www.magazine-industry-usa.com
23
'21
Written on Modified on
Joh. Johannson Kaffe saves 85% CO2 with new plant
Bühler supplies technology for first ultra-low CO2-footprint coffee processing plant.
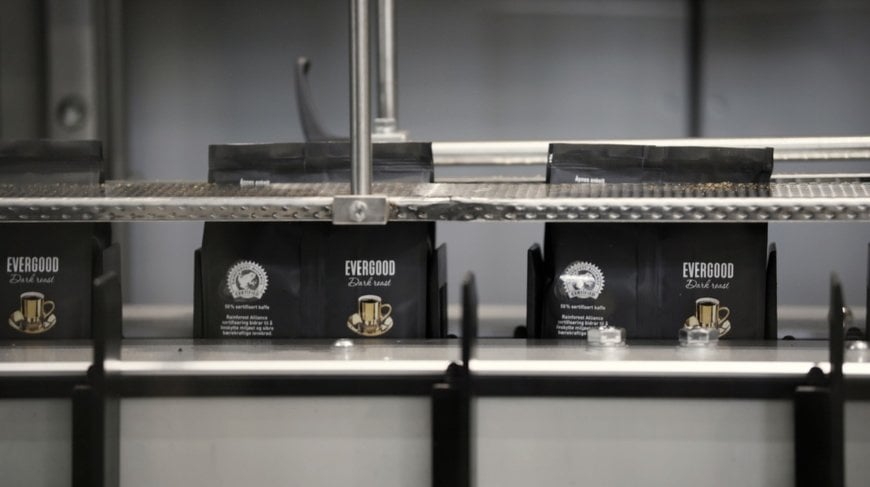
Together with Bühler, the leading Norwegian coffee producer Joh. Johannson Kaffe has built the world's first and only plant that consumes 85% less CO2 compared with conventional coffee production facilities. The new plant in Vestby has been in operation for about 10 months and will soon be producing at full capacity in three shifts. "We have asked a lot of Bühler. Thanks to their solutions, we are recovering nearly all the energy used in our roasting process. Together, we have achieved the goal of protecting the environment sustainably and for the long term. In addition, we save energy costs and are even more profitable as a result," says Bengt Ove Bitnes Hagen, Production Director at Joh. Johannson Kaffe.
When Joh. Johannson Kaffe awarded the construction contract for its new coffee processing plant to Bühler in June 2017, the Norwegian premium manufacturer not only expected a consistently excellent flavor. The plant was to achieve the lowest greenhouse gas emissions at high productivity. "How we would achieve this, we didn't know at the time," says Bengt Ove Bitnes Hagen. "Bühler showed that they could provide solutions for all our complex requirements and maintain the excellent flavor of our coffee. That's why we implemented the project with them as a full-service provider.” Bühler is seeing an increasing demand for such extremely low-emission coffee processing plants. “The fact that the first one, that of Joh. Johannson Kaffe, is currently proving itself in operational use is a sign for all industrial coffee producers," Daniel Egy, Head of Business Unit Chocolate and Coffee at Bühler, says. He estimates high energy savings from Bühler's technologies. "In the roasting process alone, our solutions allow energy savings of around 50%, which translates directly into lower production costs." The energy-intensive roasting process accounts for more than 70% of the total energy consumption of such a plant.
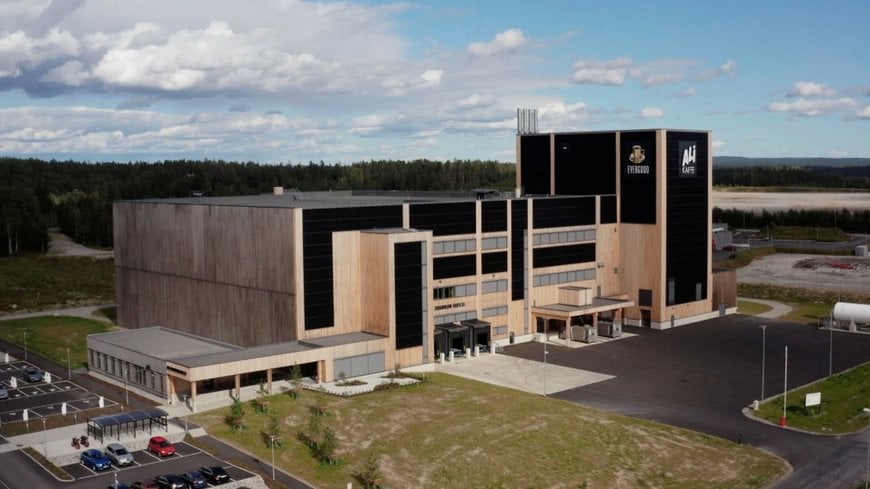
The reason for the extremely low emissions
Bühler supplies the entire processing technology: from green coffee intake to cleaning, blending, roasting, grinding, and including plant automation. At the heart of the coffee processing plant and responsible for the extremely low-emission production is the InfinityRoast with its green coffee preheating unit. At Joh. Johannson Kaffe, Bühler has combined this with a novel energy recovery system as well as an energy-efficient emission control system. The heat of the roasting process is recovered by heat exchangers which heat water up to 100 degrees Celsius which is then sent to accumulator tanks in an energy central. Most of the energy stored in this way is reused for the same roasting process and for preheating the coffee beans. The incoming cold air is also heated in this way. In addition, the planned plant has one of the most modern emission control systems for roasting systems by regenerative thermal oxidation (RTO). This process renders the plant's exhaust gases harmless by burning off organic matter. Excess energy stored in the accumulator tanks is used to heat the offices and laboratories or for other purposes in the building. The total balance of electric power required by the factory is covered by huge photovoltaic solar cells. At maximum capacity, the plant produces up to 12,000 tons of coffee per year.
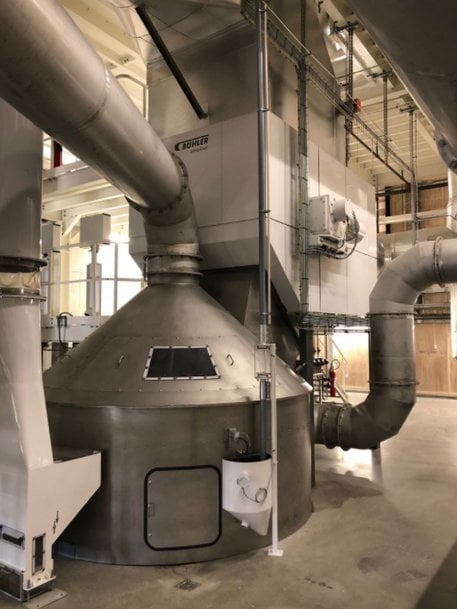
Highest quality, best flavor – also from the new plant
"We were able to give Joh. Johannson Kaffe confidence that they could reproduce their high quality and characteristic flavor in the new plant," says Daniel Egy. The InfinityRoast's auto-corrective, high-performance profile control system constantly modulates the energy input to the roasting chamber to ensure that the flavor develops exactly according to Joh. Johannson Kaffe’s quality specifications. A state-of-the-art process control system allows full product traceability. "From this plant, we supply our customers with outstanding coffee with excellent flavor – a premium product. The fact that we have reduced energy and CO2 emissions to an absolute minimum is a compelling selling point. In addition, we save energy costs and are therefore even more profitable," says Bengt Ove Bitnes Hagen.
www.buhlergroup.com