www.magazine-industry-usa.com
03
'13
Written on Modified on
Arnold Umformtechnik: aluminium replaces steel
Alufast® screws suitable for series production – Substantially lower weight than steel screws – Mitigate problems with bolted joints in magnesium parts
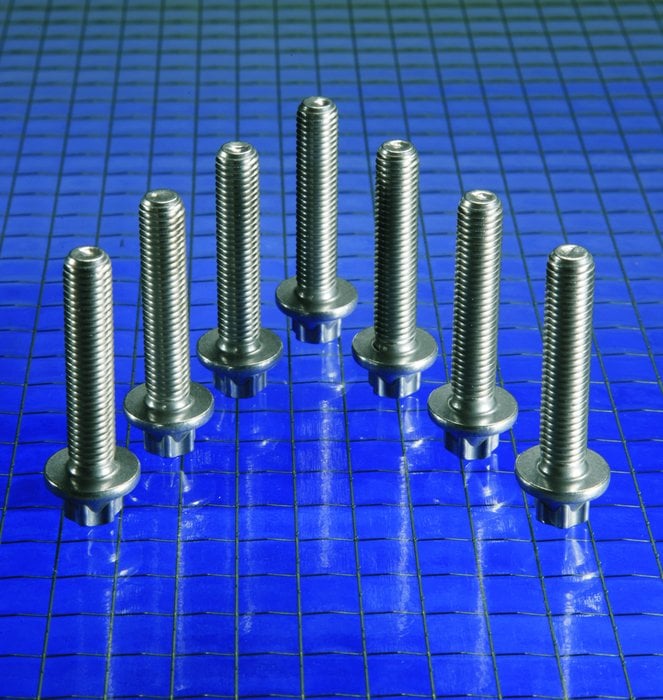
A weight advantage of around 350 grams versus comparable steel screws makes Alufast® screws an attractive option for designers of transmission housings and other applications. According to the results of an engineering study by joint specialists at Arnold Umformtechnik, this weight reduction can be achieved for each transmission in an application with 20 screws per transmission unit. With an annual production volume of 100,000 transmissions, for example, that add up to some 35 metric tons of steel per year.
The Alufast® fastener family also scores well for use in joints subjected to high thermal stress in a corrosive environment. Alufast® components exhibit especially good characteristics under thermal stress. The mechanical properties of the screws remain stable in the presence of long-term stress at peak temperatures up to 150 degrees Celsius.
In contrast to steel screws, designers can use standardised bearing surfaces for bolted joints in magnesium parts. The screws reliably achieve strength and strain figures in the production environment while exhibiting good corrosion resistance.
Alufast® screws feature higher residual clamping force after thermal cycling than steel screws in bolted joints for magnesium parts. Last but not least, Alufast® screws yield cost savings of 20 to 50 per cent compared to steel screws with additional corrosion protection treatment.