www.magazine-industry-usa.com
31
'21
Written on Modified on
HS2 reveals new piling innovation with huge potential benefits for the construction industry
New Zero Trim Pile Technique, utilising a vacuum excavator, has been successfully tested on HS2
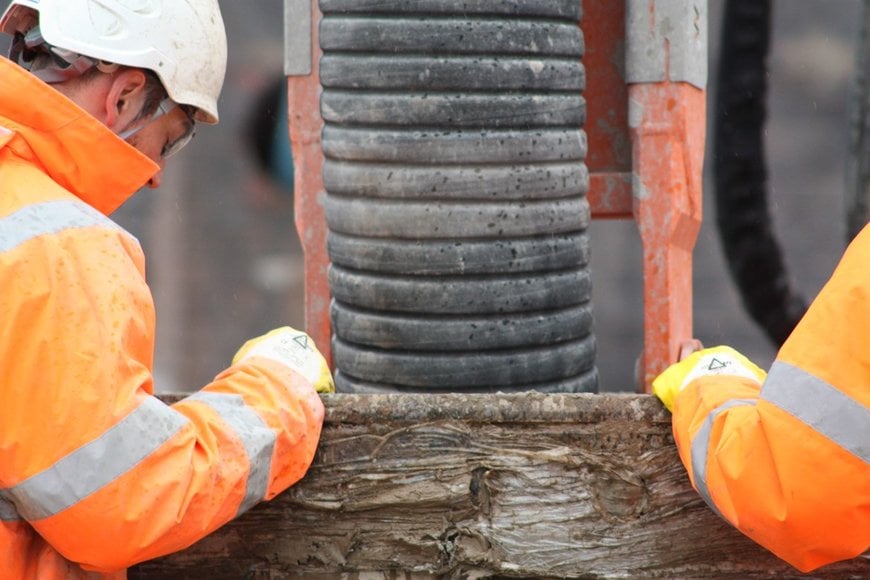
HS2 Ltd has today revealed a new vacuum excavation technique for piling which could have massive benefits for the wider construction industry in the UK and abroad. The innovation, developed by specialist contractors working on HS2, is better for the environment, safer for workers and reduces construction noise, to the benefit of neighbouring communities and businesses.
Lee Piper, working for HS2 contractor Skanska Costain STRABAG joint venture (SCS JV), identified the opportunity to test a new piling technique and worked with a colleague, Deon Louw from Cementation Skanska, to develop the pioneering new approach.
The “zero trim pile technique” involves sucking out excess concrete whilst still wet using a new vacuum excavator technique. Traditionally in piling, concrete is overpoured and then workers have to break out the excess concrete. This can cause a lot of health problems, including hand-arm vibration syndrome, hearing loss and silicosis. By removing the need to break out excess concrete, this new approach is safer for workers, and also reduces the work hours involved in complex piling work.
Whilst vacuum excavation technology is not new, using it in this way in the construction sector marks a step change, and initial trials have proved overwhelmingly successful. HS2 contractors developing innovative new methods to deliver the project saw a promising opportunity and found a willing supplier to invest in machinery to test the approach. Hercules Site Services, a company from Cirencester, were keen to develop the technology, and provided a machine for use on site in the Euston Approaches, for use on real life piles. Materials excavated were then sent off for lab testing and reports.
Lee Piper, Site Superintendent for Skanska Costain STRABAG joint venture said:
“I have worked in the construction sector for over 20 years, and the same piling techniques have been used throughout that time. Working with colleagues I saw an opportunity to try a new approach and was supported to do so by HS2.
“This technique could be transformational for the construction sector, reducing the health risk that results from breaking piles. The additional benefits of noise reduction, time and carbon savings mean the technique should be attractive for the whole sector to use going forward.”
Deon Louw, Project Director, Cementation Skanska, said:
”This piling innovation has been developed as a result of a fantastically collaborative approach. This included trials with Hercules Site Services to perfect the vacuuming technique, together with extensive onsite testing to validate the integrity of the piles constructed using this new approach.
“We’ll be installing around 2,000 piles over the next three years in the Euston area. This zero trim innovation will bring amazing benefits in terms of reduced carbon, noise reduction and safer ways of working for our site teams. The potential health impacts associated with concrete breakdown are well known, so to be able to mitigate these risks from the outset is great for our people.
“Longer-term, we’ll be looking to see how we can use this innovation on future projects. It really does have the potential to be a game-changer for our industry.”
As the largest infrastructure project in Europe, HS2 is keen to support the construction sector to trial new innovative techniques to drive positive change in the industry. Working with its supply chain, HS2 can provide the certainty of ongoing work, creating an environment where innovative thinking can not only take place but be put into practice.
As well as having health and safety benefits and improving efficiency, the technique also reduces the noise from piling, which is hugely important for projects like HS2 where construction is taking place within communities and near operational businesses. Further, there are considerable cost savings and, done in the right way, there are environmental benefits, as the new technique uses less concrete. On HS2, the extracted concrete is retained and is being reused in construction elsewhere. Keeping the excess material on site and reusing it will reduce lorry movements to and from sites.
Malcolm Codling, Client Director for HS2, said:
“HS2 is an ambitious project and in order to deliver it, we need to innovate. We are proud to be supporting our contractors to deliver these world class transformational innovations, and to support them to be adopted across the project to help reap the benefits.
“At the site near Euston where this technique has already been put into practice, we estimate it will save 60,000 manhours, have a significant positive impact on the health and wellbeing of our staff, reduce noise for nearby residents as well as removing carbon from the construction process. Delivering this across the route could have a major impact on the HS2 project.”
The zero trim technique is currently being used on HS2 worksites near Euston and will extend to other sites across London where SCS JV are working. Discussions are also taking place with other HS2 contractors to see how it can be used further across the route.
www.hs2.org.uk