www.magazine-industry-usa.com
24
'22
Written on Modified on
Unique Alloy Substance Can Help OEMS Reduce the Risk Of ADAS-Related Recalls
A global automotive materials specialist has demonstrated the reliability benefits of a unique alloy substance that can replace traditional tin/silver/copper (SAC) alloys in the design of Advanced Driver Assistance Systems (ADAS). Internal tests suggest that this alternative alloy can play a significant role in helping automotive OEMs eliminate the risk of solder fractures, a potential cause of failure in ADAS hardware.
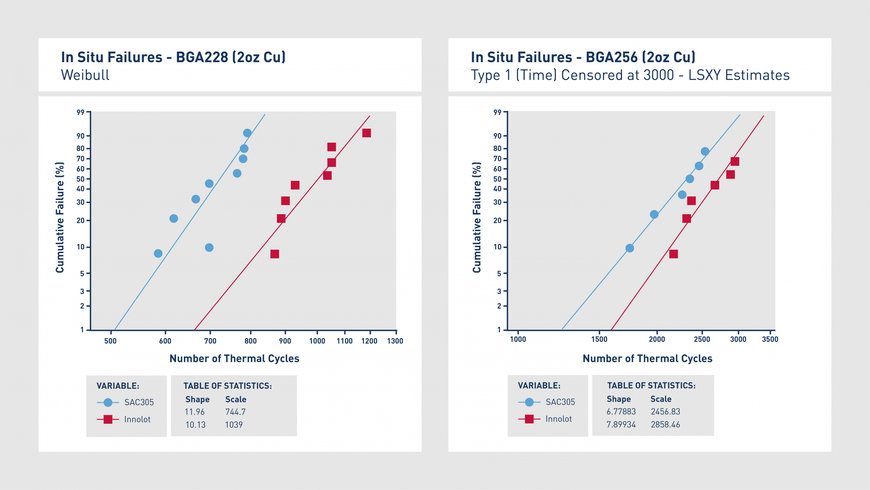
ESI Automotive held a series of quality tests to assess the reliability of Innolot alloys compared to conventional SAC and tin-silver (SnAg) alloys. The Innolot alloy was developed with the automotive industry for use in high temperature environments where vibration is also a factor. It is designed to offer significantly improved creep resistance, particularly when operating in temperature extremes such as within an ADAS circuit board assembly.
“We ran a series of thermal cycling tests, pitting Innolot against the traditional SAC alloy. For this, we tested the alloy on two different ball grid arrays (BGAs), which are surface mount packages being used more in advanced safety designs,” explained Lenora Clark, Director of Autonomous Driving and Safety Technology at ESI Automotive.
“Our testing demonstrates that the size of the package, the pitch and the overall input and output does influence the characteristic life of the solder joint. Using both a 228 BGA and 256 BGA, the Innolot alloy improved solder joint reliability by a defined percentage when compared to the traditional SAC alloy. The percentile difference was 39% for the 228 BGA and 16.3% for the 256 BGA. This is a significant difference in reliability. Our results conclude that the creep resistance properties of the Innolot alloy offer significant improvements in reliability over standard SAC.”
Lenora added: “This is significant when you consider the context of carmakers progressing vehicle designs towards level three autonomy. Traditional solder alloys are still commonplace within ADAS hardware designs but as we move vehicle systems towards level three autonomy, we need to consider alternative options.
“People don’t always think about ADAS operating in harsh environments. These systems are doing a high volume of processing and therefore generate their own heat as part of this function. In addition, because these systems are safety-critical, carmakers need to ensure they are reliable enough to withstand up to 3,000 thermal cycles. This cycle of constant heating and cooling is too extreme for traditional solder to withstand in new vehicle designs, necessitating the need for a high reliability alloy such as Innolot, to reduce the risk of ADAS failure and associated warranty and recall situations.”
For more information about ESI’s materials for ADAS hardware, visit
https://esiauto.com/safety-systems-adas