www.magazine-industry-usa.com
30
'13
Written on Modified on
Superwool® Plus Blok - New tests reveal most energy-efficient solution for kiln linings
Tests carried out by Morgan Advanced Materials, a leading manufacturer of engineered products for a range of thermal insulation applications, have revealed the company’s latest Superwool® Plus Blok insulation offers significant performance advantages over other materials in the area of thermal insulation for kiln linings.
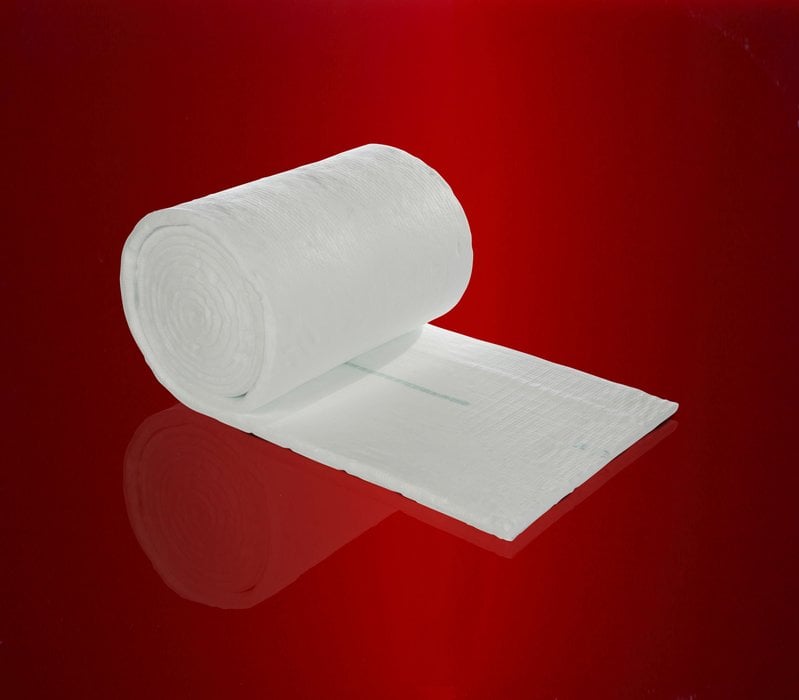
The tests, carried out at the group’s world leading Research and Development facility, involved the use of 25mm thickness Superwool® Plus Blok 800 with a bulk density of 342.7kg/m³ and a calcium silicate board of the same thickness with a bulk density of 244.2kg/m³. Using Batfix G glue to affix layers to the desired thickness, a small laboratory furnace was lined with each of the products. Before the tests, the boards were dried at 300°C for 15 hours and then two test firings were conducted at each of four temperatures, 600°C, 800°C, 900°C and 1,000°C. The temperatures were reached at a rate of 3°C per minute and the test temperatures were then maintained for 15 hours. EMU electronic equipment was used to measure the energy usage throughout the test.
The tests indicated that it took approximately the same length of time for the benchmark temperatures to be reached with both products, but the energy used was lower with Superwool® Plus Blok 800 at each level. Similarly, when the furnace ran for the 15-hour period, energy consumption was lower with the Superwool® Plus Blok 800. In fact, at 600°C, the calcium silicate product used 12% more energy, at 800°C it used 20% more and at 900°C and 1,000°C the difference was around 16%. The test also revealed that the calcium silicate board was fragile and not flexible, while the Superwool® Plus Blok product was easier to cut and manipulate.
The difference in energy consumption is accounted for by the difference in thermal conductivity - the ability of the material to restrict the flow of heat from the furnace to the external environment. Heat loss is dominated by infra-red radiation and in a fibrous insulation material, the greater the number of fibres, the more effective the insulation will be. The latest Superwool® Plus Blok fibre-based boards combine high-specification low-biopersistent fibres, fillers and organic binders to deliver significantly reduced thermal conductivity.
Ermanno Magni of Morgan Advanced Materials explained: “Superwool® Plus Blok 800 offers a range of benefits – it is simple to cut and shape, offers optimum flexibility and is treated with a water repellent that eliminates the need for a separate vapour barrier, reducing costs. However, perhaps its most significant advantage is in the area of thermal conductivity.
“The high cost of energy combined with government pressure on industry to meet carbon reduction targets is increasingly influencing purchasing decisions. When specifying insulating materials for back-up lining in kilns and furnaces, the initial cost should only be part of the equation. Designers and specifiers should look for the products that will deliver optimum long-term performance and return on investment. Thermal conductivity has a direct impact on long-term cost and energy efficiency and the latest generation of low-biopersistent fibre-based boards offer enhanced energy-saving properties. These advantages far outweigh the modest cost premium associated with Superwool® Plus Blok.”
Strong, lightweight and thermally shock-resistant, Superwool® Plus Blok is available in three grades – 800, 1000 and 1100. These numbers directly relate to the maximum continuous use temperature for each product, meaning grade 800 panels can be used in continuous applications up to 800ºC, helping to ensure appropriate selection based on temperature requirements.
The product is available as a standard sheet size (1000mm x 600mm), with thicknesses between 25mm to 50 mm. Greater thicknesses can be achieved by bonding together two thinner sheets during production.
For further information, visit www.morganthermalceramics.com.