www.magazine-industry-usa.com
30
'12
Written on Modified on
New application limits for torque limiting clutches
Perfect torque limiting clutches for test stands
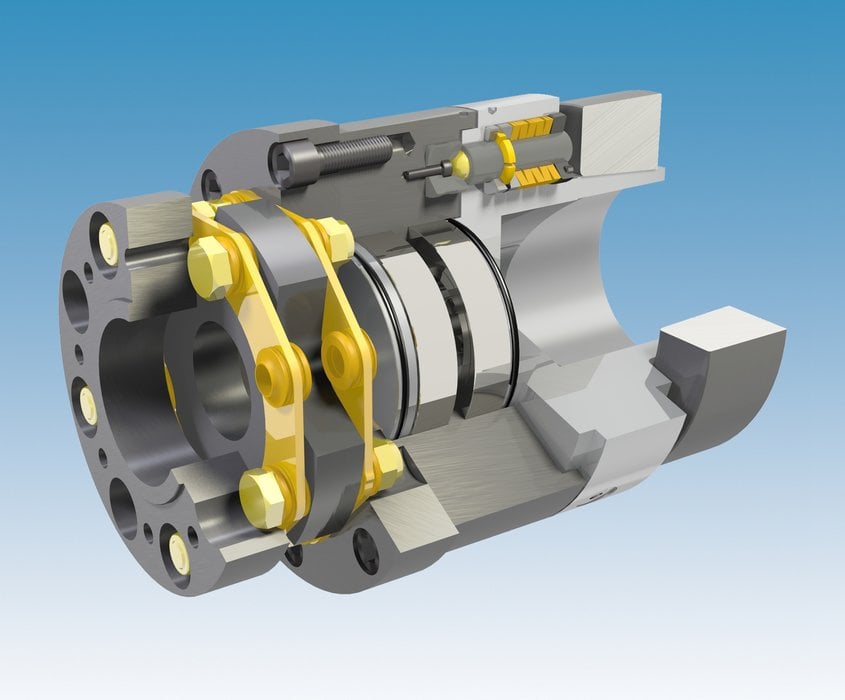
As worldwide market leaders, mayr® power transmission has offered the widest range of products in load-holding, load-separating, torque and force-limiting, frictionally locking, positive locking, magnetic, controllable and switchable torque limiting clutches for decades. Despite this extensive selection, the company permanently records demands from all different branches for new, application-optimised torque limiting clutches, as the standard type series available on the market are unable to fulfil the increased demands optimally.
Test stand technology is one of these application areas. Here, torque limiting clutches must primarily be suitable for extremely high speeds. Furthermore, they must be able to transmit the torque in a backlash-free and torsionally rigid manner. In case of malfunctions, protection of the high-quality systems must be guaranteed. When dealing with high speeds, the only expedient option is a residual torque-free separating (disengaging) torque limiting clutch, so that in case of overload, the rotational energy stored in the uncoupled masses can slow down freely.
With the type series EAS®-HSC and EAS®-HSE, mayr® power transmission has developed new torque limiting clutches tailored for the extreme demands of test stand technology. Both construction series are based on tried and tested design principles, which have proven their worth for decades.
The basic prerequisite for the application of a torque limiting clutch in high-speed applications is, among other things, a high balance quality in each individual component, in order to reach optimum running smoothness of the drive line on combination of the components. When speeds increase, imbalances cause substantial centrifugal forces and vibrations. This puts a strain on the entire test stand construction, leads to uneven running and falsifies the test results of the measurement devices. Therefore, optimising the mass imbalance was a top priority in the development of the new high-speed clutches.
In comparison to the standard torque limiting clutches available on the market, the new test stand clutches EAS®-HSC and EAS®-HSE provide numerous technical features. At first glance, the extremely compact design of the clutches is noticeable. The high performance density reduces the rotating masses and has a positive effect on the running smoothness and the machine dynamics.
Torque limiting clutches consist of many individual components, which must not change their positions within the clutch in mounted condition and also in case of overload. This is guaranteed through certain design features. Furthermore, the clutch is balanced in completely installed condition to a balance quality of G2,5, reference speed 3000 rpm.
In order to guarantee that the completely installed torque limiting clutch, which is set to the respective torque and balanced, also provides the required balance quality after integration into the customer system, the joint clearance between the customer shaft and the clutch bore is minimised. The clutch bores are designed in quality 6 in the standard series. Furthermore, the frictionally locking shaft-hub connection guarantees backlash-free torque transmission.
External reaction forces which have an effect on the output flange of the high-speed clutches are absorbed by a high-quality clutch bearing, and therefore do not influence the disengagement mechanism. The precise torque limitation remains intact. In case of blockage of the drive line, the torque limiting clutch disengages instantly. The input side to output side of the EAS-High Speed is accelerated extremely quickly. The high-quality clutch bearing is designed to absorb these accelerations.
After overload occurrence, too, the position of the individual components to each other must not change. On clutch disengagement, the input and output are rotated in relation to one another. Therefore, it must be guaranteed that the initial position is re-established after re-engagement. That is why the new test stand clutches are disengaging, with synchronous re-engagement.
On the EAS®-HSC, the torque in normal operation is transferred via balls which engage simultaneously into the grooves of the hub and the output flange. Cup springs pre-tension the balls via a ring. The amount of spring force is proportional to the transmittable torque. This principle also remains backlash-free in case of wear on the grooves. mayr® power transmission uses cup springs with falling characteristic curve in their torque limiting clutches. This means that the torque is transmitted torsionally rigidly until the pre-set disengagement value is reached. In case of overload, the spring pre-tension force is reduced, and the clutch disengages precisely.
After disengagement, a special disengagement mechanism ensures that the clutch remains disengaged. The drive line can slow down freely. During the stopping time, there are no engagement impacts, which might have a negative effect on the drive line, in particular on the torque measurement device. The torque transmission unit is designed so that re-engagement is only possible at the disengagement position. This means that the individual components of the clutch always have the same angular position to each other during operation, and the balance quality is maintained. The special disengagement mechanism enables easy, fast re-engagement without major expenditure of force.
On the EAS®-HSE, individual overload elements transmit the torque via positive locking. In case of overload, these overload elements disengage and separate the input and output almost residual torque-free with high switch-off and repetitive accuracies. The kinetic energy of the rotating masses, which is stored in the system, can slow down freely. The elements do not re-engage automatically. They remain separated until they are re-engaged manually or via a device. The position for synchronous re-engagement to maintain the balance quality is clearly marked on the clutch.
The new test stand clutches are supplied in flange design for the attachment of customer-side elements or with torsionally rigid single-jointed or double-jointed disk pack couplings. In addition to the classic connection of 2 shafts, mayr® power transmission offers adaptor flanges for the direct integration of standard measurement flanges. This enables extremely compact overall designs.
The EAS®-HSC type series covers a nominal torque range of 5 to 1,000 Nm with 5 construction sizes. Depending on the size, speeds of 6,000 to 12,000 rpm are permitted. For the EAS®-HSE type series, 3 sizes for torque values of 500 to 5,700 Nm have been realised up to now. Plans have been made for four additional sizes. The complete type series will be able to cover torque values of 300 to 25,000 Nm and speeds of up to 16,000 rpm.
Due to their characteristics, the new torque limiting clutches EAS®-HSC and EAS®-HSE are not only suitable for test stands, but are also the perfect solution for all other high-speed drive axes.
Product figures
Fig. 1
File: F-5-40-Bild1.jpg
On the test stand clutch EAS®-HSE, individual overload elements transmit and limit the torque. The torque can be varied greatly via the number of elements and the layering of the installed cup springs.
Fig. 2
File: F-4-19-Bild3.jpg
Disengaging, backlash-free EAS®-torque limiting clutch in combination with a backlash-free ROBA®-DS all-steel disk pack coupling, installed into a test stand at ThyssenKrupp EGM, Langenhagen.