www.magazine-industry-usa.com
26
'12
Written on Modified on
Kennametal Extrude Hone™ announce HYDROM™, the ADD
ON Electrolyte Cleaning Unit
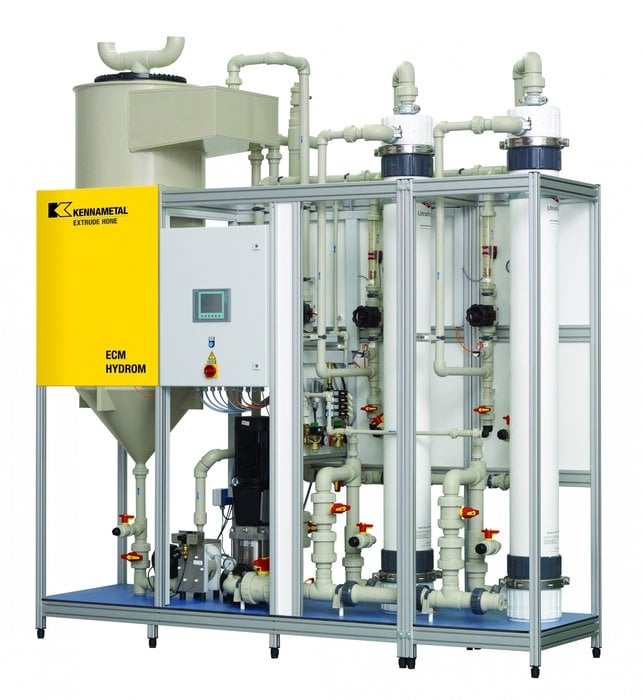
Electrochemical machining accomplishes metal removal by the dissolution of surface atoms without direct contact between the tool and workpiece material. The amount of material removed is proportional to the time and intensity of an electrical current flowing between tool and workpiece. The process is highly controllable and can machine or polish areas previously unreachable by other methods, including hand polishing and deburring.
As an electrolytic solution (water and specialized salts) flows over the workpiece surface, a DC current is applied between the tool and the workpiece. The amount of material removed is determined by the amount of electrical current flowing between the negatively charged tool and the positively charged workpiece. The tool is normally designed to have a mirror image of the final surface of the workpiece. Since the tooling, known as a cathode, never touches the workpiece, there is virtually no tool wear in the process. Typical deburring and polishing times are extremely fast – between 10 and 30 seconds for most applications. Depending on production requirements and the workpiece size, multiple part fixturing can be used to obtain high production rates.
Now making the process even more effective is the HYDROM add-on cleaning unit. Combine HYDROM with a CFP – chamber filter press -- and reduce disposal costs on filter cake by up to 10%. CFP cleaning time can be reduced by up to 6x, and cathode tool life is extended. Accordingly, machine availability increases.
HYDROM can be delivered with new ECM equipment but also as an add-on to existing machines of all brands. For complex machining and finishing, HYDROM will help companies increase competitiveness and improve quality and productivity in cost-pressured manufacturing markets.
For more information, visit http://www.kennametal.com/extrudehone