www.magazine-industry-usa.com
24
'20
Written on Modified on
Manufacturers Urged To Consider Best Practices For Optimizing Control Plans With AI
While every factory process is unique, a number of best practices will generally apply when implementing Artificial Intelligence (AI) for process control, according to DataProphet, a global leader in AI for manufacturing.
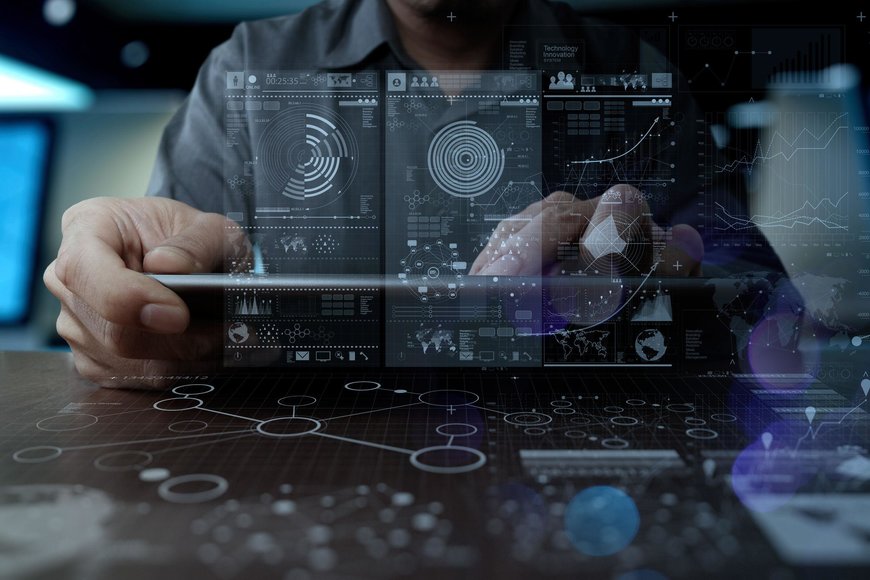
Below, Joris Stork, one of DataProphet’s senior Data Scientists, has identified three key principles that will help manufacturers to maximize the success of their process optimization projects with AI. As part of a digital transformation strategy, they will help manufacturers to navigate the complexity of their Industry 4.0 investments.
1. Select a proactive and holistic AI solution
Holistic process models capture the complexities of a system, including interactions between process parameters, higher-order effects, interdependencies along a chain of processes, and the physical constraints within which processes must operate.
Crucially, a holistic digital twin of the process can proactively avoid non-quality before it happens. This type of end-to-end process model is able to guide the production line along a viable path of improvement towards an optimal operating region. Where traditional solutions typically alert manufacturers to known bad process conditions, a proactive model will predict and avoid defects before they even arise.
2. Augment human expertise with machine learning
Traditional process optimization technologies extract narrow insights for analysis by specialised process engineers. These engineers in turn produce control plans, which guide operators’ adjustments to process parameters. A well-designed factory AI captures the history of these adjustment choices as well as their effects. In doing so it captures and stores the past and present experience and expertise of factory specialists . Incorporating the AI into machine operators’ workflows, in what is known as a “human in the loop” design, empowers those operators to make optimal process adjustments without the need for extensive analysis. In addition to augmenting the human operator with a well of accumulated experience and expertise, this approach adds a layer of human validation and cultivates greater trust in the AI system.
3. Optimize continuously
Factory processes are not stationary. The design of an AI optimization system needs to reflect this reality. The system must continuously optimize as conditions change, due, for example, to upstream changes on the line, or due to machine wear.
DataProphet’s PRESCRIBE is an Expert Execution System (EES) designed with this reality in mind. Through its intelligent web interface, technicians can view up-to-date optimization reports that are relevant to their particular process at any time.
PRESCRIBE works to achieve zero defects in the production process, using advanced predictive and prescriptive machine learning capabilities to predict defects, faults, and quality errors, and then to prescribe optimum control parameters that improve production.
Every manufacturing process is different, but by following these best practices, businesses across a range of industries can realize significant savings in production costs and reduce waste when they optimize their processes with AI.
For more information, please visit: https://dataprophet.com/prescribe/