www.magazine-industry-usa.com
07
'13
Written on Modified on
Record-sized toothpaste production needs massive geared motors
EKATO, manufacturer of customized industrial agitators, has scaled up the largest model from its UNIMIX line to more than double the size, thereby implementing the largest discontinuous toothpaste production system in the world. Two mixers, each with 10,000 liters effective volume, produce 6,000 to 11,000 kg of toothpaste per hour, depending on the product concentration. Thus, the output has been more than tripled. The drive specialist NORD DRIVESYSTEMS supported the development of the new record-sized systems.
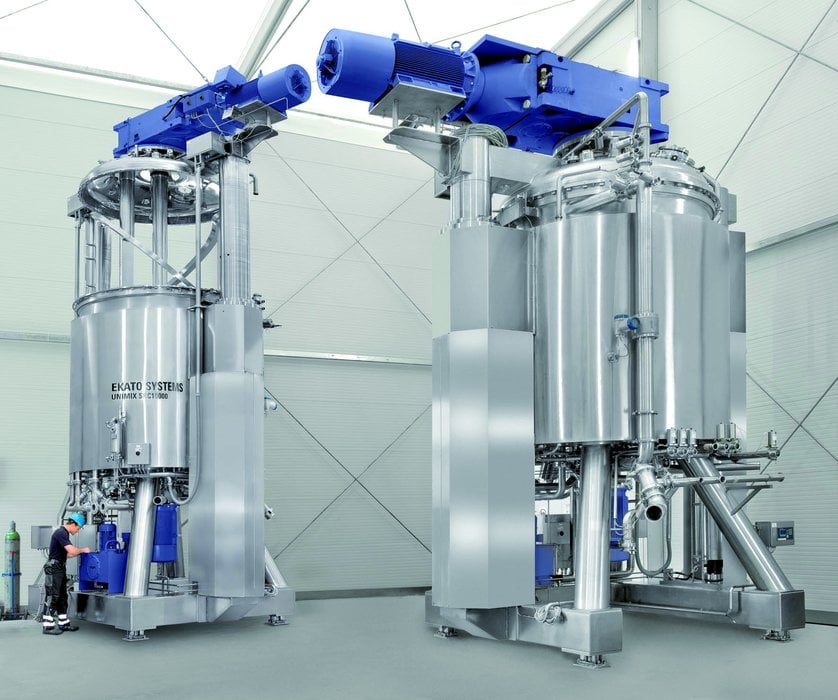
Illustration 1: The new UNIMIX systems, driven by NORD industrial geared motors: at a record volume of 10,000 l each, they form the world’s biggest plant for the batch production of toothpaste.
Many manufacturers with a global reach are interested in concentrating production capacities in just a few places. The hygiene and personal care industries certainly follow this trend. Accordingly, there is a demand for ever larger batch sizes for products such as toothpaste. Furthermore, a larger range of variants is produced at each site. Therefore, modern plants must be capable of producing large volumes while at the same time providing maximum versatility. With this complex task in its sights, EKATO SYSTEMS from Schopfheim at the southern reaches of the Black Forest has constructed a new plant for the discontinuous production of toothpaste.
The state of the art up until now
The maximal capacity of toothpaste production plants used to lie between 4,000 and 5,000 liters, with outputs of approximately 2,000 to 3,000 liters hourly. Continuous or batch production is possible. Continuous systems enable high throughput but are not very versatile with regard to product changes; since different ingredients sometimes require their own dispensing and blending technology, recipe changes often bring about conversions and readjustments. It also comes into play that toothpaste cannot easily be reworked when it is not sufficiently homogeneous. The biggest challenge with continuous plants is ensuring the uniform dispersion of active ingredients such as sodium fluoride, even after changes to the dispensing systems. On the other hand, the production rate of existing discontinuous plants cannot be significantly increased without major modifications in plant equipment. In order to meet the demands of a toothpaste manufacturer, EKATO therefore had to construct larger plants.
Production mixer design
Toothpaste production systems basically consist of an evacuable vessel with an agitator, a homogenizer, and various dispensing systems for the introduction of ingredients into the process. Liquid ingredients are either measured and then vacuum-inserted into the vessel or dispensed by gravimetric methods. Powders and thickeners to increase viscosity can be added via the integrated homogenizer or drawn into the vessel through a valve at its base.
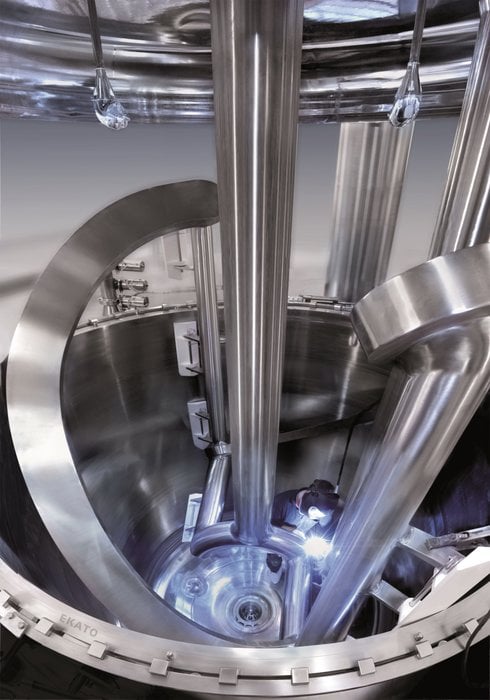
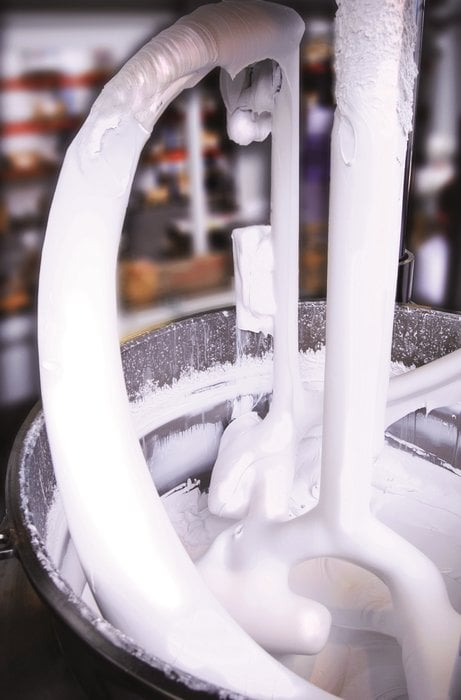
Illustration 2, 3: EKATO constructs the perfect agitator for each product.
Complex calculations for the scale-up
For larger mixer dimensions, EKATO had to determine the components’ dosage and dispersion times, blend and homogenization times, vacuum values, and the necessary agitator and homogenizer performances. The agitator and homogenizer were configured according to the mixing performance equation for mixing technology. Based on its extensive experience, EKATO determines the power coefficient “Ne” (or Newton number) for each respective impeller and the product’s specific viscosity curve. In addition to the product concentration, the equation furthermore contains the speed and the diameter – with the exponents 2, 3, or even 5, these values are especially important. That is why the correct configuration of the agitator and homogenizer drives is crucial. The drive supplier NORD was required to configure motors and gear units with the performance according to EKATO’s calculations, and to make them as efficient and durable as possible. Since the agitator drive is installed on top of the production mixer, it should be as compact as possible despite the high performance required.
Agitator drives as large as a city car
This application, which depends on homogeneous product quality, calls for speed and continuity. The radial and axial loads on the agitator shaft, which are very high due to the high product viscosity, must be taken into account for the drive configuration. NORD DRIVESYSTEMS configured and supplied two 250 kW motors with industrial gear units which provide nominal output torques of 242,000 Nm. NORD is the only manufacturer worldwide to produce such extremely large industrial gear units in this power range in the proven one-piece UNICASE housing. Hence, the type SK 15407 3-stage helical bevel gear units, though of an impressive size, are still relatively compact as the UNICASE design allows for larger rolling bearings which can accommodate higher forces.
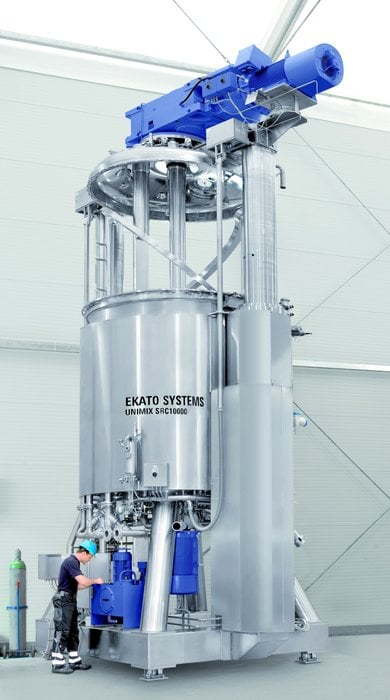
Illustration 4: The geared motors from NORD DRIVESYSTEMS meet the standard set by the record-sized plant: no other drive manufacturer is currently capable of producing industrial gear units of this size in a one-piece housing.
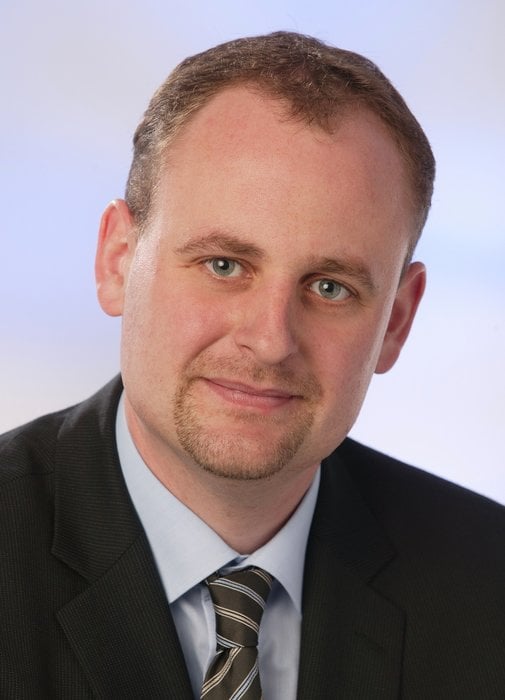
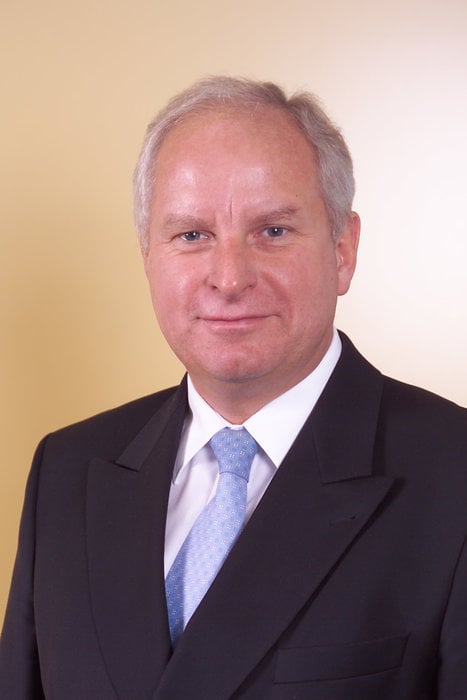
Illustrations 6, 7: The authors are Alexander Lukas (left), Head of Research & Development at EKATO SYSTEMS, and Peter Dittmers (right), Managing Director Germany, NORD DRIVESYSTEMS.
Authors:
Alexander Lukas, Head of Research & Development at EKATO SYSTEMS, and
Peter Dittmers, Managing Director Germany, NORD DRIVESYSTEMS