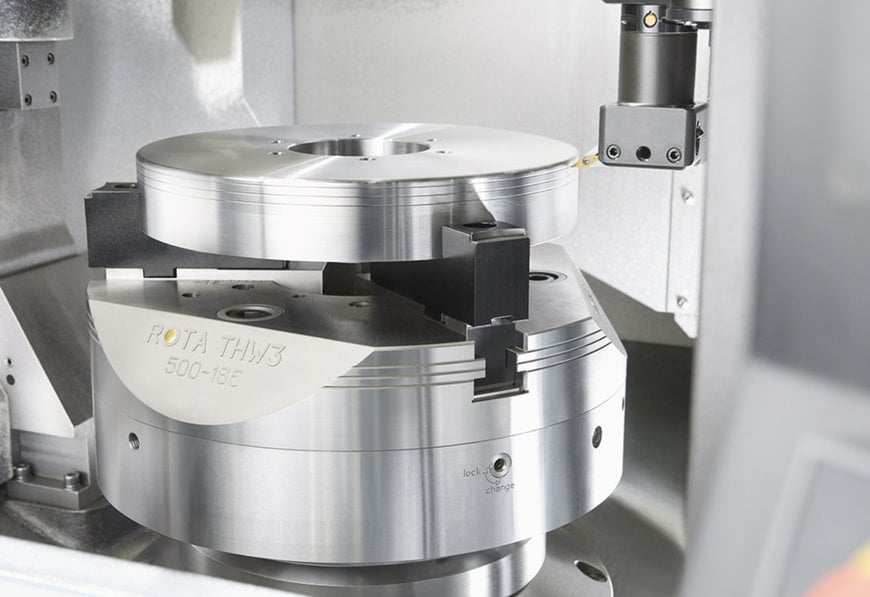
The flexible ROTA THW3 jaw quick-change chuck manages the balancing act between short set-up times and low maintenance intervals.
Awarded excellence and sustainability
In its product developments, SCHUNK focuses on approaches that save on resources and energy. The iF design award-winning ROTA THW3 jaw quick-change chuck manages the balancing act between short setup times and extremely long maintenance intervals. The developers of the lathe chuck have consistently saved weight; this reduces the energy requirements and enables faster acceleration and braking of the machine. The sustainable sealing concept ensures up to 10 times less lubricant consumption than comparable lathe chucks. The smart iTENDO² toolholder will also attract attention at AMB. It provides "closest to the part" data in real time and detects tool wear at an early stage. In addition to process-reliable machining, the intelligent toolholder ensures a longer tool service life and fewer rejects. SCHUNK now offers the toolholder, which received the German Innovation Award 2022, in a new variant iTENDO² easy connect with a simple data interface that can be used for machine and process monitoring.
www.schunk.com