www.magazine-industry-usa.com
23
'13
Written on Modified on
Materials in design
Dieter Steudtner, Sales Manager at Morgan Advanced Materials, gives designers and manufacturers an insight into advanced ceramic materials and their properties.
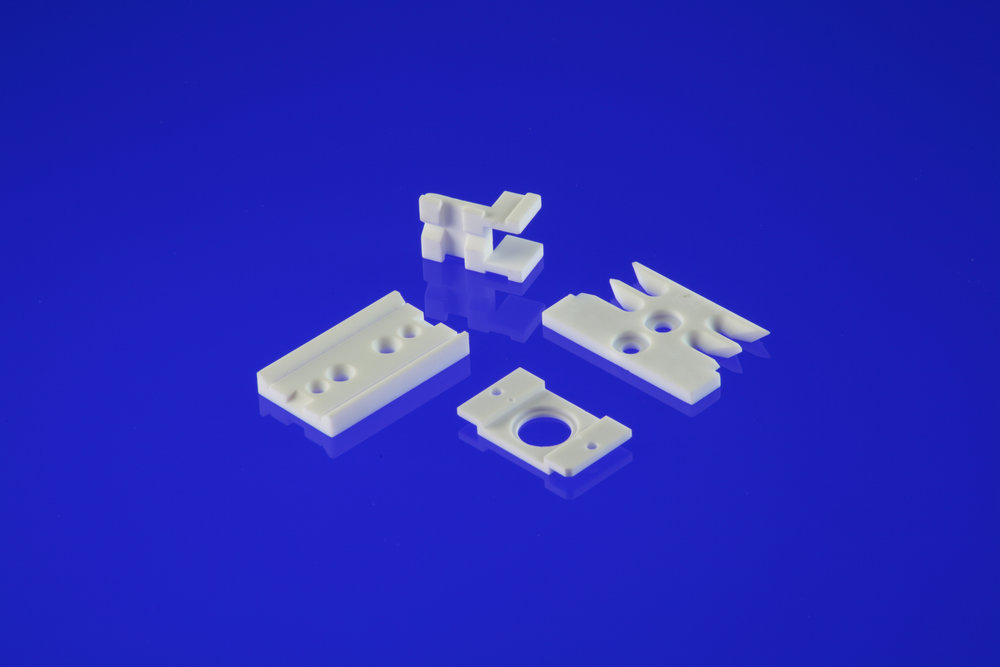
Advanced ceramics such as alumina, aluminum nitride, zirconia, silicon carbide, silicon nitride and titania-based materials, each with their own specific characteristics, provide a cost-effective, high performance alternative to traditional materials such as metals, plastics and glass. The demand posed by new and changing applications is to improve operation at a reduced cost. New materials are constantly being developed and engineered to address the needs of individual applications.
There are many factors that designers should consider when choosing a material including the desired properties for the application and the available materials. By fully understanding the materials, designers can then make well-informed choices. In particular when thinking about the shape, the design and the application of the part there are a lot of things to be considered in the early stages of engineering the parts. The shape of ceramic parts is often designed similar to metal parts. However this can have a negative impact on the cost and on the properties of the parts as well.
Joining of ceramics to metals also creates its own engineering challenges that require specialist expertise. Morgan Advanced Materials is a world leader in the metallisation and joining of ceramics. Its applications engineers have worked with customers all over the world to provide high-integrity solutions for components of all sizes, shapes and specifications.
Desired properties for the application
Physical properties such as strength, hardness, wear resistance, corrosion resistance and thermal stability are considered when choosing a material. Each of these characteristics is determined by specific materials; for a breakdown of materials and their characteristics see fig 1. Designers look for those materials which give the best combination of characteristics for an excellent performance.
Materials
Having identified the material properties needed for individual applications, designers should then consider the various ceramic materials available to them. A number of available ceramic materials are optimised for their mechanical, electrical, thermal and/or chemical properties. Examples are detailed below:
Alumina
Alumina is a versatile material that offers a combination of good mechanical and electrical properties. It is suitable for a wide range of applications including laser devices, x-ray tubes, electron tubes, aerospace devices, high vacuum applications, flow meters, pressure sensors, and wear components. It has a good strength and stiffness, good hardness and resistance to wear. Alumina is available in many grades ranging from 60% to 99.9% with additives designed to enhance properties such as wear resistance or dielectric strength. It can be formed using a variety of ceramic processing methods and can be processed net-shaped or machined to produce a variety of sizes and shapes. In addition it can be readily joined to metals or other ceramics using specially developed metallising and brazing techniques.
Aluminum Nitride (AlN)
Aluminum nitride (AlN) has excellent thermal conductivity. Other properties include excellent thermal shock resistance and corrosion resistance. Based on these properties AlN is used in power electronics, aeronautical systems, railways, opto-electronics, semiconductor processing, microwave and military applications. Typical applications include heaters, windows, IC-packages and heat sinks.
Zirconia
Zirconia offers chemical and corrosion resistance at high temperatures up to 2400°C – well above the melting point of Alumina. In its pure form, crystal structure changes limit use in mechanical/temperature applications, but zirconia stabilised with calcium, magnesium or yttrium oxide additives can produce materials with very high strength, hardness and in particular, toughness. Morgan is a pioneer in this area of materials technology, producing Magnesia Partially Stabilised Zirconia (Mg-PSZ) and Yttria Tetragonal Poly-crystal Zirconia (Y-TZP). These belong to the group of very high strength, toughness zirconias that harness the “transformation toughening” phenomenon unique to this material. They are suited to engineering or structural applications where exceptional mechanical strength and properties such as hardness, wear and corrosion resistance are required. 3Y-TZP is a similar product used primarily for medical implant applications.
Meanwhile, the high temperature capability of zirconia products has led to the development of Fully Stabilised Zirconia (FSZ) grades for crucibles, nozzles and other components for molten metal applications.
Silicon Nitride
Silicon nitride has excellent high-temperature strength, creep and oxidation resistance, while its low thermal expansion coefficient provides good thermal shock resistance when compared with most other ceramic materials. It has high fracture toughness, hardness, chemical and wear resistance, and is manufactured in three main product types: reaction bonded silicon nitride (RBSN), hot pressed silicon nitride (HPSN) and sintered silicon nitride (SSN). RBSN gives a relatively low-density product compared with HPSN and SSNM nitride types, because of this feature HPSN and SSN materials which are suited to for more demanding applications. Typical applications include: bearing ball and roller elements, cutting tools, valves, turbocharger rotors for engines, glow plugs, non-ferrous molten metal handling, thermocouple sheaths, welding jigs and fixtures and welding nozzles.
Silicon carbide
Silicon carbide is a highly wear-resistant material with good mechanical properties including high temperature strength and thermal resistance of up to 1650C. It has low density, high hardness and wear resistance and excellent chemical resistance. Its characteristics mean the material is ideal for applications such as fixed and moving turbine components, seals, bearings, ball valve parts and semiconductor wafer processing equipment. Other specialist applications include beams and profiled supports, rollers, tubes, batts and plate setters, as well as thermocouple protective sheaths.
Shape of the components
Having chosen the material, the first step is to consider is the shape of the final engineered component. There are certain shapes that will cause weaknesses in the component. Therefore, when designing and manufacturing with ceramic to give high performance, reliable parts with high strength it is best to keep the shape simple. For example, avoid sharp edges and corners, and sudden changes in cross section. .
Metallising/brazing
For many applications it is often necessary to join ceramic to metal to create the finished part. Ceramic-metal bonding is one of the biggest challenges that have faced manufacturers and users due to the inherent differences in the thermal expansion coefficients of the two types of materials. Various methods are available including mechanical fasteners, friction welding and adhesive bonding but by far the most widely used and effective method for creating leak-tight, robust joint between ceramic and metal is brazing. This starts with the chemical bonding of a metallisation layer on the ceramic to create a wettable surface upon which braze alloy will flow between the two components during the brazing process.
In order to achieve maximum bond strength, ceramic parts are typically metalized with molybdenum manganese (MoMn) and then plated with nickel (Ni). They are then ready for brazing and are generally assembled with metals that have very similar expansion properties as ceramic.
Morgan Advanced Materials manufactures WESGO braze alloys and supplies high-purity, low vapour pressure alloys, including precious metal filler materials, non-precious alloy filler materials and active braze alloys. Precious brazing filler metals are derived from gold, silver, platinum and palladium based materials and exceed the most stringent requirements imposed by the power tube, aerospace, semiconductor, medical, electronic and vacuum industries in which they serve. Non-precious alloy filler materials are ideal for applications including tooling for mining and heavy industry equipment. They are suitable for brazing applications between 500ºC and 1200ºC. Active braze alloys provide a single-step approach for joining ceramics to metals by eliminating the need for prior metallization of the ceramic surface, as the active components promote wetting. As it can be done in a single step it replaces metalizing, firing and electroplating and offers time and cost savings.
Co-fired assemblies
For specific applications, such as flow meters, a metal feedthrough can be produced by placing a wire in the ceramic in the pre-sintered (green) stage. As the ceramic shrinks during the sintering process, it compresses on the metal and forms a gas tight seal. This needs excellent knowledge and control about the sintering cycle temperature and careful selection of the metal.
Coating and glazing
The roughness of the final product depends on the grain size. If the grain size is large, then the product will have a rough finish and, after grinding, cavities could be formed. In order to achieve an excellent surface finish parts can be glazed. This is important if parts are to be exposed to dust or pollution. In this case, the glossy surface can be cleaned easily to avoid surface leakage and flashovers.
An advanced solution
In summary, many factors determine the material from which components are manufactured. It is most important to consider the application and the performance requirements based on thermal, mechanical, electrical and chemical properties. Ceramic materials’ hardness, physical stability, extreme heat resistance, chemical inertness, biocompatibility, superior electrical properties and, not least, their suitability for use in mass produced products, make them one of the most versatile groups of materials in the world.
As applications make greater demands on one or any combination of these properties, ceramics not only become the materials of choice, but in many cases, the only viable option in terms of materials that can survive in the extreme conditions of the application.
Advanced ceramics are meeting the needs for higher performance critical components in a wide variety of applications. Through a detailed understanding of the ceramic-metal bonding techniques such as the metallisation process and the advantages of glazing and coating, designers and manufacturers are becoming able to devise increasingly complex components.
For further information visit http://www.morganadvancedmaterials.com.
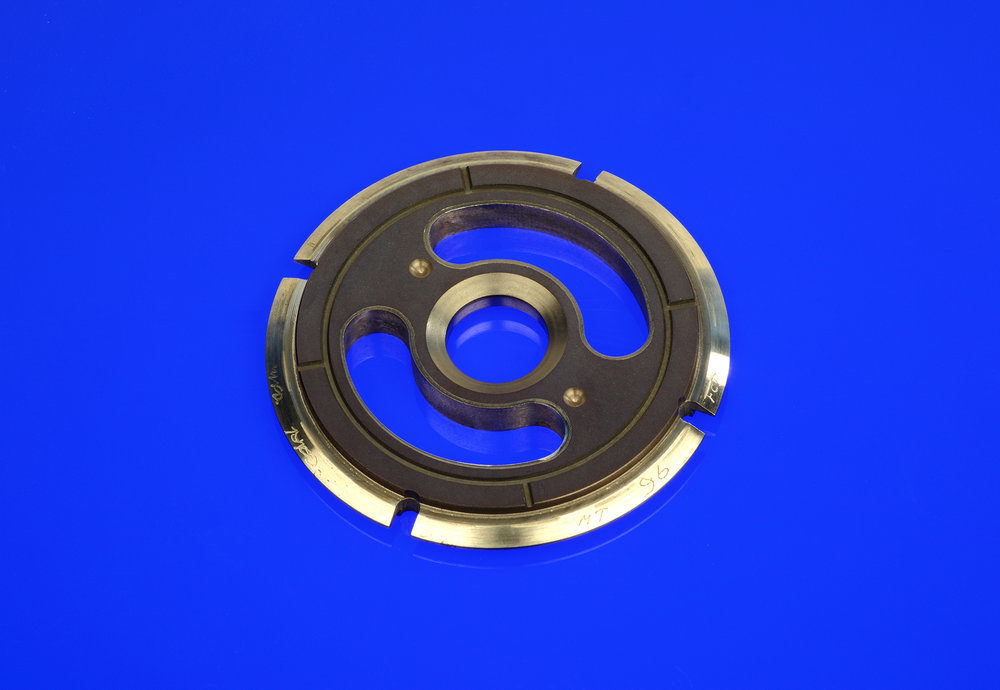

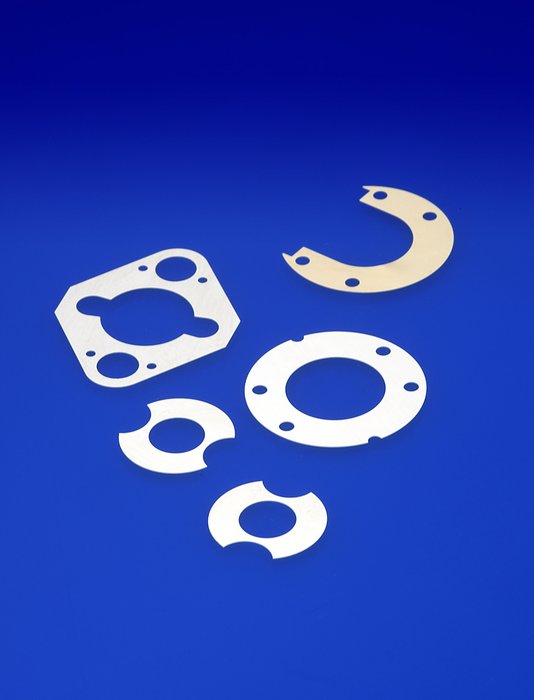
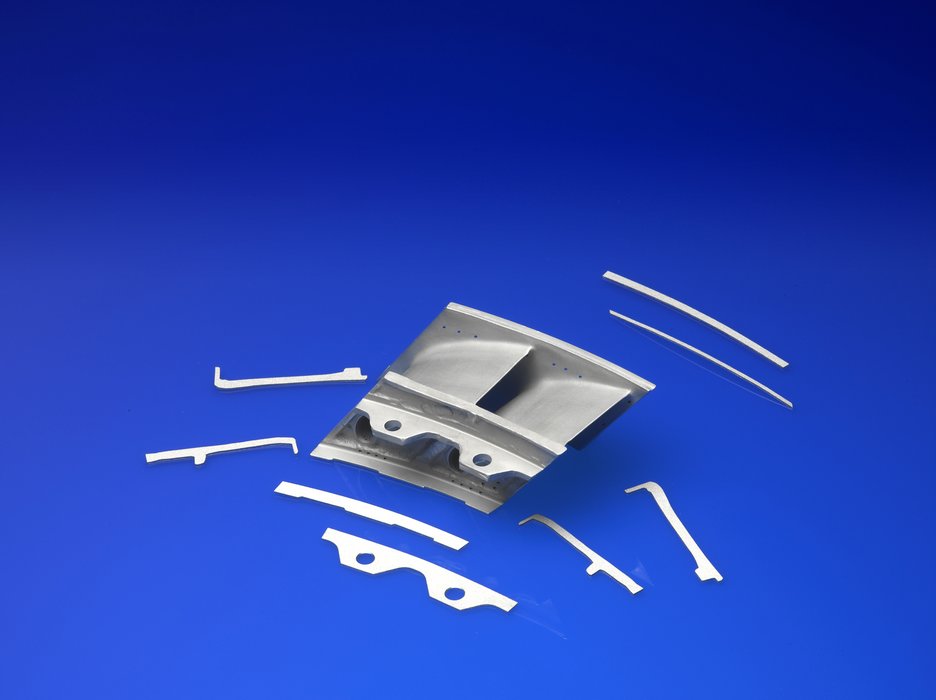