www.magazine-industry-usa.com
22
'21
Written on Modified on
Variance and volume advantageously combined One of a kind in series
Up until now, users in the metal and plastics processing industries often faced a difficult choice: with CNC lathes and milling machines, one opted either for the largest possible variance or for large volumes, i.e., high quantities. An innovative solution from the Netherlands makes both possible and simultaneously lowers the threshold for automation. In the servo-controlled gripper jaws, brushless DC-servomotors with integrated Speed Controller from FAULHABER provide the necessary precision and reliability.
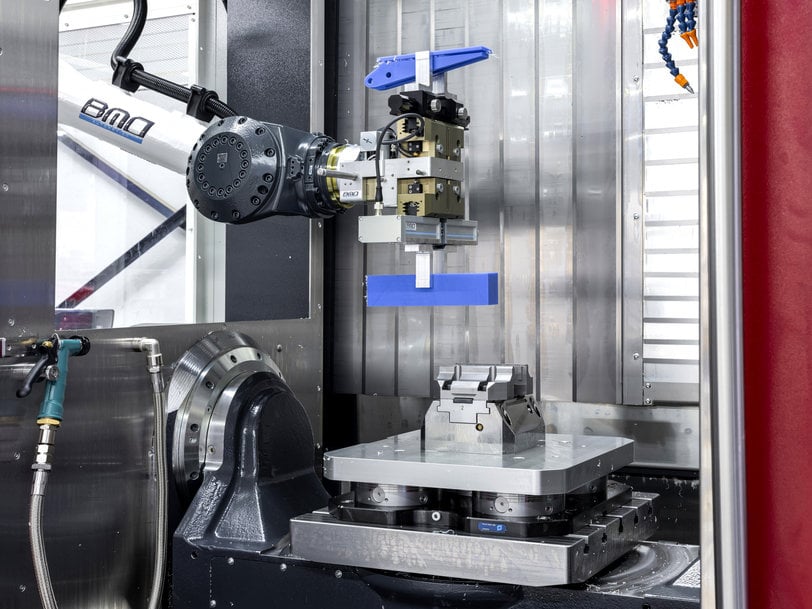
Dutch company BMO Automation started in 2008 with the vision of a significantly more effective loading of CNC lathes and milling machines. Customers, mainly from the metal and plastics processing industries, can make use of modular complete solutions for the machining industry characterised by high-quality, user-friendly and flexible automation solutions. Working in collaboration with FAULHABER, the result was a servo gripper that is connected to a robot arm in the robot cells. These cells are used for the automatic loading and unloading of CNC lathes and milling machines.
Game changer
With their robot cells, BMO Automation from the Dutch town of Nederweert in the province of Limburg enables automated production of widely varying batch sizes with quantities as small as a single unit. "Performance at BMO is defined as flexibility² times productivity. Using the servo gripper developed by us, flexibility is increased significantly and customers can automate for batch sizes as small as 1. This is the future!" stresses Marketing Manager Maarten van Bun. "A simple robot or cobot performs the same job 1000 times. But we believe that the future is more likely to be the automation of smaller product series in a single pass. We call this multi-batch automation. We can also automatically manufacture 1000 parts, but split into multiple series with low volumes. The result is both high mix and high volume."
High mix & high volume
The margins in the manufacturing of small quantities are generally higher than in mass production. At the same time, however, it is more personnel- and cost-intensive if the workpieces need to be manually loaded between individual turning and milling processes. Thus, a solution that achieves both high variances as well as high volumes when using CNC lathes and milling machines in the metal and plastics processing industries is a game changer. For their approach, BMO Automation combines the advantages of pallet automation with the option of also being able to load individual workpieces fully automatically. From the principle "high mix – low volume" thus becomes "high mix & high volume".
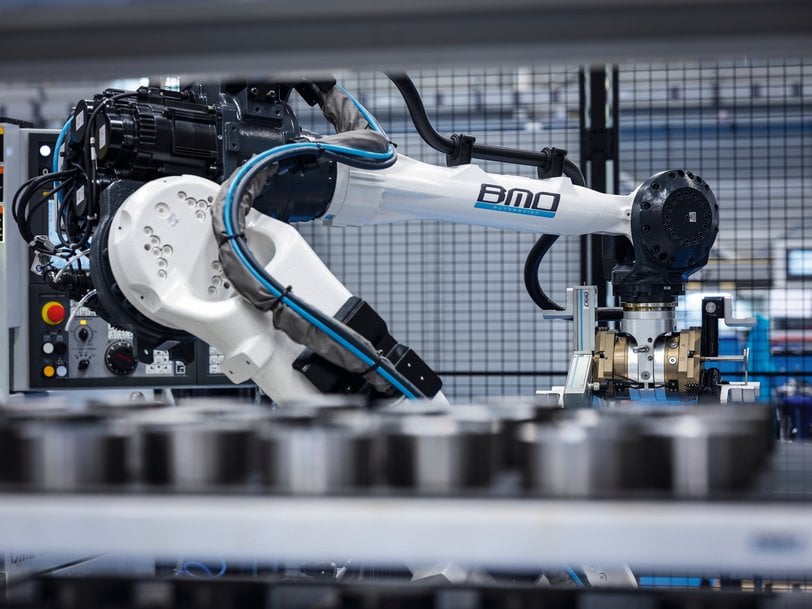
This is made possible by, among other things, servo-controlled gripper jaws whose precision and reliability are guaranteed by FAULHABER drives. In the servo gripper, a FAULHABER motor drives a gear spindle that is part of a linear guide system. The gripper fingers, connected to the guided blocks, thereby move to the desired position for the product that is to be loaded into the CNC machine. The dimensions of the workpiece can change following the turning or milling process. Here, the servo gripper automatically adapts the position of the gripper fingers and does so without changing the loading and unloading cycles. As a result, it is not necessary to change the gripper.
"Harco Hermans, responsible for research and development for us, knew FAULHABER from previous projects, where he had very good experiences with the Motion Control products," explains Maarten van Bun. The appropriate motor was selected using the Drive Selection Tool on the FAULHABER website. At the same time, BMO Automation received support from FAULHABER, for example, in checking the script files for communication with the BMO Intelligent Control Software.
Development lasted approximately one year, including a two-month test phase with reference customers. The biggest challenge was in integrating a reliable solution that is available in the smallest possible dimensions with a low weight and thereby has a minimal impact on the load capacity of the robot. "Here, FAULHABER offers a very compact and yet high-performance solution in both the mechanical as well as electronic part that convinced us."
Outstandingly innovative
A concentration in the area of CNC automation, many years of experience and good contact with manufacturers of CNC machines enables complete integration of robot automation in machining production. BMO is a leader here in the field of automation and digitization. This is also evidenced by three nominations to the TechniShow Award. The first nomination in 2016 was for an automation solution by means of which individual pieces and series could be manufactured in an ongoing process. This was made possible by the change of clamping means, pallets and products. At the time of the nomination, this was a true first. In 2018, BMO was awarded for the revolutionary Xenon software for Smart Industry 4.0. This is used to collect and link a wide range of data from CNC machines of a machining plant. In 2020, the company was nominated for the third time in a row for its Smart Centric E-Clamp, but did not prevail this time.
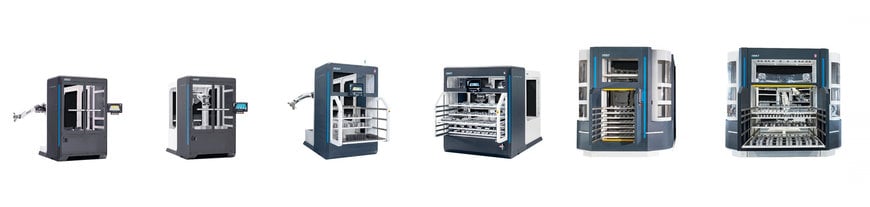
"CNC automation increases productivity, reduces processing time and offers a way to avoid issues associated with the shortage of specialists," states Maarten von Bun. The advantage of an automated robotics solution also proved itself during the Covid-19 pandemic. "Corona had a large impact on the metal industry. At the start, customers were more conservative with investments. The segment quickly changed, however, as it became clear that CNC automation is not only a solution for the future but also for today. A robot does not fall ill and, even with limited working hours, a human operator can maintain the production level together with a BMO robotics solution."
Automated manufacturing also makes production possible on-site, thereby eliminating the disadvantages of outsourced production, such as closed borders, restrictions on travel and the movement of goods, longer border and customs inspections and local lockdowns, as have been experienced during the pandemic.
"If you would like to automate, it is important that a precise process be created that constantly guarantees a high level of safety. This precision and, in particular, the repeatability are important; because everything happens fully automatically, the error rates are low and our automation solutions function without an employee needing to be present. A reliable process is, therefore, extremely important. The products from Faulhaber guarantee us quality, safety and nothing that we need to worry about. We know that it’s good and trust the products that Faulhaber offers us," summarises Maarten van Bun.
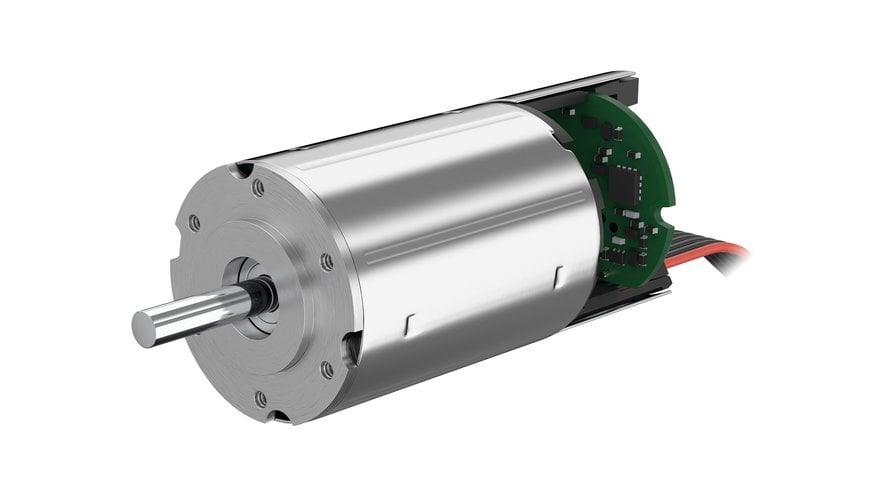
Faulhaber BX4 5C